Troybie shooting – Sears 113.21308 User Manual
Page 23
Attention! The text in this document has been recognized automatically. To view the original document, you can use the "Original mode".
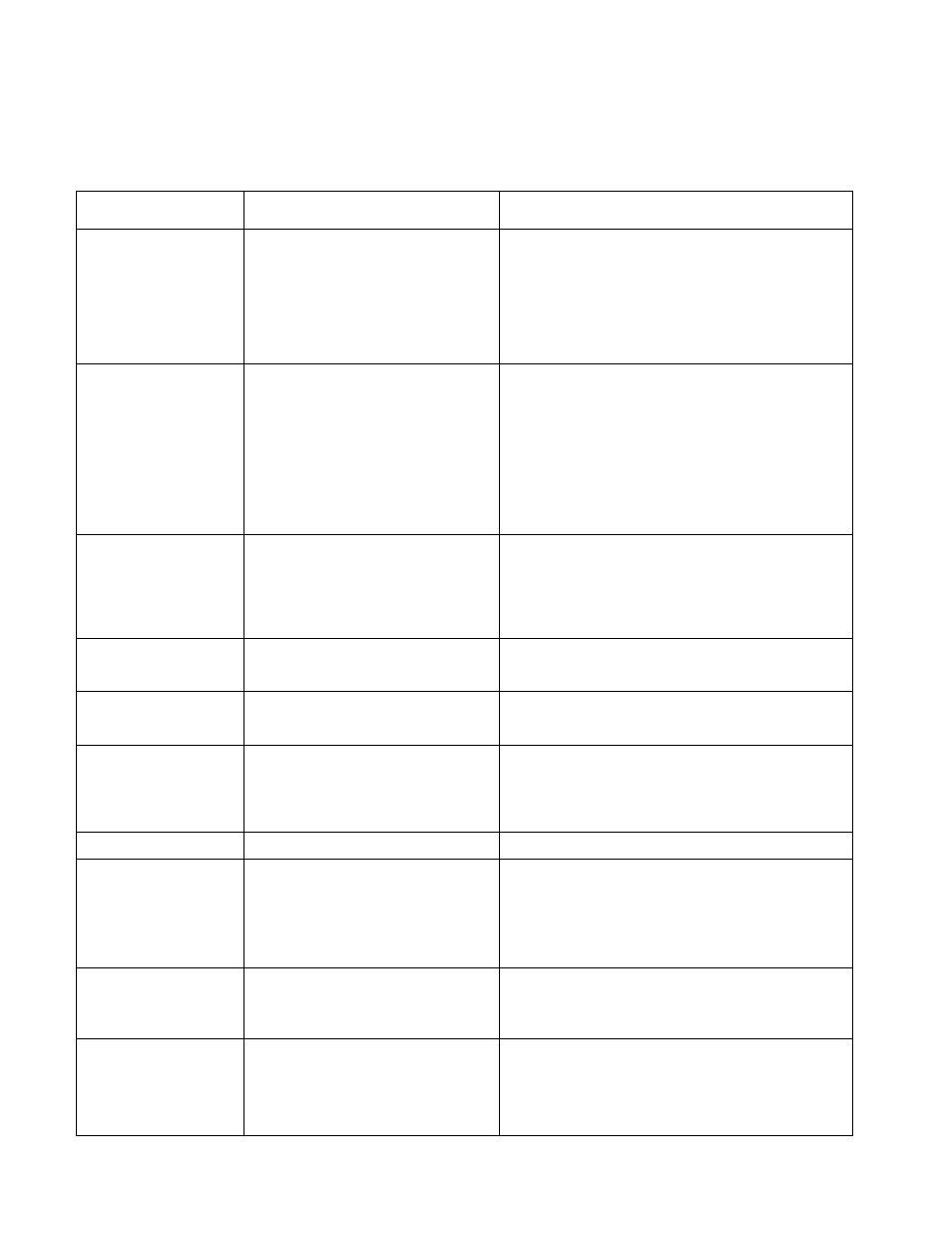
troybie shooting
WARNING; FOR YOUR OWN SAFETY, TURN SWITCH "OFF" AND ALWAYS REMOVE PLUG FROM POWER
SOURCE OUTLET
BEFORE TROUBLE SHOOTING.
• CONSULT YOUR LOCAL SEARS SERVICE CENTER IF FOR ANY REASON MOTOR WILL NOT RUN.
TROUBLE
PROBABLE CAUSE
REMEDY
. . ...............
Noisy Operation
j
1
. Incorrect belt tension,
2. Dry Spindle,
3. Loose spindle pulley,
4. Loose motor pulley.
1. Adiust tension. See section
' "ASSEMBLY-TENSIONING BELT."
2, Lubricate spindle. See “Lubrication"
section.
3. Checking tightness of retaining nut on
pulley, and tighten if necessary.
4, Tighten setscrews in pulleys.
Drill Burns
1. Incorrect speed,
2. Chips not coming out
of hole.
3. Dull Drill.
4. Feeding too slow,
5. Not lubricated.
1, Change speed. See section “Getting
To Know Your Drill Press".,,
DRILLING SPEED.
2, Retract drill frequently to clear chips.
3, Resharpen drill.
4, Feed fast enough ,, , allow drill to cut.
5, Lubricate drill. See “Basic Drill Press
Operation" section.
1 Drill leads off...
1 hole not round.
1, Hard grain in wood or
lengths of cutting
lips and/or angles
not equal.
2. Bent drill bit.
1. Resharpen drill correctly,
2. Replace drill bit.
Wood splinters on
underside.
1. No “back-up material’'
under workpiece.
1. Use “back-up material",., See Basic
Drill Press Operation" section.
Workpiece torn
loose from hand.
1. Not supported or
clamped properly.
1. Support workpiece or clamp it... See
“Basic Drill Press Operation" section.
Drill Binds in
workpiece.
1. Workpiece pinching drill
or excessive feed pressure.
2. Improper belt tension.
1. Support workpiece or clamp it... See
“Basic Drill Press Operation" section.
2. Adjust tension .,. See section
“ASSEMBLY-TENSIONING BELT."
Excessive drill
1. Bent drill.
1. Use a straight drill.
runout or wobble.
2. Worn spindle bearings.
3. Drill not properly
installed in chuck.
4. Chuck not properly installed.
2. Replace bearings,
3. Install drill properly... See “Basic
Drill Press Operation" section.
4. Install chuck properly.,. refer to
“Unpacking and Assembly Instructions
. ,. INSTALLING THE CHUCK,"
Quill Returns
too slow or too
fast.
1. Spring has improper tension.
1. Adjust spring tension .,. See section.
“Adjustments—Quill Return Spring.”
Chuck will not stay
attached to spindle
it falls off when
trying to install it.
1. Dirty, grease, or oil on the
tapered inside surface of chuck-
oronthe spindles tapered
surface.
1. Using a household detergent-dean the
tapered surface of the chuck and spindle to
remove a!i dirt, grease and oil
o>
8
Jtz
m
m
23