Please note while programming – HEIDENHAIN TNC 640 (34059x-04) Cycle programming User Manual
Page 198
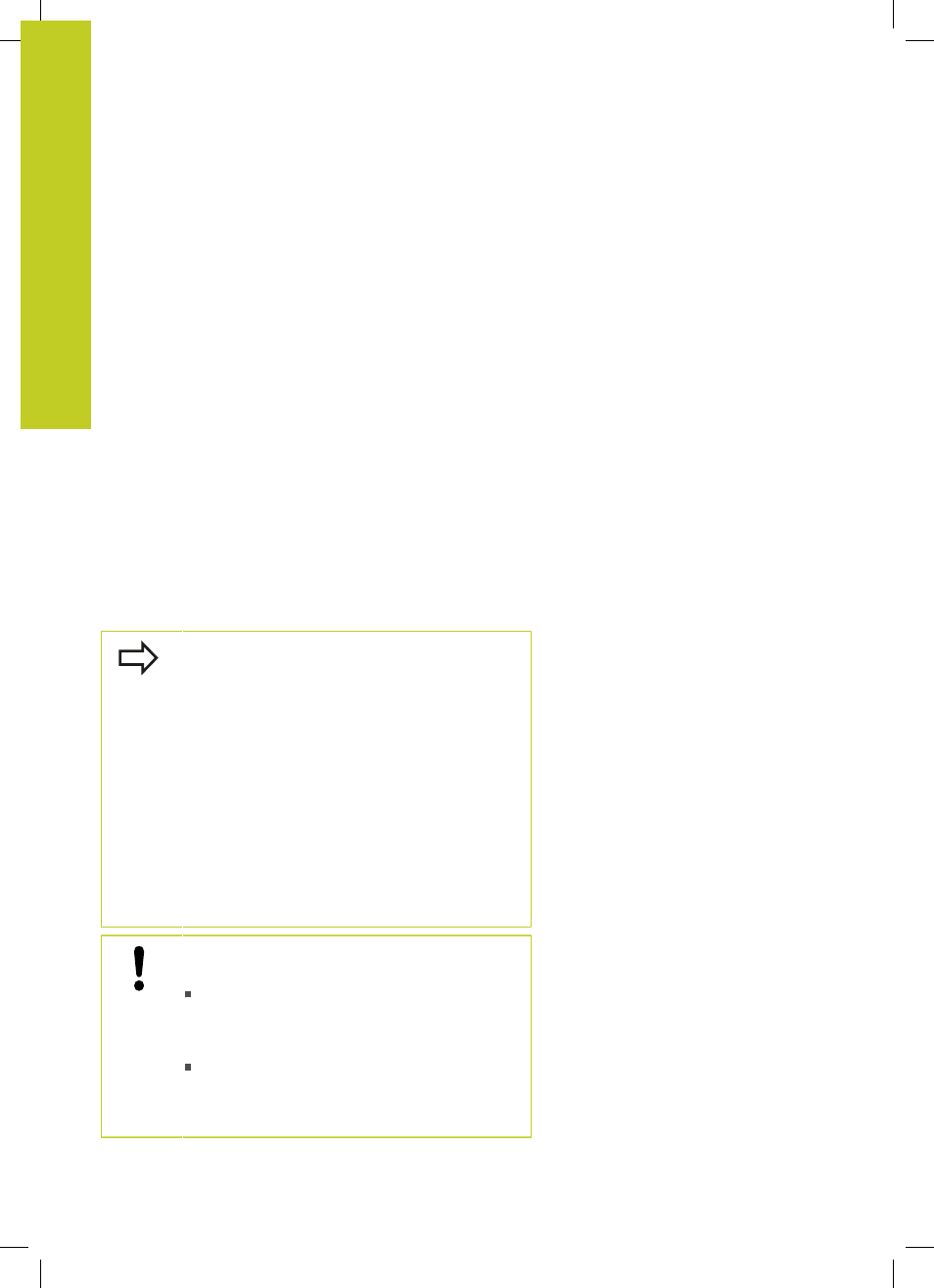
Fixed Cycles: Contour Pocket
7.10 TROCHOIDAL SLOT (Cycle 275, DIN ISO G275)
7
198
TNC 640 | User's Manual Cycle Programming | 3/2014
Roughing with open slots
The contour description of an open slot must always start with an
approach block (
APPR).
1 Following the positioning logic, the tool moves to the starting
point of the machining operation as defined by the parameters
in the
APPR block and positions there perpendicular to the first
plunging depth.
2 The TNC roughs the slot in circular motions to the contour end
point. During the circular motion the TNC moves the tool in
machining direction by an infeed you can define (
Q436). Define
climb or up-cut of the circular motion in parameter
Q351.
3 At the contour end point, the TNC moves the tool to clearance
height and returns to the starting point of the contour description.
4 This process is repeated until the programmed slot depth is
reached.
Finishing with closed slots
5 Inasmuch as a finishing allowance is defined, the TNC finishes
the slot walls, in multiple infeeds if so specified. Starting from the
defined starting point of the
APPR block, the TNC approaches the
slot wall. Climb or up-cut are taken into consideration.
Please note while programming:
The algebraic sign for the cycle parameter DEPTH
determines the working direction. If you program
DEPTH=0, the cycle will not be executed.
When using Cycle 275 TROCHOIDAL SLOT, you
can define only one contour subprogram in Cycle 14
CONTOUR GEOMETRY.
Define the center line of the slot with all available
path functions in the contour subprogram.
The memory capacity for programming an SL cycle
is limited. You can program up to 16384 contour
elements in one SL cycle.
The TNC does not need Cycle 20 CONTOUR DATA in
conjunction with Cycle 275.
The starting point of a closed slot must not be
located in a contour corner.
Danger of collision!
To avoid collisions,
Do not program positions in incremental
dimensions immediately after Cycle 275 since
they are referenced to the position of the tool at
the end of the cycle.
Move the tool to defined (absolute) positions in all
principal axes, since the position of the tool at the
end of the cycle is not identical to the position of
the tool at the start of the cycle.