Omnilink 5000 feed manual – LINK Systems OmniLink - Feed Interface User Manual
Page 26
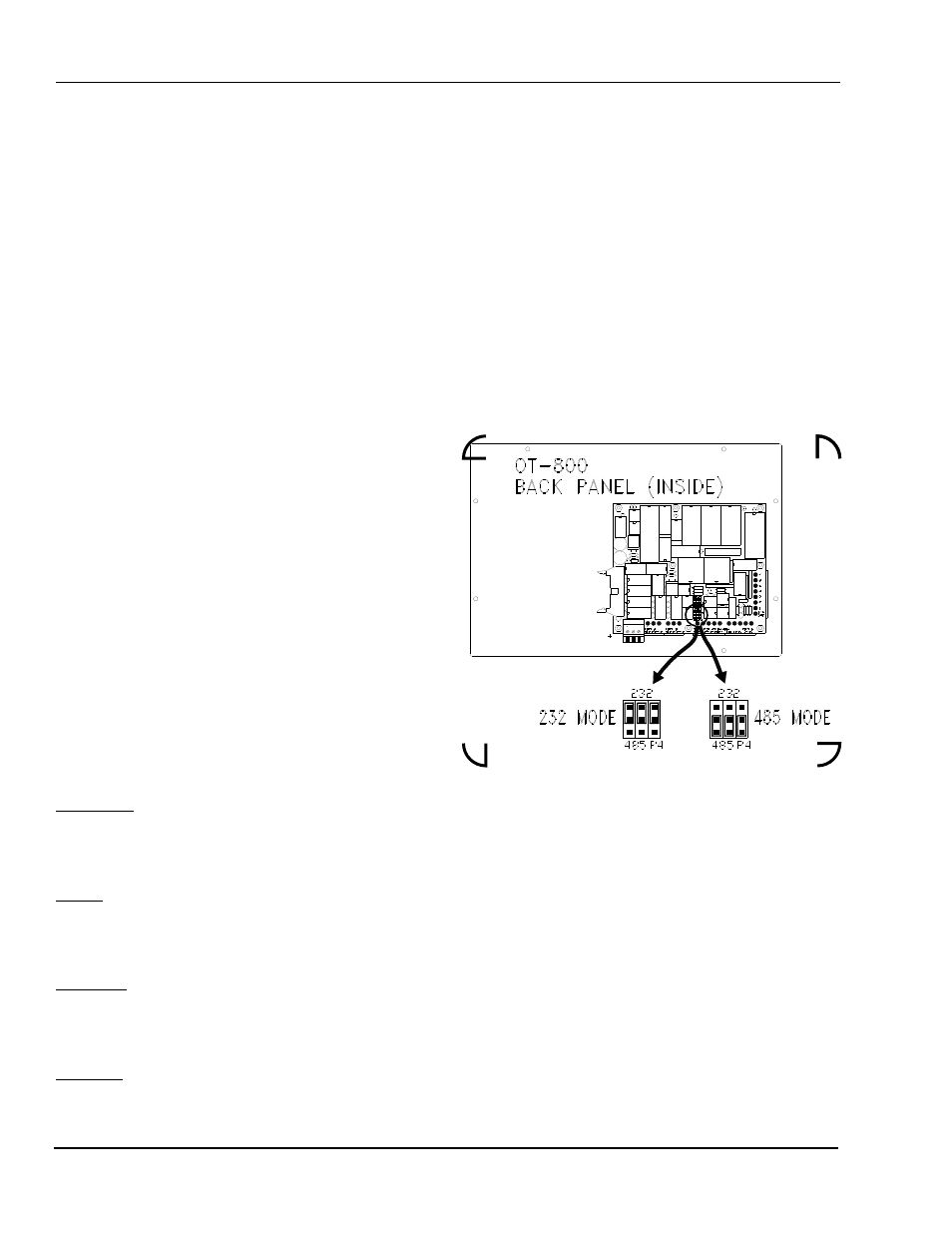
OmniLink 5000 Feed Manual
December 13, 1999
3.4
Manual Rev 2.3
the feed. Note that the units displayed to the right
of the value should be set as well. To change the
max acceleration, use the arrow keys to move the
highlight cursor to the numeric “Max Accel” field.
Enter the desired max acceleration using the
numeric keypad and hit the “ENTER” key. To
change the max acceleration units, use the arrow
keys to move the highlight cursor the “Max Accel”
units field (to the right of the number). Hit the
“CHANGE SETTING” softkey until the desired
units appear (choices are in/sec
2
and mm/sec
2
).
These values are used in three ways.
First, they will not allow a feed acceleration
setting greater than this number to be entered.
Second, feeds that support only a “percent of
full scale” acceleration value can be made to accept
acceleration in whatever unit is entered for the
“Accel Units” setting. For instance, if 1000 in/sec
2
has been entered as the max acceleration of a feed
that requires acceleration in percentage of full scale,
then an entry of 500 in/sec
2
for the feed acceleration
will cause “50%” to be sent to the feed.
Third, feeds that do not accept percent of full
scale acceleration entry can be made to if “% Full
Scale” is selected in the “Accel Units” setting. For
example, if 1000 in/sec
2
has been entered for the
max acceleration of a feed that requires acceleration
in in/sec
2
, then an entry of 50% will cause 500
in/sec
2
to be sent to the feed.
Baud Rate -
The baud rate used to “talk” to the
feed. This should match the baud rate setting on the
feed (typically 9600).
Parity -
The parity setting used to “talk” to the
feed. This should match the parity setting on the
feed (typically None).
Data Bits -
The number of data bits used to
“talk” to the feed. This should match the data bits
setting on the feed (typically 8).
Stop Bits -
The number of stop bits used to
“talk” to the feed. This should match the stop bits
setting on the feed (typically 1).
3.3
Setting the New Communication Board
Feed Port for RS-232 or RS-485
Operation.
Occasionally a feed will have to be interfaced
via RS-485 instead of the more common RS-232.
With the old communication board, an external RS-
232 to RS-485 converter was necessary. The new
communication board has a set of three jumpers (see
figure 3.4) that allow serial port 4 to be configured
for either mode.
Figure 3.4:
Jumper Settings for Port 4 of New
Communication Board
Using figure 3.4 as guide, set the jumpers for
RS-232 or RS-485 as appropriate. The installation
section for each feed will indicate if this is
necessary. If the installation section for a feed does
not explicitly state that RS-485 operation is
required, then this should be left as RS-232, which
is how the card ships.