Tnc model, software and features – HEIDENHAIN TNC 640 (34059x-04) Cycle programming User Manual
Page 7
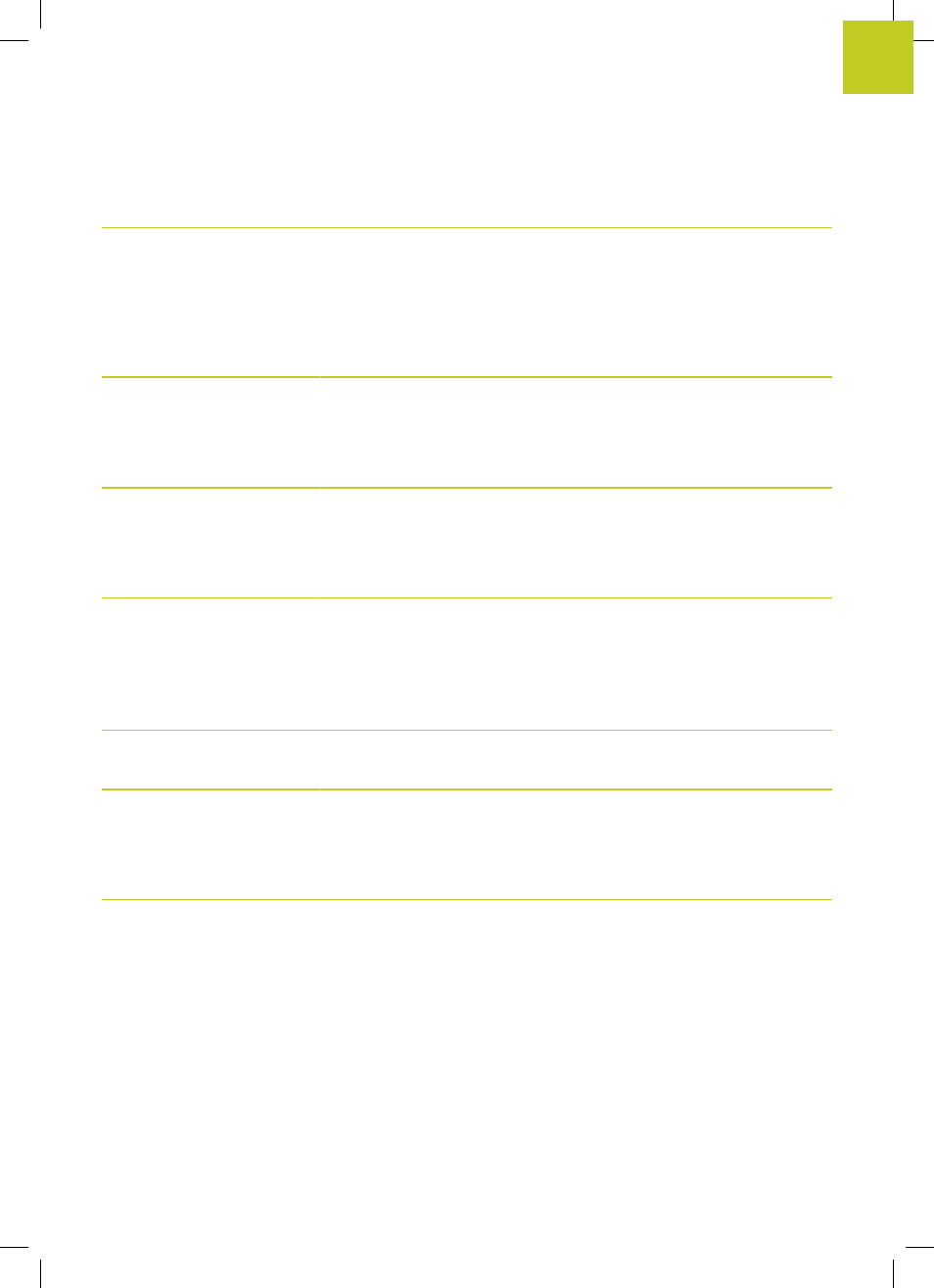
TNC model, software and features
TNC 640 | User's Manual Cycle Programming | 3/2014
7
DXF Converter software option
(option number 42)
■
Supported DXF format: AC1009 (AutoCAD R12)
■
For contours and point patterns
■
Simple and convenient specification of reference points
Extracting contour
programs and machining
positions from DXF data.
Extracting contour sections
from plain-language
programs.
■
Select graphical features of contour sections from conversational
programs
Adaptive Feed Control (AFC) software option
(option number 45)
■
Recording the actual spindle power by means of a teach-in cut
■
Defining the limits of automatic feed rate control
Function for adaptive feed-
rate control for optimizing
the machining conditions
during series production
■
Fully automatic feed control during program run
KinematicsOpt software option
(option number 48)
■
Backup/restore active kinematics
■
Test active kinematics
Touch-probe cycles for
automatic testing and
optimization of the machine
kinematics
■
Optimize active kinematics
Mill-Turning software option
(option number 50)
■
Switching between Milling/Turning mode of operation
■
Constant cutting speed
Functions for milling/turning
mode
■
Tool-tip radius compensation
■
Turning cycles
Extended Tool Managment software option
(option number 93)
■
Extended tool management, python-based
Remote Desktop Manager software option
(option number 133)
■
Windows on a separate computer unit
Remote operation of
external computer units
(e.g. Windows PC) via the
TNC user interface
■
Incorporated in the TNC interface
Synchronizing Functions software option
(option number 135)
Real Time Coupling (RTC)
■
Coupling of axes