Flowserve DMX User Manual
Page 29
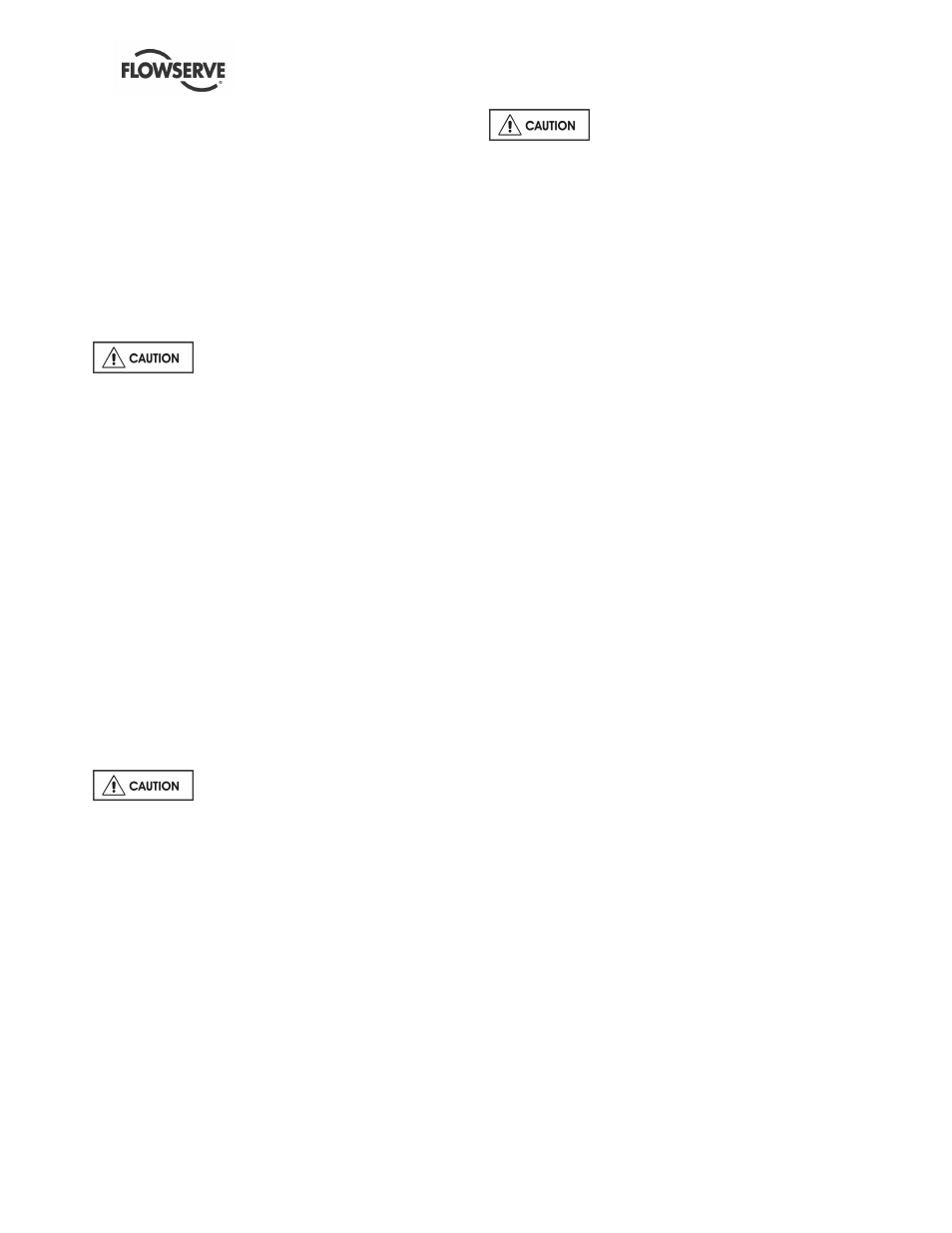
DMX/DMXD/DMXH/DMXDH USER INSTRUCTIONS ENGLISH 85392728 - 10/09
Page 29 of 60
Due to the heavy metal sections, the casing will lag
the liquid temperature during such changes, and
severe temperature stresses and subsequent
misalignment of machined fits may result. Pre-
heating is accomplished by circulating a small
amount of hot fluid through the casing by utilizing
vents, drains or bypass from discharge and suction.
Preheat pump slowly at a rate not to exceed 55.6 °C
(100 °F) per hour.
d) Prime pump and ensure pump suction valve and
bypass isolating valve are open.
Before starting or while operating the
pump, the casing and suction line must be completely
filled with the liquid being pumped. The rotating parts
depend on this liquid for lubrication, and the pump
may seize if operated without liquid.
e) Ensure pump recirculating line (if provided) is
open and free of obstructions.
f) Check that pump is vented by observing leakage
from casing vent and seal piping vent. Close vent
when liquid is emitted.
g) Make sure seal piping is turned on.
h) Prepare the driver for start-up in accordance with
the manufacturer’s instructions.
i)
Check pump rotation by starting unit
momentarily. The direction of rotation is shown
on 10-4, pump data sheet. Note the pump coasts
to a gradual stop.
If pump stops abruptly when driver is
shut down, investigate for pump binding. Take
necessary remedial action before resuming
operation.
j)
Starting the driver (motor driven).
k) Starting the driver (turbine driven).
Start the turbine and bring it up to speed quickly.
l)
As soon as the pump is up to rated speed, open
discharge valve. This will avoid abrupt changes in
velocity and prevent surging in the suction line.
5.2 Pump lubricants
Operation of the unit without
proper lubrication can result in overheating of the
bearings, bearing failures, pump seizures and
actual breakup of the equipment, exposing
operating personnel to injury.
Oil is supplied to the pressure lubrication system by
one of the two oil pumps. The main oil pump is
mounted on a support head which is bolted to the
thrust end bearing body and cap and is driven by the
main pump shaft via a coupling.
An auxiliary oil pump is furnished to supply oil to the
pressure lubrication system to be used as a minimum
for start up, shut down or periods when the main oil
pump can not supply sufficient oil. Whilst the
operational logic of the system is outside the scope of
this section refer to the lube system control panel
manufacturer for actual logic. It is a requirement to
have oil supplied to the bearings prior to running the
machine i.e. start the auxiliary oil pump prior to start
up of the main train, and for shut down of main
machine or indeed at any time the main oil pump fails
to deliver sufficient quantity of oil.
During operation, oil is taken from the oil reservoir by
the pump and is directed through the oil filter and is
then supplied to the pump/drive bearings. A back
pressure relief valve mounted in the lubrication
system maintains the required system oil pressure.
The system is additionally equipped with a low
pressure, pressure switches, which can be used to
control the unit when the oil pressure in the
lubrication system decreases to predetermined
values or prevents the starting of the unit until
adequate oil pressure is established. A gravity
assisted, sloped oil return line conducts the oil from
the pump/driver bearings back to the system
reservoir.
A check valve is mounted in the auxiliary oil pump
discharge line to prevent oil from returning to the oil
reservoir when the main oil pump is running and the
auxiliary oil pump is shut down.
5.2.1
Lubricating oil
Oil requires frequent replenishment at normal
operating temperatures and very frequent
replenishment at elevated operating temperatures.
Oil is always subject to gradual deterioration from use
and contamination from dirt and moisture. This
deterioration and contamination will, in time, be
harmful to the bearing and cause premature wear.
For this reason, oil should be checked for
contamination and deterioration regularly.