Finishing, Palsun® technical guide – Palram PALSU User Manual
Page 29
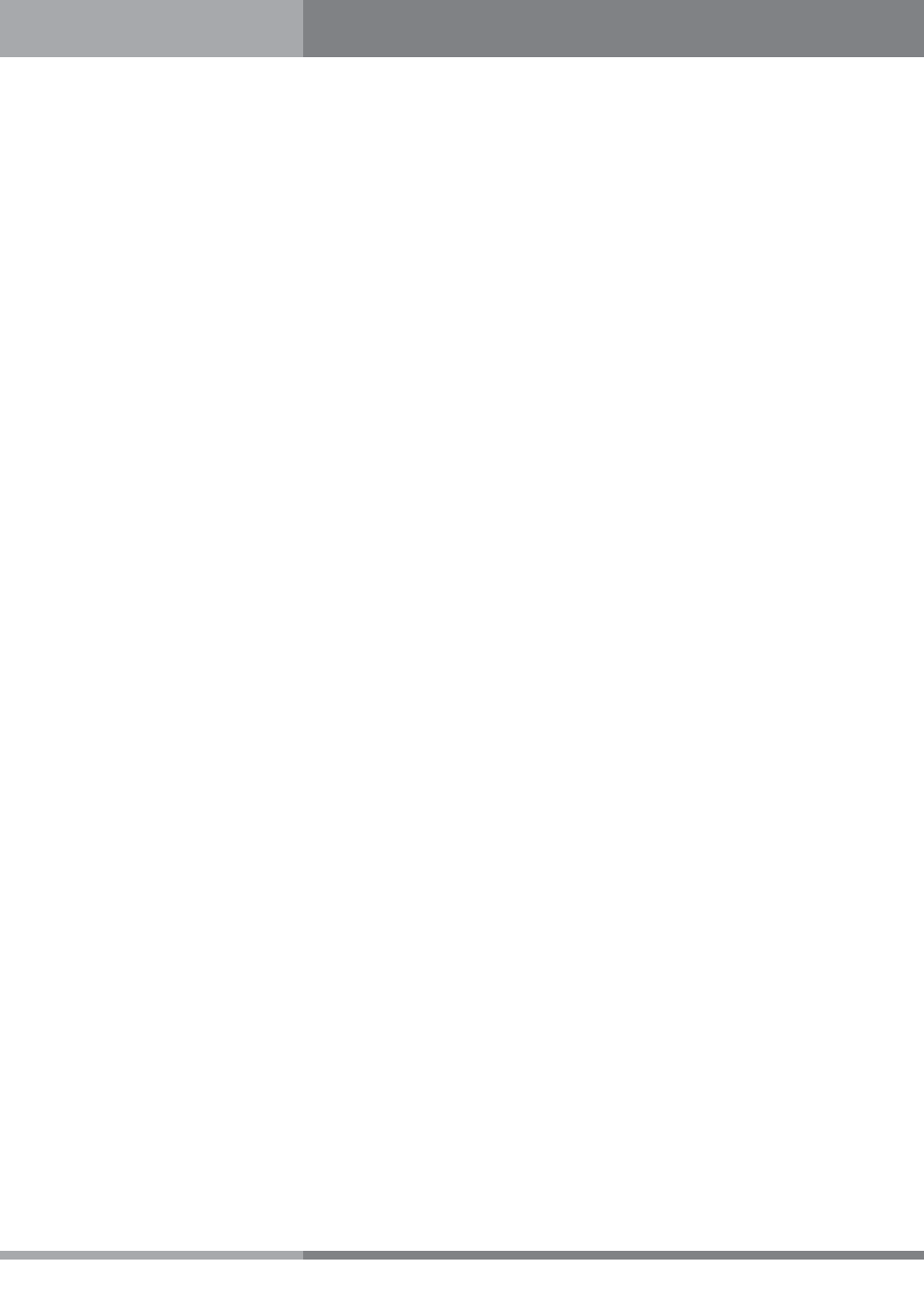
PALSUN® Technical Guide
29
Drilling tips and recommendations
Location: Locate holes no closer to the edges than 2 – 2.5 times the diameter of the pertinent hole, with a 10mm (0.4 inch)
minimum.
Precision: It is imperative to keep the sheet (or stack of sheets) firmly clamped to a stable workbench (or a similar base) to avoid
fluttering during drilling.
Cooling: Usually cooling is not required with regular drills.
However, in cases of deep drilling, like putting perpendicular holes through the sheet’s edge, or when drilling through a stack of
sheets, cooling both the drill bit and the vicinity of the hole with a jet of compressed air is a good practice.
It is also recommended, when drilling deep holes, to stop frequently, pull the drill out and clear the hole from swarf and debris
with compressed air.
Preventing internal stresses: Producing a clean, smooth bore, keeping heat buildup to the minimum, by the procedure
described above, prevents excessive heat buildup, meltdown and gumming of the drilling dust and debris, and possible seizure
of the bit. It also prevents undue internal stresses at the vicinity of the hole.
Honing and polishing the edge of the hole by mechanical or chemical means contributes to keeping the sheet stress-free,
preventing cracking.
Maintaining the edge: Carbide tipped twist drill bits are preferable for long or continuous production runs. They are more
durable and improve the edge quality.
Finishing
General Comments
Reasons, Means and Targets
The final step in fabrication, finishing improves both the practical and aesthetic properties of PALSUN sheet prior to assembly.
Grinding & Polishing
This is mostly done as a part of edge preparation.
Practical objective: Rough, uneven, untended edges may be starting points for crazing and cracks after the PALSUN sheet is
installed and subjected to day by day exposure to wind loads, UV radiation and thermal expansion & contraction, not to mention
man-made impacts.
Aesthetic objective: Nicely finished, smooth edges are a must for a quality appearance of the finished product, often installed
with exposed edges.
Decorating: A type of finishing intended mostly for aesthetic appearance or for display purposes. Executed by painting, printing,
films or hot stamping.
Grinding / Sanding
General
A primary stage in edge finishing, rough or jagged edges and cutting tool marks created by a saw, shearing machine or a router,
can be removed by grinding.
Grinding / Sanding Recommendations
A belt sander, equipped with a 400-500 grit belt, running at 20 - 30 m/sec (65 - 100 ft./sec), is the preferred option, applying low
contact pressure during operation. Wet sanding and waterproof belts are preferable, as they prevents heat buildup, sanding
dust accumulation, and prolong sanding belt life.
A reciprocating or orbital sander can also be used, but it can be applied only by the dry sanding method.
Manual Sanding can also be used, wet or dry, working with successive grit size abrasive paper (Starting with 100, then 280-grit
silicon-carbide, and finally 400-600 grit sandpaper).