Ecu connection, Telemetry – MoTeC ADL2 EDL2 User Manual
Page 23
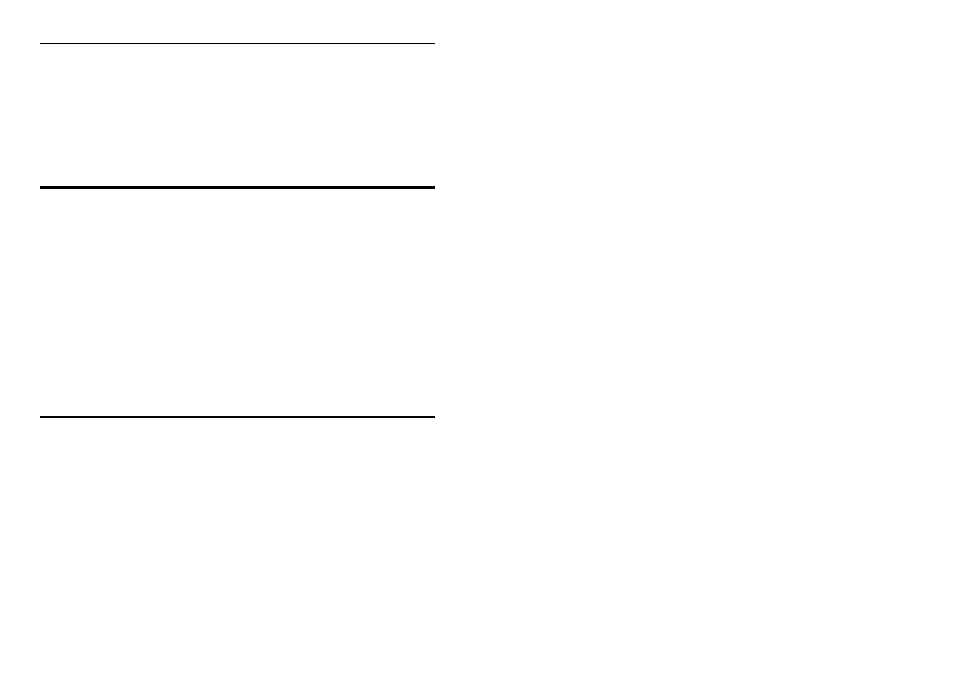
MoTeC
Overview
21
connected devices to communicate with each other, also the CAN port
communicates at very at high speed.
Other MoTeC products that use CAN for intercommunication include the
M800, BR2, PLM and MDD.
Note that these devices communicate at 1Mbit/sec, so any other devices
connected on the CAN bus must also communicate at 1Mbit/sec.
ECU Connection
The ADL2 can be connected to most Engine Management Systems (ECUs).
This avoids duplication of sensors and allows the ADL2 to display and log
many ECU parameters.
The ECU may send up to 40 values to the ADL2. The update rate of these
values depends on how many values are transmitted, the communications
baud rate and if sent using CAN or RS232. For RS232 the typical update rate
is about 20 times per second and for CAN it is about 50 times per second.
Note that logging the ECU values faster than these rates is unnecessary and
will reduce the total logging time.
• Note that if the ADL2 is connected to a MoTeC M800 ECU the M800
sensors should be calibrated in metric otherwise special scaling will be
required.
Telemetry
The ADL2 can transmit real time and/or end of lap telemetry data. This allows
monitoring of the current vehicle condition, position on the track, lap times,
fuel remaining, laps remaining etc.
The real time telemetry data is transmitted continuously.
The end of lap telemetry data is transmitted at a specified time after the lap
beacon is detected
• Note that if RS232 ECU communications is used then the telemetry baud
rate must be the same as the ECU communications baud rate (normally
9600 or 19200 baud)
• Note that the Telemetry option is required.