Gas supp, Gas supply, Electrical power connections – Raypak MVB 5042004 User Manual
Page 20
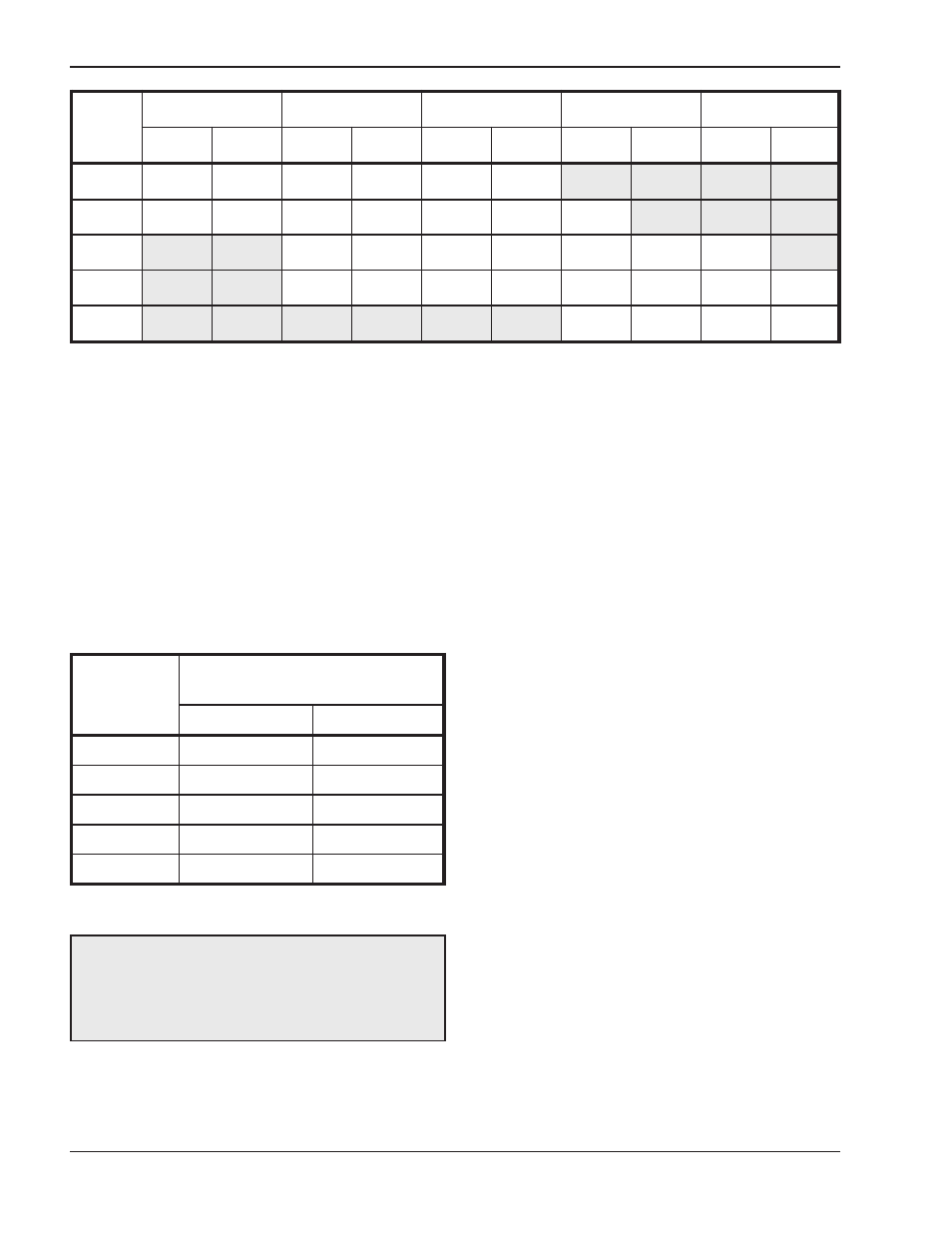
20
•
National Electrical Code and any other national,
state, provincial or local codes or regulations hav-
ing jurisdiction.
•
Safety wiring must be NEC Class 1.
•
Heater must be electrically grounded as required
by the NEC.
•
In Canada, CSA C22. 1 C.E.C. Part 1.
The MVB 504-1504 heaters are wired for 120 VAC, 12
amps while the MVB 2004 heaters are wired for 120
VAC, 18 amps. Consult the wiring diagram shipped
with the heater. Before starting the heater, check to
ensure proper voltage to the heater and pump.
Boiler mounted pumps (up to
3
⁄
4
hp) get their power
supply directly from the boiler power supply (connec-
tions in rear wiring box). Install a circuit breaker sized
sufficiently for both the heater and the pump. Pumps
larger than
3
⁄
4
hp must use a separate power supply
and run the power through the optional pump contac-
tor which is located in the rear wiring box. Use
appropriately-sized wire as defined by NEC, CSA
and/or local codes. All primary wiring should be 125%
of minimum rating.
If any of the original wire as supplied with the heater
must be replaced, it must be replaced with 105°C wire
or its equivalent.
All high voltage wiring connections to the MVB heater
are made inside the rear wiring box as shown in Fig.
18. Pump power should be taken from terminals 2
(Com), 3 (GND) and 6 (Hot) –
3
⁄
4
hp and smaller ONLY.
Power to the MVB heater should be connected to ter-
minals 1, 2, and 3 as noted in Fig. 18. All low voltage
wiring, including sensors, interlocks, enable/disable,
and various options are wired into terminals 1–20 on
the front wiring panel as noted in Fig. 18.
When connecting additional gas utilization equipment
to the gas piping system, the existing piping must be
checked to determine if it has adequate capacity for
the combined load.
The gas valve pressure regulator on the heater is
nominally preset as noted in Table J.
During normal operation, carbon dioxide should be 8.5
to 9.0% at full fire for natural gas and between 9.5 and
10.0% for propane gas. Carbon monoxide should be
‹100ppm.
Electrical Power Connections
Installations must follow these codes:
Natural Gas – 1,000 BTU/ft
3
, 0.60 specific gravity at 0.5 in. WC pressure drop
Propane Gas – 2,500 BTU/ft
3
, 1.53 specific gravity at 0.6 in. WC pressure drop
Table I: Maximum Equivalent Pipe Length
NOTE: Manifold pressures should be ±0.2 in. WC.
Table J: Manifold Gas Pressure Settings
Model
No.
1 in. NPT
1-1/4 in. NPT
1-1/2 in. NPT
2 in. NPT
2-1/2 in. NPT
N
P
N
P
N
P
N
P
N
P
504
15
35
65
150
150
360
754
5
15
35
75
70
175
250
1104
15
35
35
75
100
250
225
1504
10
20
20
45
60
150
150
275
2004
35
85
85
200
Model
No.
Manifold Gas Pressure
(High Fire Values)
Natural Gas
Propane Gas
504
-0.1
-0.1
754
-0.4
-0.1
1104
-1.0
-0.2
1504
-2.4
-0.6
2004
-1.0
-0.5
CAUTION: For proper operation, no more than a
30% drop in gas supply pressure from no-load to full-
load conditions is acceptable. Under no
circumstances should the pressure be outside the
listed operational range.