Flowserve DMX User Manual
Page 24
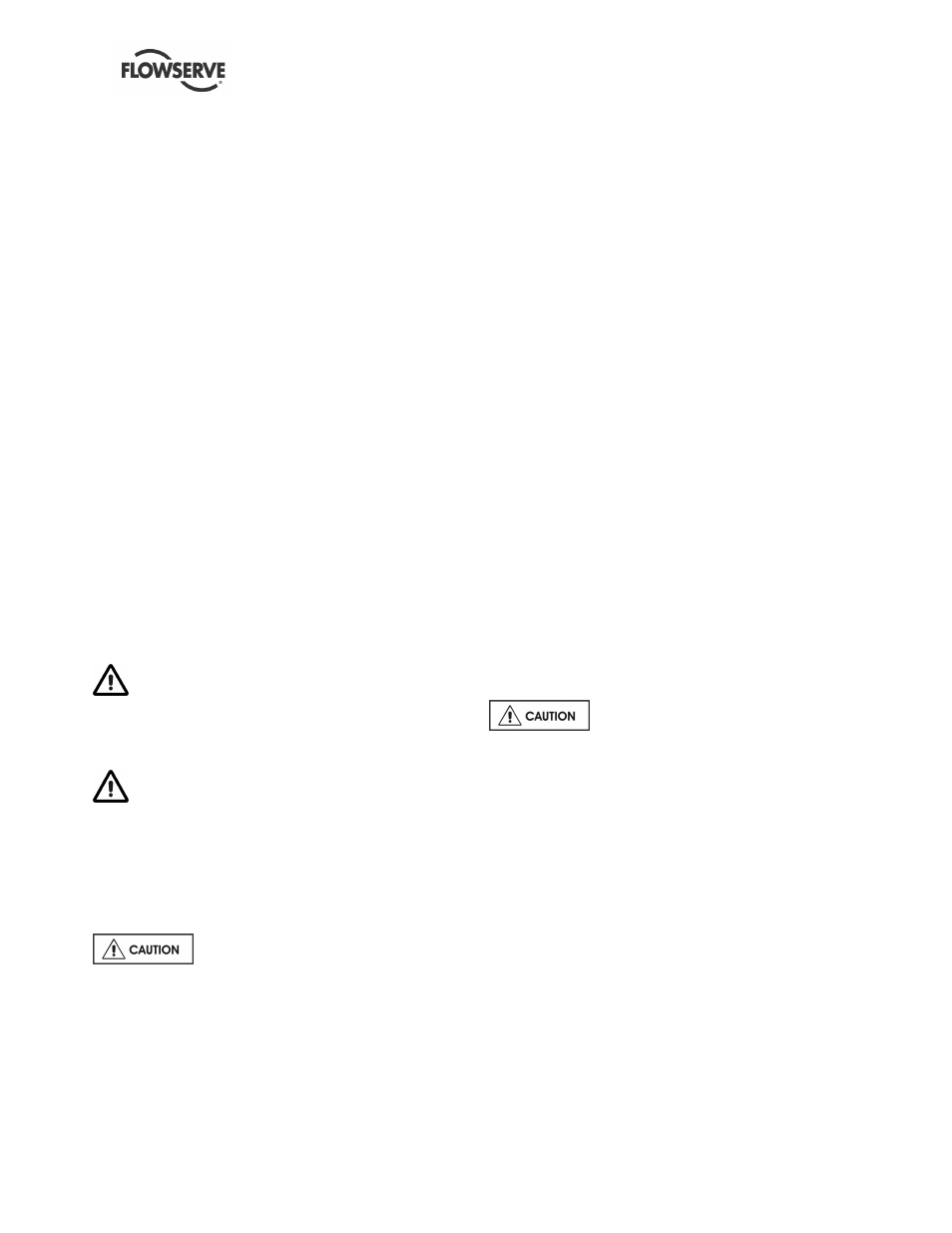
DMX/DMXD/DMXH/DMXDH USER INSTRUCTIONS ENGLISH 85392728 - 10/09
Page 24 of 60
b) Install the dowel pins in the pump drive end foot
by drilling the foot and the baseplate for the
tapered dowel provided.
c) Position the gib blocks to obtain a 0.254 mm
(0.010 in.) clearance between the gib block and
the side of the non-drive end pump foot as noted
on the attached figure. Drill and tap the cap
screw holes for the gib blocks.
d) Tighten the hold-down bolts for the gib blocks.
e) Install the dowel pins in the gib blocks by reaming
the block and baseplate for the tapered dowel
provided.
f) Tighten the hold-down locknuts on the non-drive
end pump feet to establish a 0.051 mm
(0.002 in.) gap between the locknut and the
pump foot.
4.4.8
Hot alignment check
A hot check can only be made after the unit has been
in operation a sufficient length of time to assume its
NORMAL operating temperature and conditions. If
the unit has been correctly cold set, the offset
misalignment will be within 0.076 mm (0.003 in.) TIR
and the angular misalignment will be within
0.0254 mm (0.001 in.) TIR when in operation. If not,
make adjustments.
Do not attempt any maintenance,
inspection, repair or cleaning in the vicinity of
rotating equipment. Such action could result in
injury to operating personnel.
Before attempting any inspection or repair
on the pump the driver controls must be in the
"off" position, locked and tagged to prevent
restarting equipment and injury to personnel
performing service on the pump.
4.5 Piping
The following information regarding
piping is only offered as a general guideline to the
customer. Flowserve requires that all piping and
related systems be designed/installed in accordance
with specifications set forth in Chapter 6, Piping from
API recommended practices 686/PIP REIE 686, First
Edition.
The design of piping, and related systems, is not the
responsibility of Flowserve. It is therefore
recommended that the customer consult a competent
specialist skilled in the field of piping, to insure proper
design/installation of all piping.
4.5.1
Suction and discharge piping
These units are furnished for a particular service
condition. Changes in the hydraulic system may
affect performance adversely. This is especially true
if the changes reduce the pressure at the suction or if
the liquid temperature is increased. In case of any
doubt contact the nearest Flowserve Office.
Suction and discharge piping should be of ample
size, be installed in direct runs, and have a minimum
of bends. Eccentric reducer shall be flat on top
(FOT).
It is desirable to have at least seven (7) diameter of
straight pipe between the first elbow and the pump
suction. Elbow in the piping to the pump’s suction
nozzle should be of the long radius type.
Seven (7) diameters of straight pipe should be used
between two elbows in series and the pump suction.
Elbows in more than one plane should not be used
without splitters.
Splitters are placed in the elbow in the mean radius
line perpendicular to the plane of the elbow.
Provision must be made to support
piping external to the pump to prevent excessive
nozzle loads, maintain pump/driver alignment and
avoid pipe- induced vibrations.
Install a check valve and a gate valve in the
discharge pipe of the pump. When the pump is
stopped, the check valve will protect the pump
against excessive pressure and will prevent the pump
from running backward. The check valve should be
installed between the gate valve and the pump
nozzle in order to permit its inspection. The gate
valve is also useful in priming and starting the pump.
Keep the suction pipe short and direct. Use a suction
pipe equal to or one size larger than the pump
suction nozzle. Keep the suction pipe free of all air
pockets.