8 electrical installation, 1 important notes, 8electrical installation – BECKHOFF AM3000 User Manual
Page 21: Drive technology
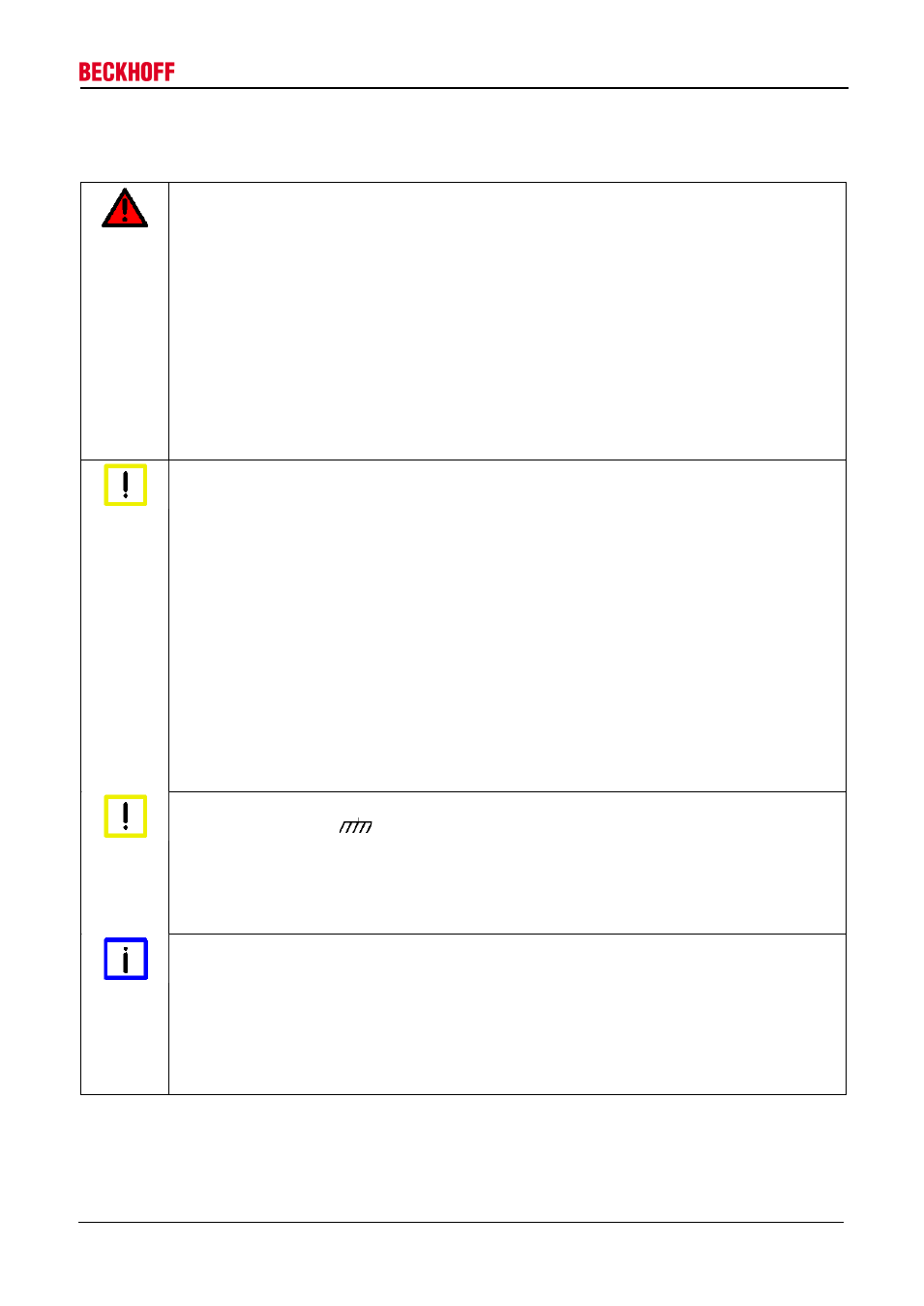
Drive Technology
8 Electrical installation
AM3000 / AM3500
Version: 1.5
21
8
Electrical installation
8.1
Important notes
DANGER
Serious risk of injury through electric shock!
•
Only staff qualified and trained in electrical engineering are allowed to wire up the motor.
•
Check the assignment of the servo drive and the motor. Compare the rated voltage and the
rated current of the devices.
•
Always make sure that the motors are de-energised during assembly and wiring, i.e. no
voltage may be switched on for any piece of equipment which is to be connected. Ensure
that the control cabinet remains turned off (barrier, warning signs etc.). The individual
voltages will only be turned on again during commissioning.
•
Never undo the electrical connections to the motor when it is live. A dangerous voltage,
resulting from residual charge, can be still present on the capacitors up to 5 minutes after
switch-off of the mains supply.
Measure the DC link voltage and wait until it has fallen below 40 V.
Control and power leads may be live, even if the motor is not running.
Attention
Smooth operation
•
Ensure that there the servo drive and the motor are earthed properly. See below for further
information regarding EMC shielding and earthing. Earth the mounting plate and motor
housing. Further details of connection types can be found in Section 8.2
•
Route the power and control cables as separately as possible from one another (separation
> 20 cm). This will improve the immunity of the system to electromagnetic interference. If a
motor power cable is used which includes integral brake control leads, then these brake
control leads must be shielded. The shielding must be connected at both ends (see below).
•
Install all cables carrying a heavy current with an adequate cross-section, as per EN 60204.
The recommended cross-section can be found in the technical data.
•
Wiring:
Connect the resolver or encoder
Connect the motor cables
Connect shields to shield terminals or EMC connectors at both ends
Connect the temperature contact
Connect the motor holding brake
Attention
HF interference
•
The ground symbol , which you will find in the wiring diagrams, indicates that you must
provide an electrical connection, with as large a surface area as possible, between the unit
indicated and the mounting plate in the control cabinet. This connection is to suppress HF
interference and must not be confused with the PE (protective earth) symbol (protective
measure according to EN 60204).
Follow the instructions in the circuit diagrams in Sections 8.3 to 8.6
Note
Long motor cables
•
In case of long motor cables (>25m) a motor choke must be provided between the motor and
the servo drive.
AX2000 / AX2500: Connect up all shielding via a wide surface-area contact (low impedance)
and metallised connector housings or EMC cable glands. Install the motor choke close to the
servo drive.
AX5000: The motor choke is supplied with a connection cable. Do not alter the configuration
(cable length, cross-section etc.).