Advanced programming, Step 9: setting up the hyperdrive, Control loop coefficients – SoundTraxx Tsunami Steam Users Guide User Manual
Page 60
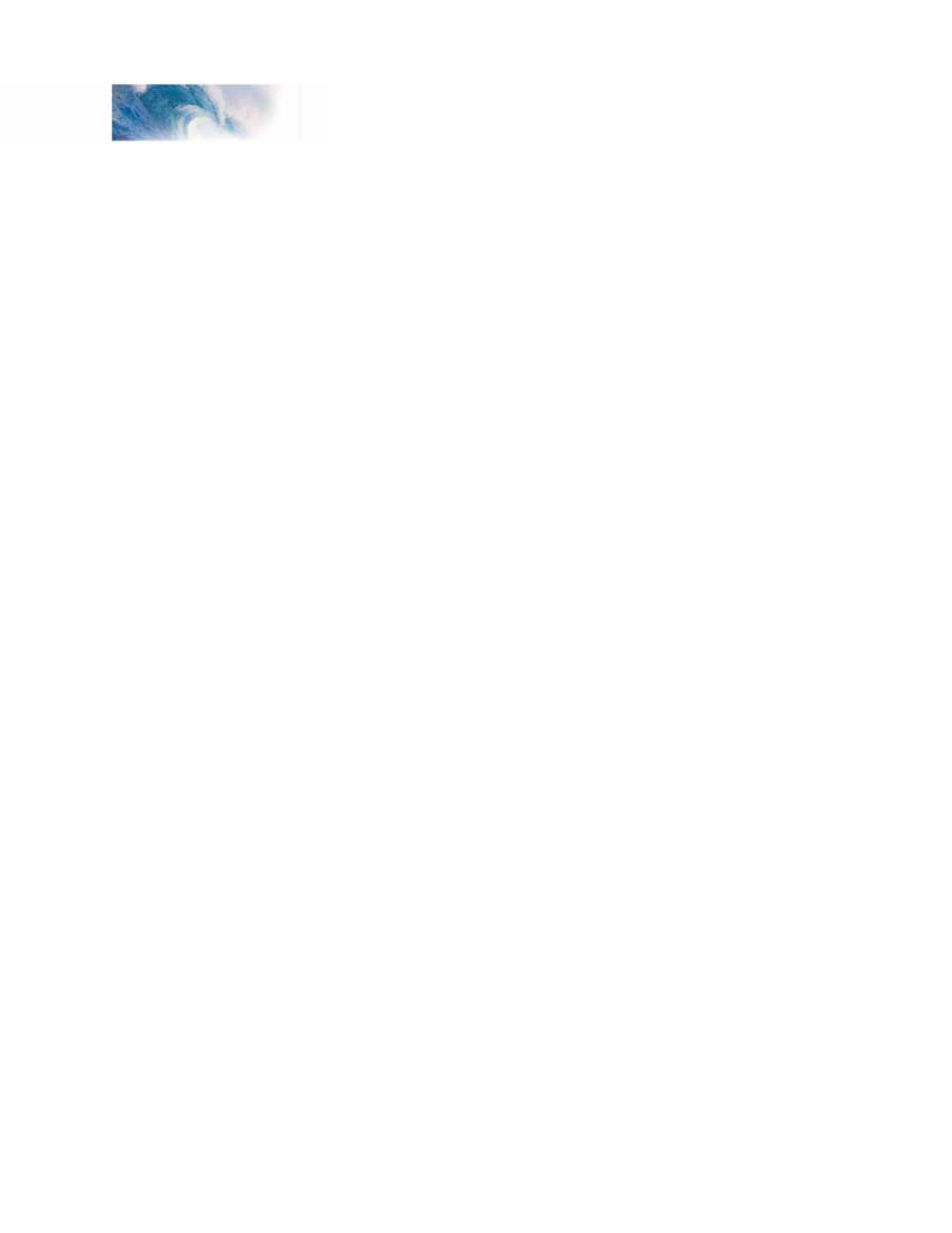
Tsunami Steam Sound User’s Guide
Page 57
Step 9: Setting Up the Hyperdrive
Tsunami’s Hyperdrive system features high-frequency PWM drive for silent
motor control along with load compensation (or back-emf) to improve low
speed operation and maintain constant speed regardless of changes to the
motor load.
The PWM frequency is fixed at 22.000Khz and there are no adjustments.
Tsunami uses back EMF and a PI control loop to sense and control motor
speed. There are four CVs associated with the load compensation feature:
CV 10, Back EMF Cutout
CV 209, Kp Coefficient
CV 210, Ki Coefficient
CV 212, BEMF Feedback Intensity
Control Loop Coefficients
Tsunami compensates for load changes by comparing the locomotive’s
speed, as measured by the motor’s back-emf voltage, with the current throttle
setting. When a difference is detected, the motor voltage is adjusted up
or down so that locomotive speed stays constant. This is done using a P-I
(proportional-integral) control loop that is tuned using two CVs:
CV 209, Kp, controls the Proportional gain of the control loop and
compensates for dynamic changes in the motor load by applying a correction
based on the difference between the throttle setting and the current motor
speed. This CV may be set between 1 and 255. Higher values produce an
increasing level of compensation. However, setting this value too high can
lead to irregular and rough performance.
CV 210, Ki, controls the Integral gain of the control loop and compensates for
static motor load by applying a correction based on the historical (or integral)
difference between the throttle setting and the current motor speed. This
CV may be set between 0 and 255. Higher values produce an increasing
level of compensation and set the ‘snappiness’ of the control loop. However,
setting this CV value too high can lead to oscillations in locomotive speed
and we suggest you use the lowest possible setting that still provides optimal
performance.
Note: Setting both Kp and Ki to zero will cause the motor to stop.
Advanced Programming