Mechanical footprint – Echelon LonWorks Twisted Pair Control Module User Manual
Page 17
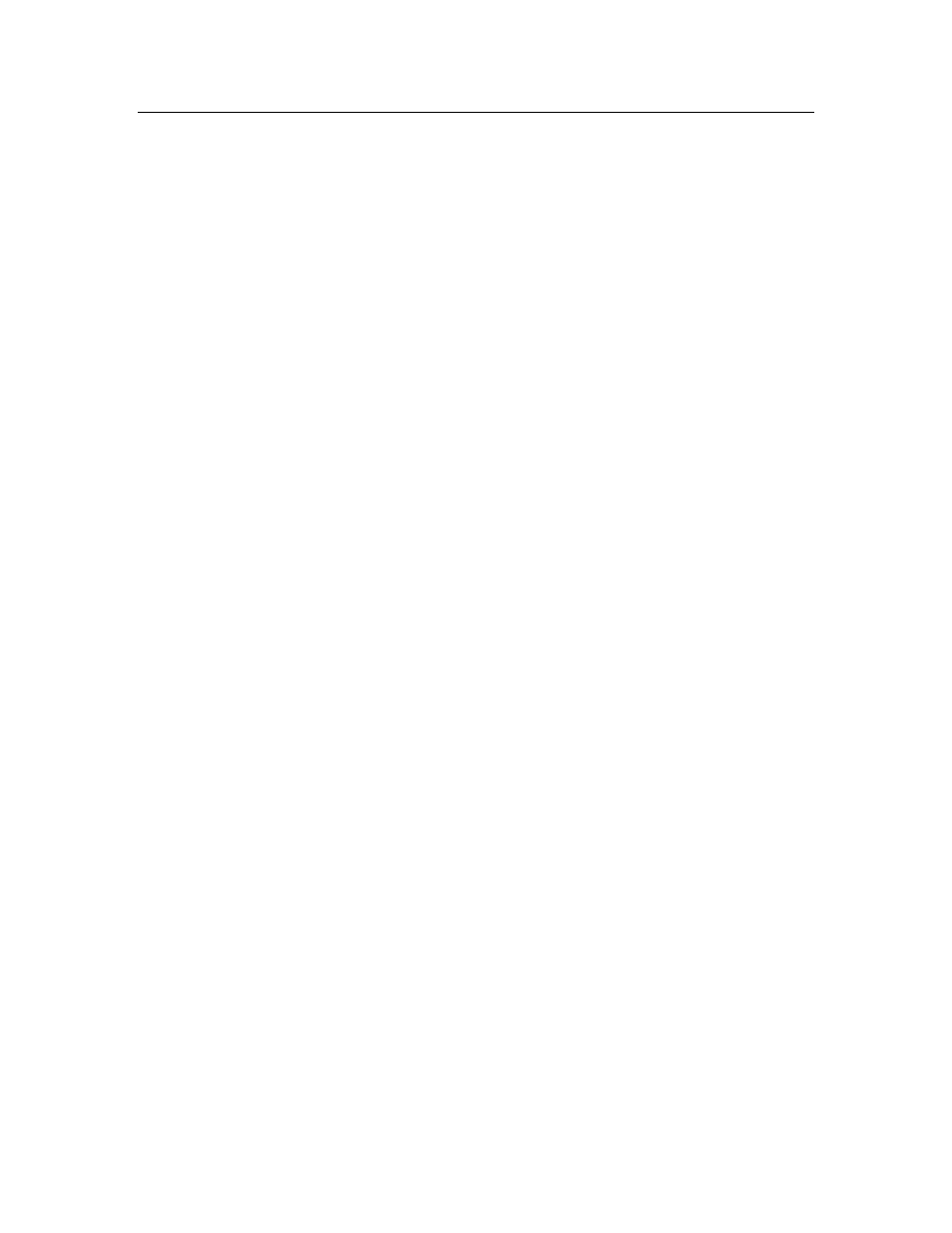
LonWorks Twisted Pair Control Module User's Guide
9
Mechanical Footprint
The Neuron 3150 Twisted Pair Control Modules share a common footprint and
connectors as shown in Figure 5 on page 10. The most common control module
mounting scenario uses socket strips on the application electronics board which
connect with P1 and P2 as shown in Figure 6 and Figure 7 on page 11.
Example vendor information for socket strips that mate with the 0.025 inch (0.64
mm) square header posts of P1 and P2 are listed in Table 6 on page 11.
If necessary, taller socket strips can be used to gain more clearance between the
control module and the application board. Decisions about component placement
on the application electronics board must also consider the electromagnetic
interference (EMI) and electrostatic discharge (ESD) issues discussed in Chapter
5, Design Issues, on page 27.
Figure 6 and Figure 7 show the maximum height of parts on both sides of the
control modules. Application designs using the transformer-isolated twisted pair
transceivers should maintain a minimum of 0.15 inch (3.81 mm) clearance from
P2 pins and traces on the network side of the transformer to achieve the
minimum isolation specified for these modules. Refer to EMI Design Issues on
page 28 and Neuron 3150 Control Module Keepout Areas on page 31 for isolation
requirements.
Three plated mounting holes that accept No. 6 (3.5 mm) mounting screws are
electrically connected to the control module ground plane. When the 0.025 inch
(0.64 mm) square posts of P1 and P2 are inserted into the sockets they provide
enough holding strength (3 oz (85 g)/pin) to secure the control module against
shock and vibration to the operating limits of the components on the control
module. However, at least one metal standoff and fastening screw located at the
mounting hole near the P2 connector is recommended to meet EMI limits and for
ESD protection (see Chapter 5).
For the TP/FT-10 control modules, the recommended metal standoff height is
0.56 inch (14.3 mm) to provide adequate clearance. Note that the Methode
Socket (referenced in Table 6) in this case is not recommended, because its
minimum insertion depth requirement is not met. Use of metal 0.50 inch (12.7
mm) #6 standoffs together with metal spacers can achieve this. Alternately,
metal 0.56 inch (14.3 mm) #6 standoffs alone will be adequate. For the TP/XF
and TP/FT-10F control modules, 0.50 inch (12.7 mm) #6 metal standoffs alone are
recommended.
Figure 8 on page 12 presents the height restrictions of the component side of the
control module. The board is divided into two height zones: the maximum height
of components in the first zone is 0.20 inch (5.1 mm). The second zone's
components are 0.47 inch (11.93 mm) for the TP/XF and TP/FT-10F control
modules and 0.555 inch (14.1 mm) for the TP/FT-10 control module. Care should
be taken to ensure that no components on the application electronics board
interfere with the height restricted areas of the control modules.
Figure 9 on page 13 shows the recommended PCB pad layout for the application
electronics board to interconnect a control module with an application board that
has socket strips mounted on the component side.