Quick-pwm design procedure – Rainbow Electronics MAX17008 User Manual
Page 28
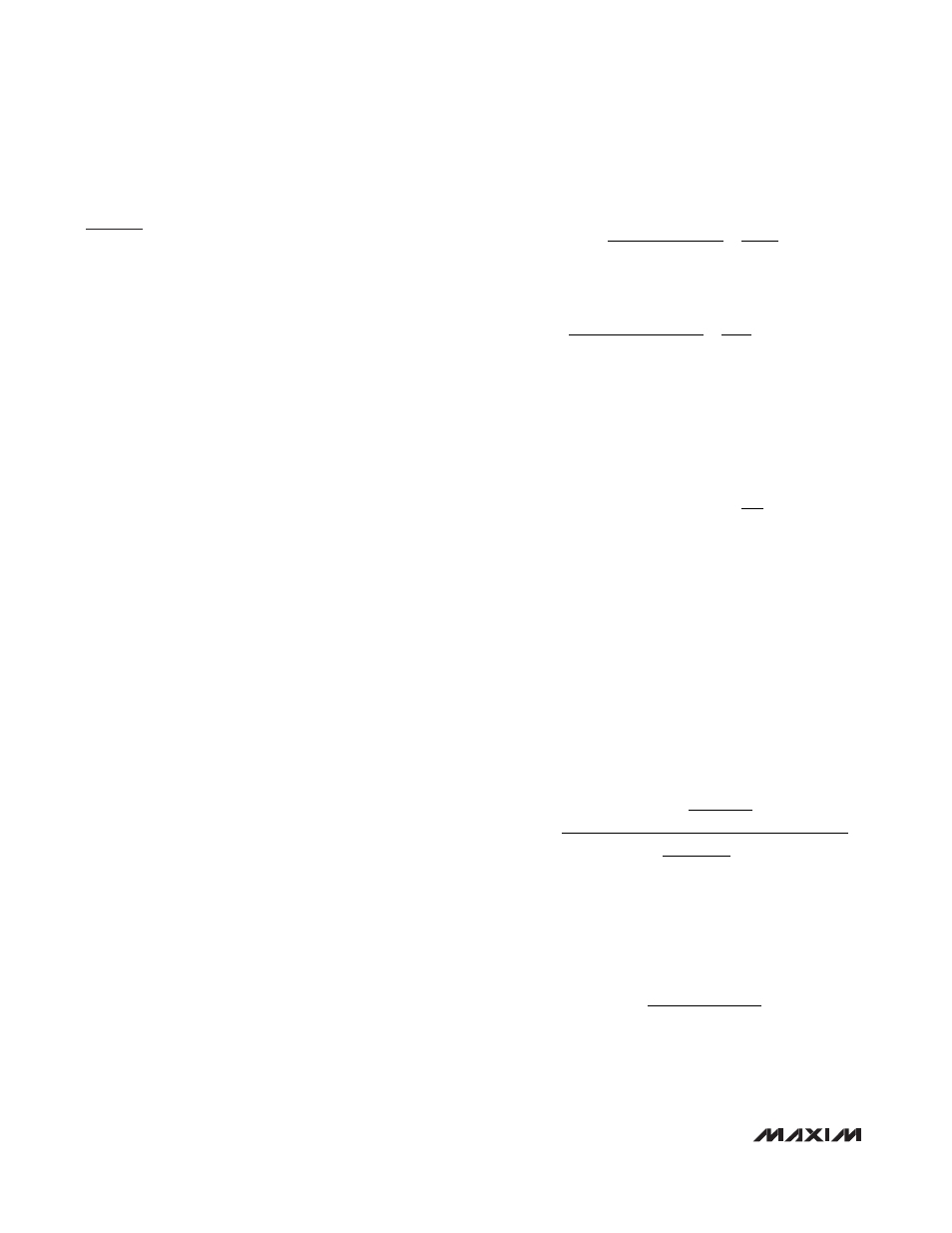
MAX17007A/MAX17008
Quick-PWM Design Procedure
Firmly establish the input voltage range and maximum
load current before choosing a switching frequency
and inductor operating point (ripple-current ratio). The
primary design trade-off lies in choosing a good switch-
ing frequency and inductor operating point, and the fol-
lowing four factors dictate the rest of the design:
•
Input voltage range: The maximum value
(V
IN(MAX)
) must accommodate the worst-case input
supply voltage allowed by the notebook’s AC
adapter voltage. The minimum value (V
IN(MIN)
)
must account for the lowest input voltage after
drops due to connectors, fuses, and battery selec-
tor switches. If there is a choice at all, lower input
voltages result in better efficiency.
•
Maximum load current: There are two values to
consider. The peak load current (I
LOAD(MAX)
) deter-
mines the instantaneous component stresses and fil-
tering requirements, and thus drives output
capacitor selection, inductor saturation rating, and
the design of the current-limit circuit. The continuous
load current (I
LOAD
) determines the thermal stress-
es and thus drives the selection of input capacitors,
MOSFETs, and other critical heat-contributing com-
ponents. Most notebook loads generally exhibit
I
LOAD
= I
LOAD(MAX)
x 80%.
•
Switching frequency: This choice determines the
basic trade-off between size and efficiency. The
optimal frequency is largely a function of maximum
input voltage due to MOSFET switching losses that
are proportional to frequency and V
IN
2
. The opti-
mum frequency is also a moving target due to rapid
improvements in MOSFET technology that are mak-
ing higher frequencies more practical.
•
Inductor operating point: This choice provides
trade-offs between size vs. efficiency and transient
response vs. output noise. Low inductor values pro-
vide better transient response and smaller physical
size, but also result in lower efficiency and higher
output noise due to increased ripple current. The
minimum practical inductor value is one that causes
the circuit to operate at the edge of critical conduc-
tion (where the inductor current just touches zero
with every cycle at maximum load). Inductor values
lower than this grant no further size-reduction benefit.
The optimum operating point is usually found
between 20% and 50% ripple current.
Inductor Selection
The per-phase switching frequency and operating point
(% ripple current or LIR) determine the inductor value
as follows:
For example: I
LOAD(MAX)
= 15A, V
IN
= 12V, V
OUT
=
1.5V, f
SW
= 300kHz, 30% ripple current or LIR = 0.3:
Find a low-loss inductor having the lowest possible DC
resistance that fits in the allotted dimensions. Ferrite
cores are often the best choice, although powdered
iron is inexpensive and can work well at 200kHz. The
core must be large enough not to saturate at the peak
inductor current (I
PEAK
):
In combined mode, I
LOAD(MAX)
is the per-phase maxi-
mum current, which is half the actual maximum load
current for the combined output.
Transient Response
The inductor ripple current impacts transient-response
performance, especially at low V
IN
- V
OUT
differentials.
Low inductor values allow the inductor current to slew
faster, replenishing charge removed from the output fil-
ter capacitors by a sudden load step. The amount of
output sag is also a function of the maximum duty fac-
tor, which can be calculated from the on-time and mini-
mum off-time. The worst-case output sag voltage can
be determined by:
where t
OFF(MIN)
is the minimum off-time (see the
Electrical Characteristics
table).
The amount of overshoot due to stored inductor energy
can be calculated as:
where N
PH
is the number of active phases per output.
N
PH
is 1 for separate mode, and N
PH
is 2 for com-
bined-mode operation.
V
I
L
N
C
V
SOAR
LOAD MAX
PH
OUT OUT
≈
(
)
Δ
(
)
2
2
V
V
T
V
t
SAG
OUT SW
IN
OFF M
=
(
)
⎛
⎝⎜
⎞
⎠⎟
+
L
I
LOAD(MAX)
2
Δ
( IIN
OUT OUT
IN
OUT
IN
SW
O
C
V
V
V
V
T
t
)
⎡
⎣
⎢
⎤
⎦
⎥
⎛
⎝⎜
⎞
⎠⎟
2
-
-
F
FF MIN
(
)
⎡
⎣
⎢
⎤
⎦
⎥
I
I
LIR
PEAK
LOAD MAX
=
+
⎛
⎝
⎜
⎞
⎠
⎟
(
)
1
2
L
V
V
kHz
A
V
V
=
Ч
Ч
⎛
⎝⎜
⎞
⎠⎟
⎛
⎝
12
1 5
300
15
0 3
1 5
12
- .
.
.
⎜⎜
⎞
⎠⎟
= 0 97
.
μH
L
V
V
f
I
LIR
V
V
IN
OUT
SW LOAD MAX
OUT
IN
=
⎛
⎝
⎜
⎞
⎠
⎟
⎛
⎝⎜
⎞
-
(
)
⎠⎠⎟
Dual and Combinable QPWM Graphics
Core Controllers for Notebook Computers
28
______________________________________________________________________________________