Flowserve DMX User Manual
Page 26
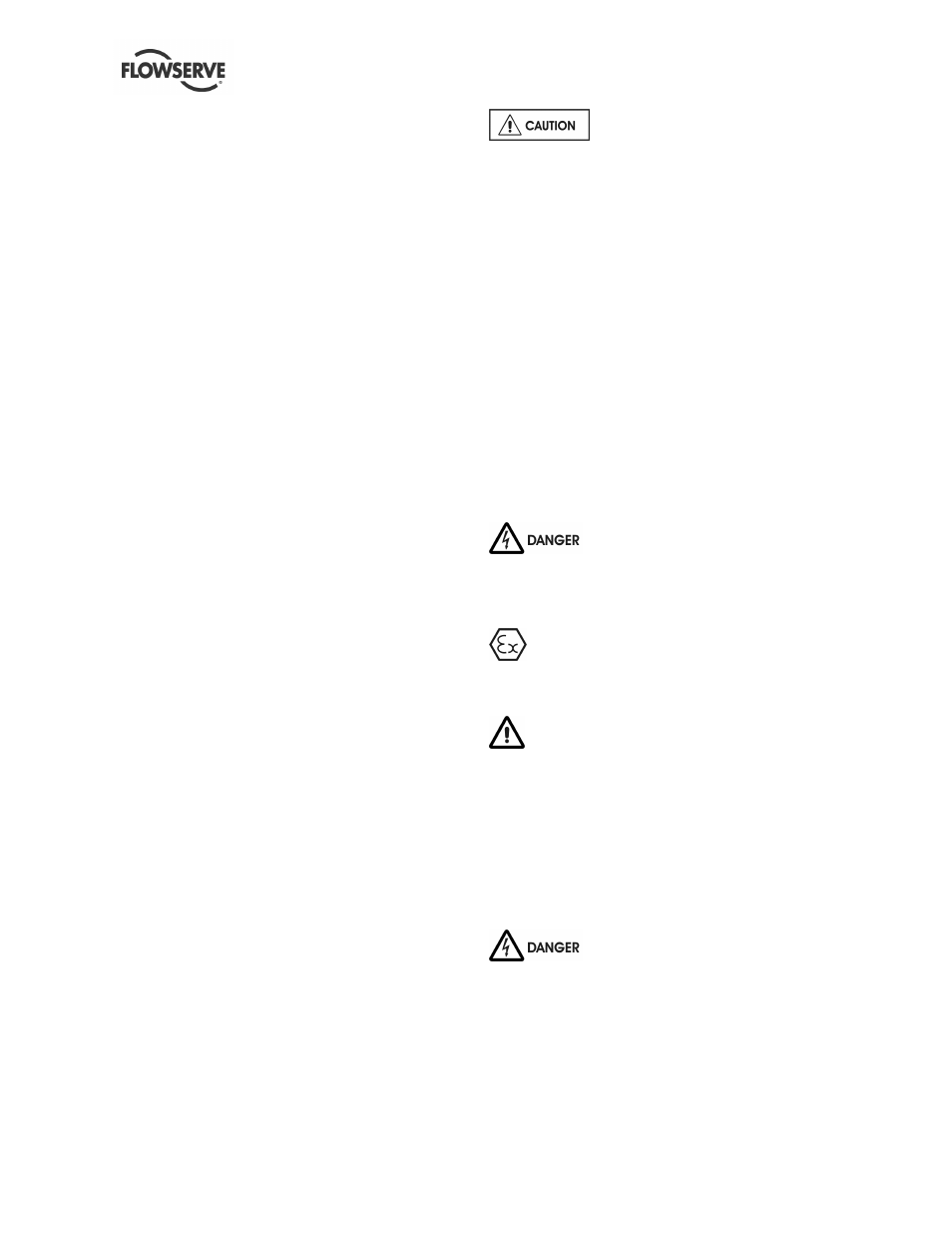
DMX/DMXD/DMXH/DMXDH USER INSTRUCTIONS ENGLISH 85392728 - 10/09
Page 26 of 60
pressure does not fall below that required to prevent
pump cavitation. Pressure (or vacuum) gauges
should be installed on both sides of the strainer so
that the pressure drop across the strainer can be
monitored. During start-up of the system, the gauges
should be monitored continuously. Consult the plant
engineer or system designer for the allowable
pressure differential across the strainer prior to
operating the pump. Pressure differential across the
strainer and/or screen is typically no more than
2 – 3 psig. An increase in the differential pressure
between the two gauges indicates that the strainer or
screen is becoming clogged with dirt and scale.
Before the pressure drop becomes so severe that
cavitation occurs, the pump should be shut down and
the strainer cleaned. Alarm settings to protect the
pump from damaging cavitation and loss of suction
need to be supplied by the plant engineer or system
designer prior to operating the pump. Typical alarm
settings to protect the pump from damaging
cavitation and loss of suction would be 5 psig
differential pressures across the strainer (screen).
The suction piping should be arranged such that the
ultimate strainer configuration (location) allows ready
access for cleaning.
The strainer may be fitted with a finer screen to filter
the inlet flow. When this is done, 40 mesh screens is
typically used for start-up operation, at reduced flow
rates. For final operation in a closed system, the
suction strainers are normally removed after the
system is cleaned. For critical pump applications,
where continuous screening of suction flow is
desirable, and in open systems, 20-mesh screening
is typically used for permanent strainers. At all times,
when using screens and suction strainers, it is
critical that pressure drop across the screen and/or
strainer be constantly monitored to ensure that the
pump suction pressure does not fall below that
required to prevent cavitation.
When dirt and scale have been removed from the
system, as indicated by no further change in pressure
drop across the strainer with time, the start-up
strainer may be removed or the screen may be
replaced with one having larger openings. If a
permanent strainer will be used during normal
operation, the pressure differential needs to be
monitored on a continuous basis.
If a permanent strainer is not used, the start-up
strainer needs to be temporarily reinstalled whenever
the system is opened up for repair or routine
maintenance. As long as a suction strainer or screen
remains in place, the differential pressure should be
monitored on a regular basis.
The pressure drop across the strainer
is a direct reduction in the NPSH available to the
pump. NPSH available must always exceed the
NPSH required by the pump. This requirement may
limit the pump flow rate, particularly during start-up
operation. Alarms or automatic pump shutdown
devices should be installed to minimize the possibility
of pump damage. It is the responsibility of the pump
operator to obtain the allowable pressure drop across
the strainer for safe pump operation from the plant
engineer or system designer prior to operation of the
pump.
4.5.3
Coupling alignment check
Refer to section entitled shaft/coupling alignment and
perform a coupling alignment check as outlined. This
check is recommended to insure the alignment has
not been disturbed during installing suction and
discharge piping.
4.6 Electrical connections
Electrical connections must be
made by a qualified Electrician in accordance
with relevant local national and international
regulations.
It is important to be aware of the EUROPEAN
DIRECTIVE on potentially explosive areas where
compliance with IEC60079-14 is an additional
requirement for making electrical connections.
It is important to be aware of the
EUROPEAN DIRECTIVE on electromagnetic
compatibility when wiring up and installing
equipment on site. Attention must be paid to
ensure that the techniques used during
wiring/installation do not increase
electromagnetic emissions or decrease the
electromagnetic immunity of the equipment,
wiring or any connected devices. If in any doubt
contact Flowserve for advice.
The motor must be wired up in
accordance with the motor manufacturer's
instructions (normally supplied within the
terminal box) including any temperature, earth
leakage, current and other protective devices as
appropriate.
The identification nameplate should be checked
to ensure the power supply is appropriate.