Operation requirements, Warning – Liquid Controls MS Meters User Manual
Page 11
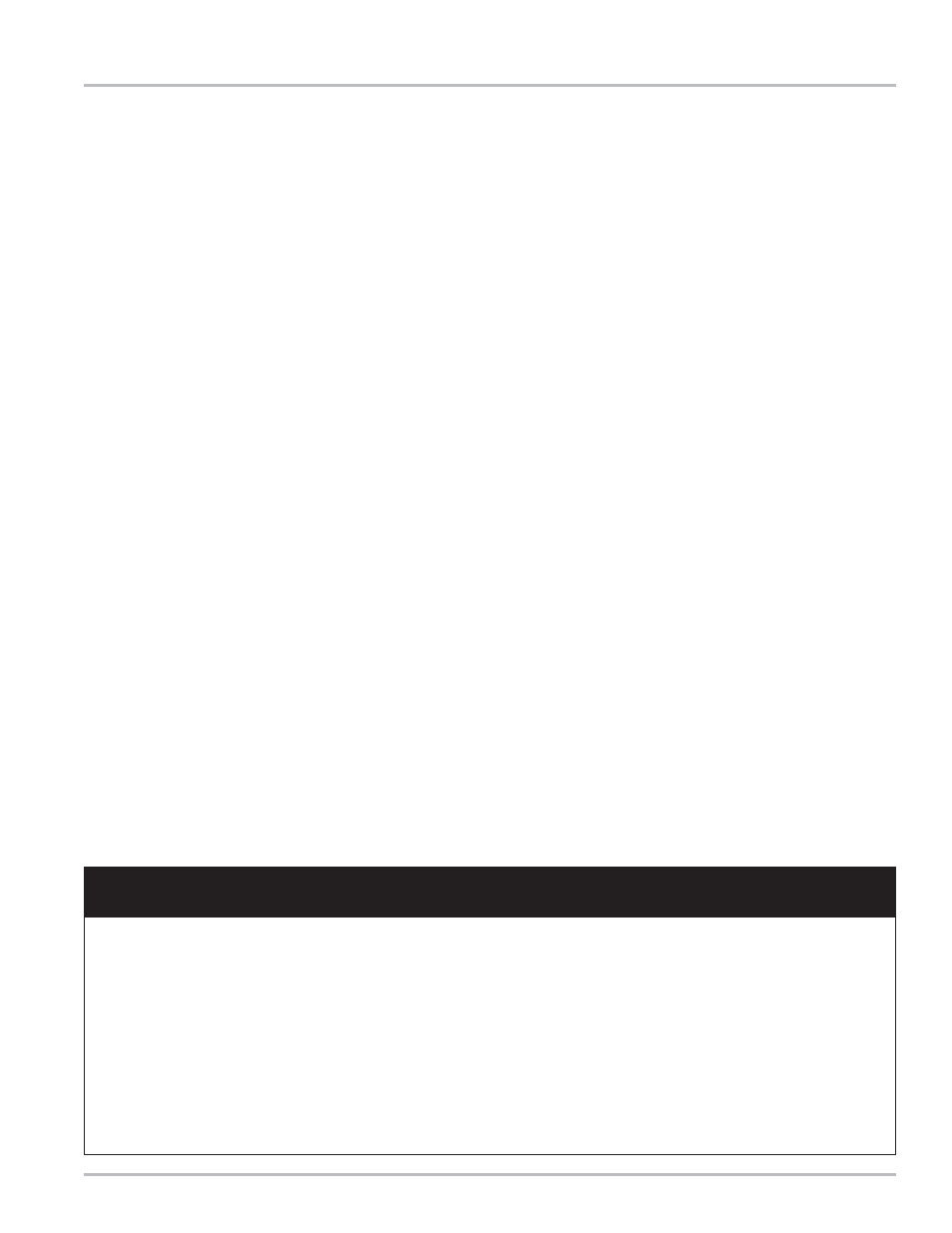
11
Operation Requirements
The meter must remain full of product at all times.
An easy way to accomplish this is to put the meter
assembly in the line below the piping center-line (a sump
position). This requires adding elbows and flanges prior
to installing the meter. The meter should be installed with
a bypass loop, below the pipe center-line, with block
valves upstream and downstream. A block valve should
be located in the mainstream, labeled as the bypass
valve. A word of caution: any portion of pipe system
that might isolate or block flow should be provided with a
pressure relief to prevent damage from thermal
expansion. There are excellent benefits to this type of
installation. First, the meter is kept full. Second, this type
of installation allows the meter to be isolated for servicing
and calibration while continuing flow through the bypass
valve.
Upstream lines must be maintained full to prevent air
from entering the meter. If the upstream or inlet lines are
constructed in a manner which allows reverse flow, foot
valves or back checks must be installed.
NOTE: Use soft seats, not cast iron swing checks.
Every meter should be calibrated under actual service
and installation conditions per the API Manual of
Petroleum Measurement Standards:
Chapter 4: Proving Systems
Chapter 5: Metering
Chapter 6: Metering Assemblies
Chapter 11 Section 2.3: Water Calibration of Volumetric
Provers
Chapter 12 Section 2: Calculation of Petroleum
Quantities
These chapters of the API Manual of Petroleum
Measurement Standards supersede the API Standard
1101.
Provide a means of conveniently diverting liquid for
calibration purposes.
Give careful attention to your system’s pumping
equipment and piping because of their influence on
liquid being measured as it enters the meter assembly.
Systems should be made free of conditions that cause
or introduce entrained air or vapor.
Follow the manufacturer’s recommendations fully
when installing pumps. Give particular attention to
factors like: use of foot valves, pipe size to the inlet and
conformance to net positive suction head (NPSH)
conditions when suction pumping is required. Following
the manufacturer’s recommendations will minimize air
and vapor elimination problems.
For all products, it is desirable to use flooded suctions
and piping sized larger than the normal pump size.
Hydraulic shock is harmful to all components of an
operating system including valves, the meter and the
pump. In particular, meters must be afforded protection
from shock because of their need to measure with high
precision. Generally the best protection is prevention,
which can be readily accomplished by adjusting valve
closing rates in such a manner that shock does not occur.
Shock pressure and system pressure are independent
of each other.
Thermal expansion like hydraulic shock is a
phenomenon that can easily damage meters and
systems in general. Care should be taken in designing
the system to include pressure relief valves in any portion
or branch of the system that might be closed off by closure
of operating valves or block valves. Note that 1°F is
equivalent to an increase amount depending on the
product in the system (70 psi for LPG).
!
!
!
!
!
WARNING
Under normal operation, do not expose any portion of the LP-Gas system to pressures in excess
of rated working pressures without an automatic safety valve to vent the over pressure discharge
to a place of safety away from the operator and other people. Failure to provide such a safety
relief may result in leakage or rupture of one or more of the components in the system. This can
result in injury or death from the gas, a fire, or pieces of flying debris from the rupture.
When a Back Check Valve is used, an automatic safety valve must be installed to prevent pressure
buildup (thermal expansion) in excess of rated working pressure in the meter housing. One
automatic safety valve should be installed in each meter. Remove the pipe plug from the front
cover or rear cover and insert the appropriate automatic safety valve.