Check refrigerant feed components, Check compressor protection devices – Carrier 30H User Manual
Page 7
Attention! The text in this document has been recognized automatically. To view the original document, you can use the "Original mode".
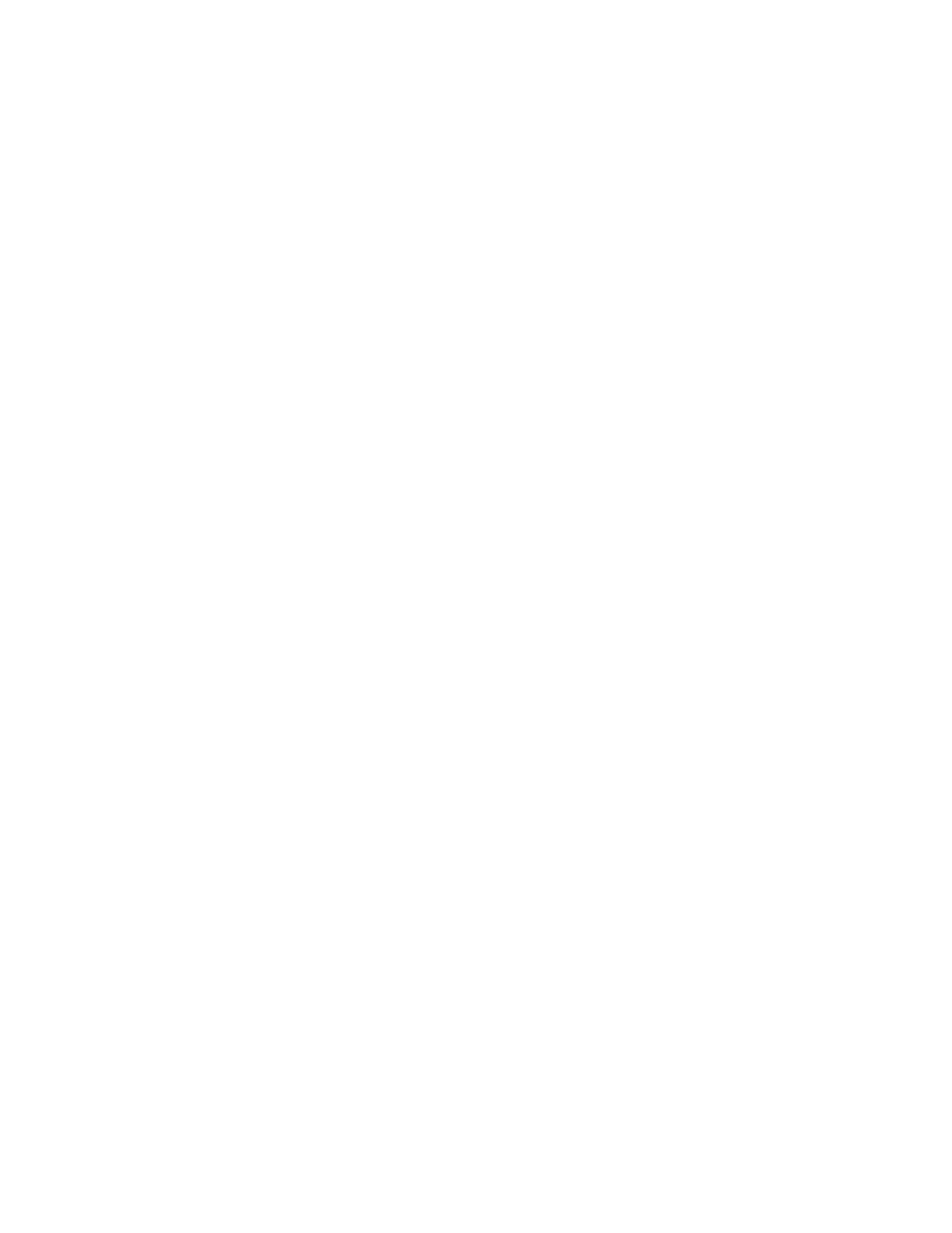
5. Check leaving chilled water temperature to see
that it remains well above freezing.
6. Recheck compressor oil level (see Check Oil
Charge).
7. Be sure unit is fully charged (see Check Refrig
erant Charge).
Check Refrigerant Feed Components
THERMOSTATIC
EXPANSION
VALVE
(TXV)
One valve for each refrigerant circuit is used to
control
the
flow
of
refrigerant.
The
valve
is
activated by a temperature sensing bulb clamped to
the suction line. The valve is factory-set to main
tain a superheat of 8 F to 10 F.
Do not change setting
unless absolutely necessary.
FILTER-DRIER (replaceable core type)
The function of the filter-drier is to maintain a
clean, dry system. The moisture indicator (below)
can indicate any need to change the filter-drier.
Additional
pressure-relief
valves,
properly
selected,
must
be
field
installed
to
protect
field-
installed high side equipment as may be required by
applicable codes.
A fusible plug is factory installed on each suction
line for low-side protection. This plug will relieve
on temperature rise to 170 F.
Most local codes require that a relief valve be
vented directly to outdoors.
The vent line must not
be smaller than the size of the relief valve outlet.
Check Compressor Protection Devices
CIRCUIT BREAKER
Each
compressor
is
protected
against
an
over-
current
condition
by
a
manual-reset
calibrated-trip
circuit breaker.
iMi*i)R ! \N T; i)n not b\ pa>v connections or
increase the size ot i.nc breaker to ct.'rrcci
trouble. Determine the cause and correct before
resetting breaker.
MOISTURE-LIQUID INDICATOR
The indicator is located immediately ahead of the
TXV
to
provide
a
constant
indication
of
the
moisture content of the refrigerant. It also provides
a sight glass for refrigerant liquid. Clear flow of
liquid refrigerant indicates sufficient charge in the
system.
Bubbles
indicate
under-charged
system
or
presence of noncondensables. Moisture in the sys
tem,
measured
in
parts
per
million
(ppm),
will
change color of indicator.
Unit must be in operation at least 12 hours before
moisture indicator will give an accurate reading.
With unit running, indicating element must be in
contact with liquid refrigerant to give true moisture
indication.
At the first sign of moisture in the system, change
the filter-drier. The color
BLUE indicates a safe,
dry condition and
PINK shows that a dangerous
moisture level is present. The first sign of moisture
would be a
LIGHT VIOLET color.
LIQUID LINE SERVICE VALVE
This valve provides a refrigerant charging port
and, in combination with the compressor discharge
service valve, allows the refrigerant to be pumped
into the high side.
PRESSURE RELIEF DEVICES
A
high-side
pressure-relief
valve
is
factory
in
stalled on each tower condenser. The valve is set to
open at a maximum pressure of 385 psig (maximum
design working pressure of the condenser).
DISCHARGE TEMPERATURE
THERMOSTAT
A sensor in the discharge side of each com
pressor reacts to excessively high discharge gas tem
perature and shuts off the compressor. The high
discharge gas temperature is a direct indication of
an
overtemperature
condition
in
the
motor
windings.
CRANKCASE HEATER
The heater in each compressor prevents absorp
tion
of
liquid
refrigerant
by
the
oil
when
the
compressor is not operating.
CM ! ION; 1 :ie licalc;'. wisich is held ;n place
by
a bracket, must be tight to prevent it from
backing out of the crankcase. The heater will
burn
out if exposed to air for an extended time.
Each 125-watt electric heater is wired into the
115-volt
control
circuit
thru
the
normally
closed
contacts of the control relay in such a way that it is
energized
only
when
the
compressor
is
not
operating.
C.\i. • ¡ON. Never ope:; any svUten or discon
nect that -Aill de-encrei/c the crankcase heater
unlcs.s the unit Is being serxiced or will be shut
down for a proic-nged period. Alter such ser\ ice
or prolonged shutdown, cnergi/c the crankcase-
heater
for 24 hours before starting the
comnrcssor.
TIME GUARD® CONTROL
This
control
protects
the
compressor
against
short cycling (switch A on four-function timer).