Cold forming – Palram PALSU User Manual
Page 31
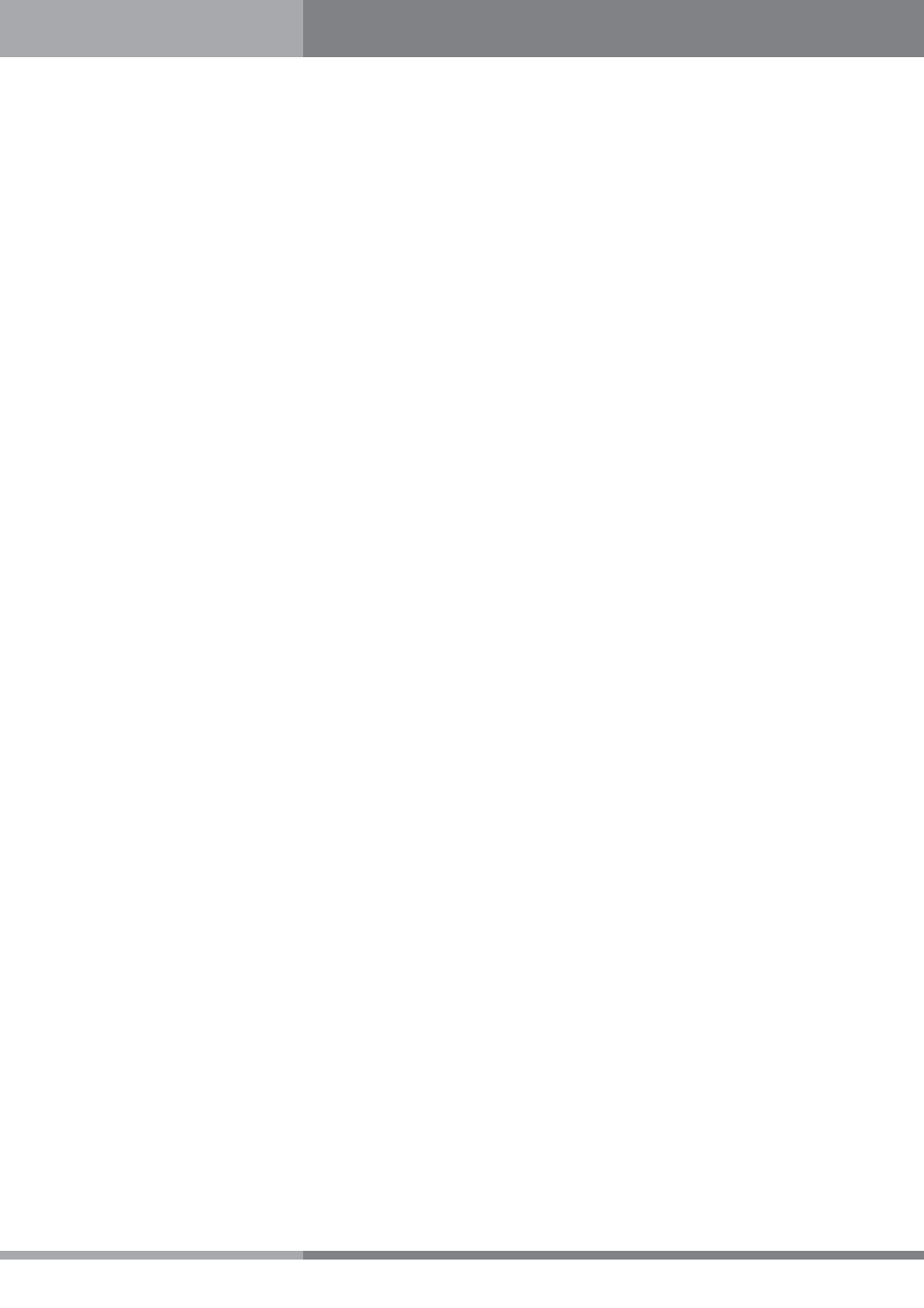
PALSUN® Technical Guide
31
Cold Forming
Cold Curving
1. PALSUN sheets can be cold bent or curved, within their minimal permitted bending radius, without damaging their mechanical
performance. The minimal permitted bending radius for a PALSUN sheet is a factor of their thickness and should be calculated in the
following manner: 200 x sheet thickness (e.g. for a 5mm PALSUN sheet, 5 x 200 = 1000mm minimum cold bending radius). Moreover,
based on our experience and observations, the internal stresses induced by curving give them extra strength and rigidity in both
directions, as in pre-stressed concrete elements.
2. Rigidity and support spans increase progressively as the curve radius is reduced (down to the minimal permitted radius). A shallow
curve should be considered virtually the same as a flat panel, while a deep curve may add significantly to the bridging ability.
Brake Forming
General Notes
1. PALSUN sheets can be cold-bent in a straight line (line bending). Standard metalworking tools, like a brake press, may be used for
bending. The bending process results in permanent plastic deformation. The degree and quality of this change depend on the
thickness of the PALSUN sheet, the final bending angle required, and the actual tools used.
2. When brake forming of PALSUN is conducted, the internal elastic stresses induced along the bent line reduce the mechanical
properties, UV resistance, and chemical resistance of the sheet along the bending line. Palram recommends using this process for less
demanding applications, and protecting the cold bent areas of the sheet from contact with aggressive chemicals or excessive forces.
3. Annealing can reduce the residual stress level induced by the cold bending process, improving the sheet’s mechanical properties.
4. The maximum angles that can be obtained using this process depend on the PALSUN sheet thickness, and the extent of the internal
elastic strain. Palram recommends a 24-48 hour delay for sheet to relax after bending. In order to achieve the desired angle, the
sheet has to be bent 20-40 degrees in excess of that angle, depending on the angle and sheet thickness. During the stress relaxation
period immediately after bending, the bent sheet will expand and regain the required shape.
5. Certain types of sheets are not suitable for either cold or thermal forming, such as PALGARD abrasion resistant sheet. This type is
supplied with a tough, scratch-proof finish, which can not be bent and must be installed “as is”.
Practical Recommendations & Work Instructions
1. Preparations of the PALSUN Sheets and Tooling for Bending:
a. Cut the sheet to its required pre-bending size. Palram recommends leaving the protective film on both sides during the cutting,
edge preparation and cold bending operations.
b. Sand and polish the sheet’s edges to a very smooth finish. Rough edges or the tiniest fissure may initiate cracks and fractures at the
vicinity of the bending lines, due to internal stresses induced by the bending process.
c. Palram recommends conducting preliminary bending tests on small samples of the same (or varied) thickness of the intended sheet,
and try a few different values of excess bending. After arriving at a satisfactory result you can start production.
d. It is advised to use special tooling, like blades and anvils, designed for plastic sheet bending. Standard metalworking blades and anvils are not
necessarily suitable for bending plastic sheets. For plastics, we recommend using a special bending blade with a straight, rounded business
edge. The edge radius should be about 4-6 mm (0.16 to 0.24 in.). The thicker the sheet, the larger edge radius required. The anvil channel outer
“banks” (corners) should be rounded. Both blade and anvil are to be smooth and polished, with no projections, irregularities or rough edges.
Please note that an anvil channel for plastics bending is different than the one suitable for metalworking. It has a wider, flat bottom
and much steeper “banks”.
2. Cold Bending Fabrication:
a. Bending a sheet with an UV protected side (the printed protective film side) on the exterior of the bend gets best results. Therefore,
unless otherwise requested, lay the sheet to be bent with the printed side face down.
b. For optimal results, perform the brake forming quickly, with an additional 20-40 degrees as explained above, then leave the sheet
to relax for 24-48 days.