Franklin Fueling Systems ATG Moormann Interface User Manual
Page 7
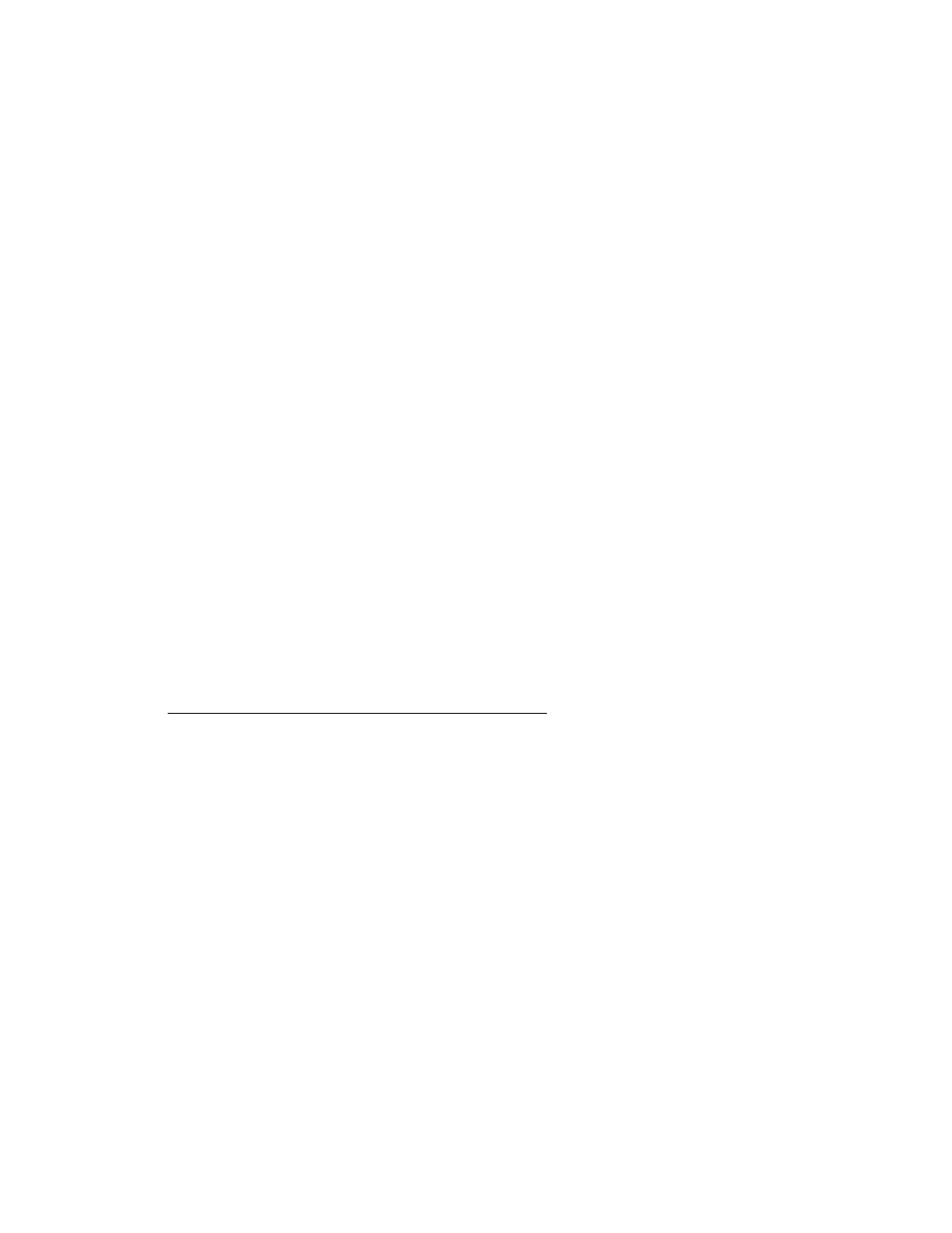
23. Remove the vice grips and electrical tape, and slowly allow the counterweight assembly to drop down in the gauge
tube. Once the weight assembly is on the bottom of the tube and the tape is slack, thread the loose end of the tape
through the short nipple on the tank top and fish this end out of the manhole access.
24. Fasten the tape clamp (Figure A, Item 3) to the float (Figure A, Item 2) using a cotter pin with a flat washer at the head
of the probe. Measure down to the product level and obtain an estimate of the dimension from the roller elbow to the
product level. Thread the free end of the gauge tape through the float tape clamp as shown in Figure A. Slide the
clamp up the tape to a point where the distance to the roller is at least 6" shorter than the dimension obtained to the
liquid level. Do not cut the tape excess at this time. Tighten the clamp only enough to prevent the tape from sliding
because a final adjustment will be necessary later — over-tightening at this time will damage the tape.
25. Lower the float assembly into the tank (
do not drop it) and carefully continue feeding the tape in until the float rests
on the product or on the tank bottom. FFS suggests that a small hand line be temporarily attached to the float bracket
to assist in this initial float installation. If there is slack remaining in the gauge tape, the float tape clamp will need to
be readjusted up the free end of the tape an additional amount to remove slack in the tape.
26. At the gauge tube window (Figure A, Item 1) reach in with a small screwdriver and place the outside tape strand
over the tape guide at the window. Be careful not to bend the tape or hook more than one tape strand. Install the
observation window pointer to the tape guide and adjust it to the middle of the range.
27. Measure the level of the liquid in the tank for an initial level gauge alignment. If the tank is empty, the initial level will
be 1⅜" (minimum float drift).
28. Read the actual gauge level at the site window of the gauge tube.
29. Visually inspect and determine the difference between the gauge readout and the actual tank level.
30. Remove the gauge float from the tank by extracting it through the manway with tape or a previously attached hand
line.
31. Mark the gauge tape where the float tape clamp is currently located. If the gauge reading was higher than the actual
tank level, slide the float tape clamp up the gauge tape from this initial mark the exact amount of the difference
between the two readings.
Example: Tank Gauge Reading:
15' and 9¾"
Actual Tank Level Reading:
– 14' and 3½"
Difference:
1' and 6¼"
Move float tape clamp up the tape:
1' and 6¼"
If the gauge reading was lower than the actual tank level, slide the float tape clamp down the tape a distance equal to
the difference between the two readings.
32. If you are uncertain that your adjustments are correct or if the initial adjustment was large, then repeat Steps 23, 24,
26, 27, 28 and 29 before proceeding.
33. Tighten the tape clamp to a point where the tape is deformed by the clamp’s dimples. Remove the small hand line
attached for float removal, and cut off any excess tape below the float tape clamp. Carefully reinstall the float into the
tank and lower it to the product level. Inspect the tape for twists or kinks and carefully remove any if they are found.
34. Install probe cable (Figure A, Item 21) to the connector on the top of the probe. Insert this wire through the hole at the
top of the weather head (Figure A, Item 22) and slide the weather head onto the head of the probe (see installation
guide 000-0113).
3