Choice of number of measuring points – HEIDENHAIN TNC 640 (34059x-04) Cycle programming User Manual
Page 558
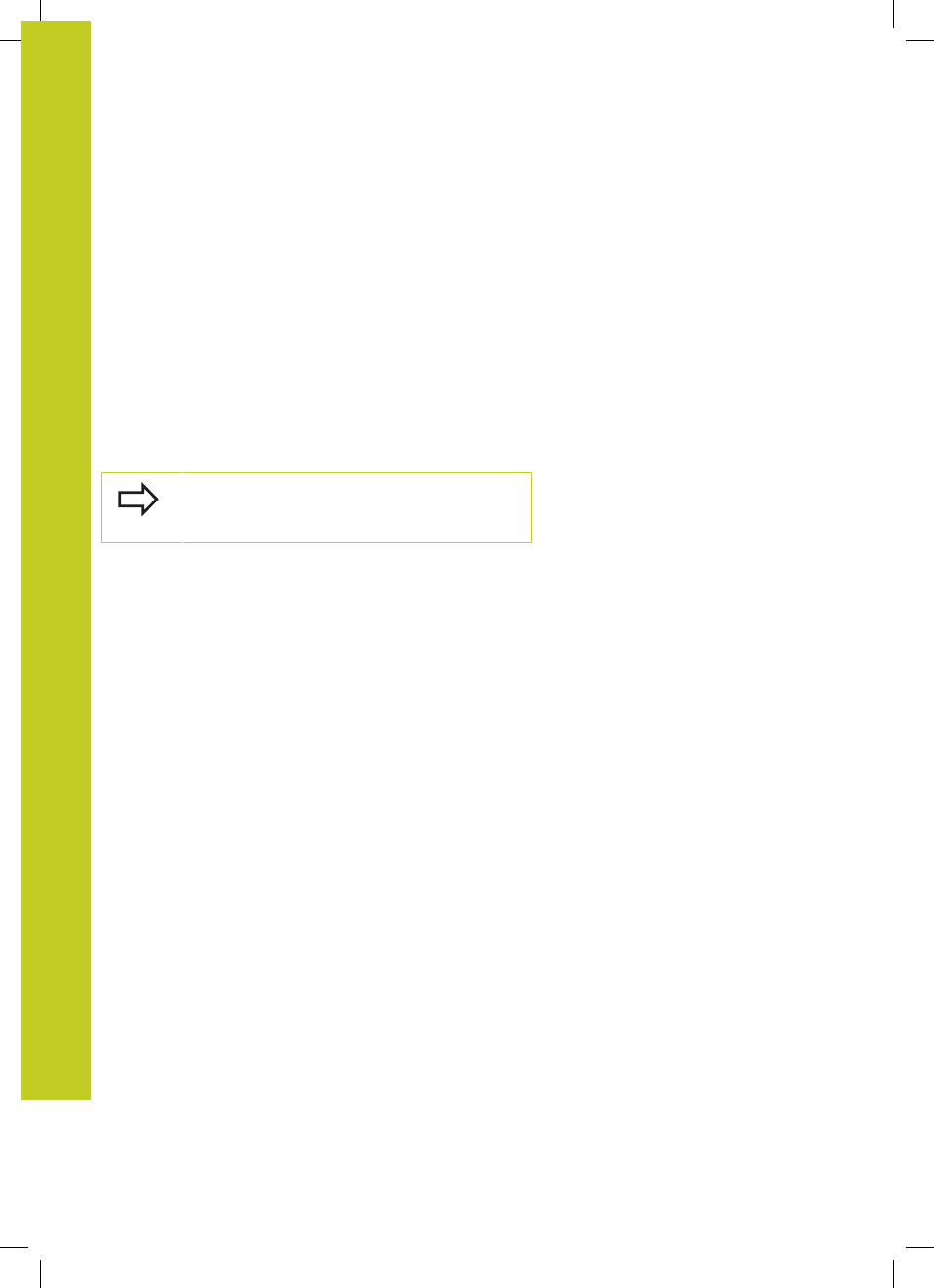
Touch Probe Cycles: Automatic Kinematics Measurement
19.4 MEASURE KINEMATICS (Cycle 451, DIN/ISO: G451, option)
19
558
TNC 640 | User's Manual Cycle Programming | 3/2014
Choice of number of measuring points
To save time you can make a rough optimization with a small
number of measuring points (1 or 2), for example during
commissioning.
You then make a fine optimization with a medium number of
measuring points (recommended value = approx. 4). Higher
numbers of measuring points do not usually improve the results.
Ideally, you should distribute the measuring points evenly over the
tilting range of the axis.
This is why you should measure an axis with a tilting range of 0°
to 360° at three measuring points, namely at 90°, 180° and 270°.
Thus, define a starting angle of 90° and an end angle of 270°.
If you want to check the accuracy accordingly, you can also enter a
higher number of measuring points in the
Check mode.
If a measuring point has been defined at 0°, it will
be ignored because the reference measurement is
always done at 0°.