Palsun® technical guide – Palram PALSU User Manual
Page 33
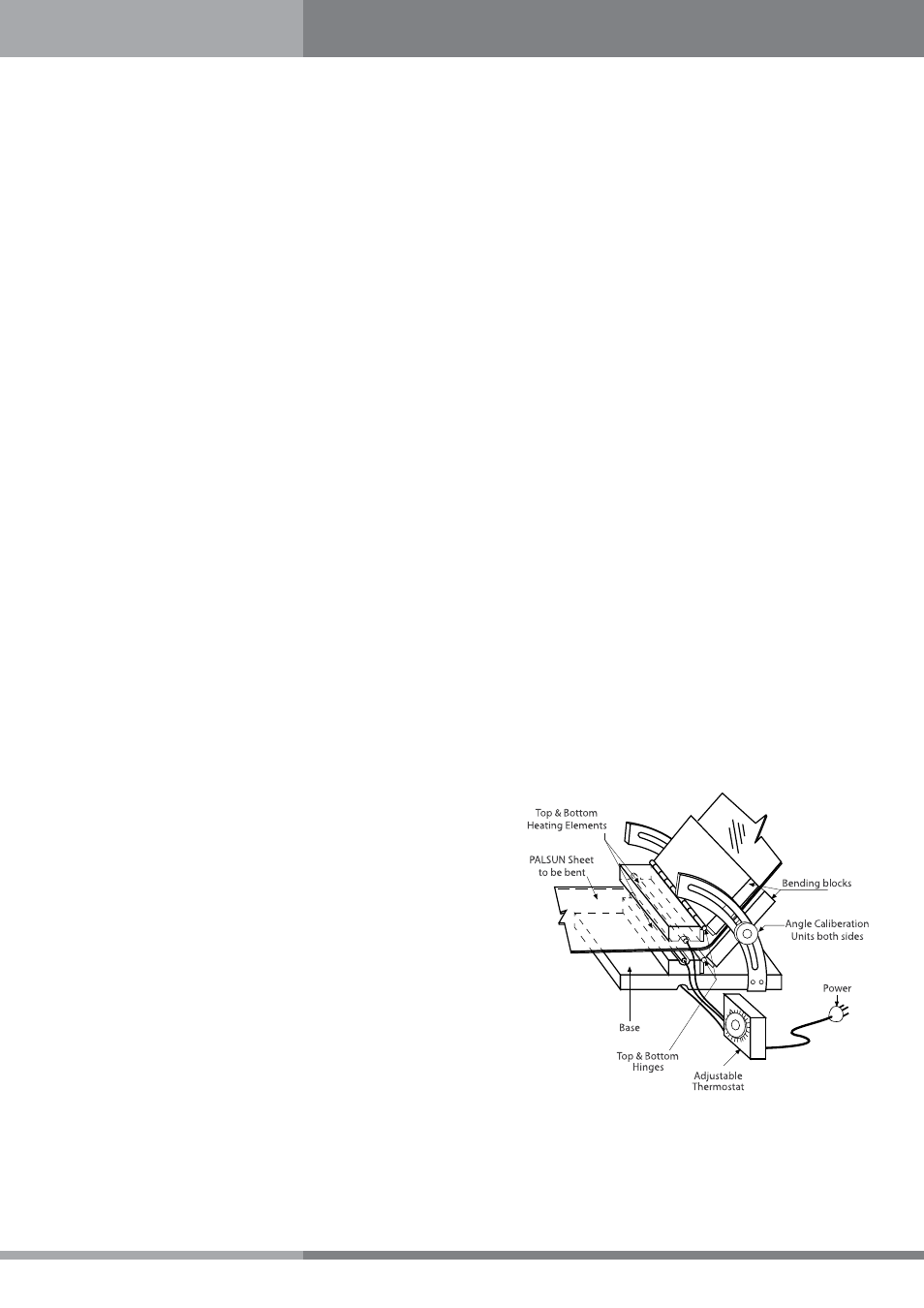
PALSUN® Technical Guide
33
Guidelines to the Heating Process
Good quality thermoformed products can only be achieved through a careful and controlled heating process. All parts of the
treated sheet should reach even, uniform temperature, achieved by a slow, controlled heating rate, avoiding sudden changes in air
circulation and temperature. Such events may result in hot spots and possible distortions. Sheet edges must maintain the same
forming temperature as the whole sheet.
Pre-heating of the clamping frame from 120°C to 130°C is recommended.
Temperature Regulation: Continuous regulation of the sheet’s temperature must be maintained inside the thermoforming device itself.
PALSUN sheet (of any type) tends to cool quite quickly, and may need a regulating system for adding or dispersing of excess heat on the spot.
The sheet’s temperature at the thermoforming zone (or the whole sheet) should be kept between 180°C and 210°C during the forming process.
Forcing the sheet to form at a lower temperature may induce detrimental internal stresses, reducing the sheet’s impact
resistance and increasing its chemical sensitivity. Internal stresses are invisible and can be detected only by polarized light.
Annealing may reduce the stresses, although it is a complicated process and could be inefficient or impossible to perform in most cases.
Protective Polyethylene (PE) masking in Thermoforming: Special masking is available for sheets intended for thermoforming and
should be specified in these cases. This type of masking may be kept on the sheet when practicing most thermoforming methods
and peeled off right before performing the procedure. When using sheets with standard masking, it should be removed prior to the
thermal treatment, otherwise it is likely to fuse into the sheet’s face.
Hot-Line Bending
General Guidelines
1. Description: A simple bending technique, used for forming local, straight line, one axis bent parts (such as corners, boxes, and
machine guards). This type of bending is usually preferable (if possible) to cold line-bending.
2. The process: A bending device with localized heaters on one or two sides of the sheet to be bent is used. The “sandwiched“ two-
sided heating method is preferable, since it retains the same temperature on both sides at the time. a one-side heater method
requires turning the sheet over a few times during the heating period, in order to maintain optimal temperature on both sides.
Steps & Indications
One-sided heating method may suffice for sheets up to 3 mm (0.12 in.). Thicker sheets or more demanding cases require using two-
sided heating. Keeping control of the sheet’s temperature limits of 155-167°C (31-332°F) is of the utmost importance.
Forcing the bend at lower temperatures will render the sheet fragile at the bend. This simple bending process enables working with
regular sheets, without pre-drying. Experimenting with small samples before final execution is highly recommended.
Figure 15: Heat bending device