Initial check, Start-up and service, Warning – Carrier 30H User Manual
Page 5: Power, Before proceeding with, Shut, Unit, Any service work. initial check
Attention! The text in this document has been recognized automatically. To view the original document, you can use the "Original mode".
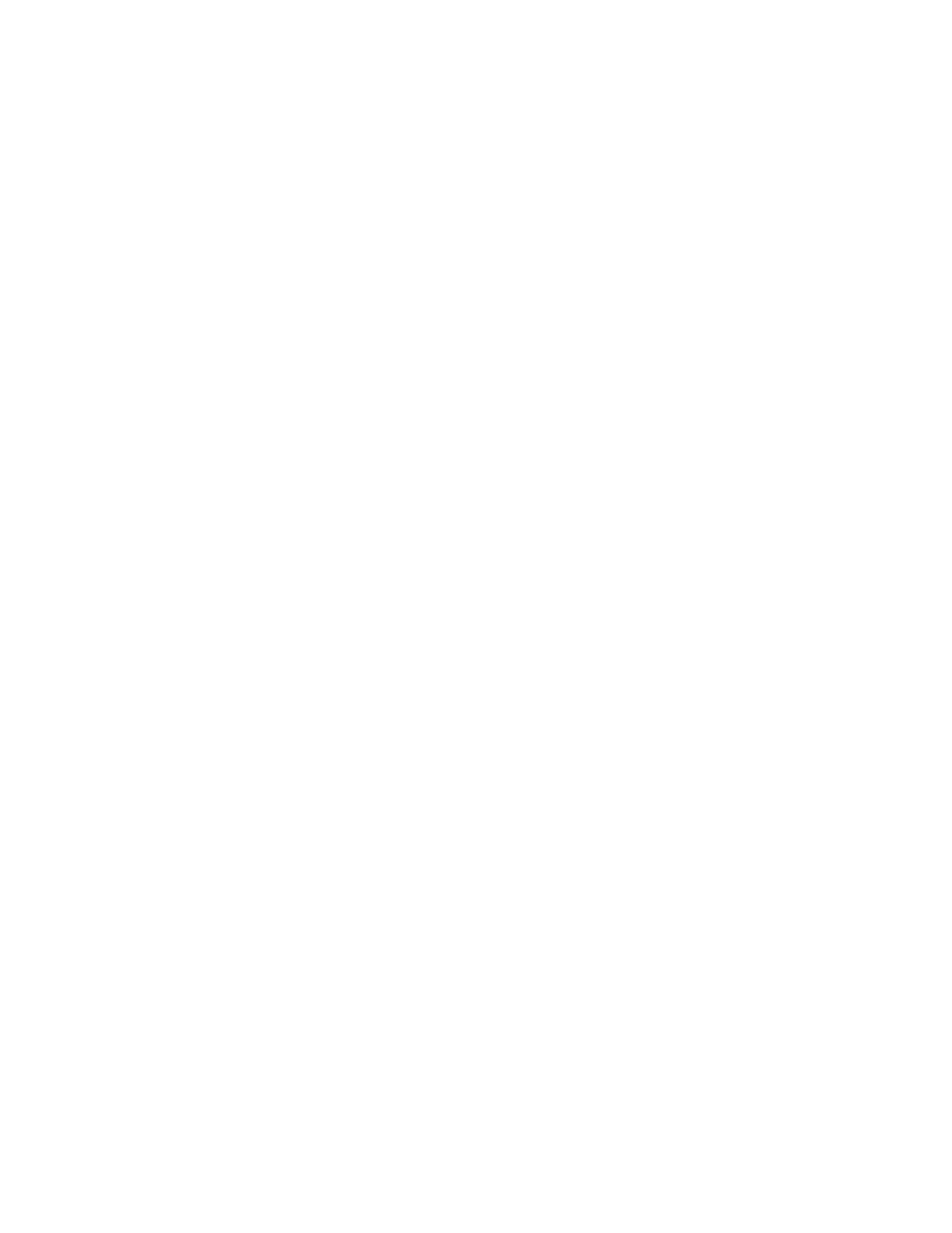
COMPLETE UNIT
Table 4 — Electrical Data; 3-Phase, 60-Hertz
Nameplate
VOLTS
200
230
460
575
06E COMPR
Supply Range"
180-229
207-264
414-528
518-660
USAGEt
Max
Max
Max
Max
UNIT 30
MKW
MCA
Fuse
MCA
Fuse
MCA
Fuse
MCA
Fuse
Cl rcuit
Amps
Amps
Amps
Amps
l' (
l
(^''' 2'{R) /^
040
50.4
194
250
167
225
84
110
68
90
B250 B250
H 050
61.1
230
300
207
300
104
150
84
125
I
J275 B250
060
71.8
259
350
239
300
120
150
97
125
J275 ; J275
INDIVIDUAL COMPRESSORS
COMPR
200 V
230 V
460 V
... 575........................
UNIT 30
nctr KW
06 E
RLA
LRA
; MTA
RLA LRA
MTA
RLA
LRA
MTA RLA
LRA MTA
; 040
250 (2) 25 2
86
345
; eo..;
74 300
102
37
150
50
30
120 42
275 (L) 35.9
11 5
506
' 80 "
106 440
"i 72.......... ''
53
220
73
43
176 58
П L/OU
250 (R) 25.2
86
345
74 300
;
102
37
150
50
30
;
120 42
060
275 (2) 35.9
115
506
Í" 80"
106 440
1......72 ' 1
53
220
73
43
176
:
58
6-Pole Breakers: values shown are for each 3-poie
section.
KW — Maximum Power Input (compressor)
LRA — Locked Rotor Amps
MCA — M inimum Circuit Amps. Complies with National Elec
trical Code (NEC), Section 430-24.
MKW — Unit Power Input at operating conditions of 50 F Leaving
Chilled
Water
Temperature
(44
F
Saturated
Suction
Temperature)
and
145
F
Saturated
Discharge
Temperature.
MTA — Must Trip Amps (Factory-installed circuit breaker)
RLA — Rated Load Amps
*Untts are suitable for use on electrical systems where voltage
supplied to the unit terminals is not below or above the range
limits shown.
fPrefix: B, J = 1 electric unloader.
ELECTRICAL
BOX
CONTROL
SECTION
Inside this section are: relays, high- and low-
pressure
cut-outs,
low
water-temperature
cut-out,
timer,
terminal
strips
and
a
4-step
temperature
controller. On the outside (control panel) are: con
trol
circuit
ON-OFE
switch,
partial
load
switch,
compressor
transfer
switch,
compressor
run
light,
safety trip lights and control circuit fuse. The control
panel is hinged to provide easy access to the controls
inside.
ELECTRICAL BOX, POWER SECTION
The main electrical power supply is brought in
thru the top of the electrical box, on the left-hand
side (see Fig. 1). The hole is suitable for accommo
dating
3-in.
conduit.
Pressure-lug
connections
on
the terminal block are suitable for copper, copper-
clad aluminum or aluminum wire.
In this section are: main power terminal block,
compressor
circuit
breakers
with
calibrated
mag
netic
trip
(for
compressor
motor
overload
and
locked rotor protection) and compressor motor con
tactors. The panel over this section is secured with
screws as a safety measure against casual entry for
purposes other than service.
START-UP AND SERVICE
WARNING:
Shut
off
all
power
to
the
unit
before proceeding with
any service work.
INITIAL CHECK
Do not start the liquid chiller even momentarily
until the following steps have been completed.
1.
Check all auxiliary components such as chilled
liquid circulating pump, cooling tower if used,
air handling equipment, or other equipment to
which the chiller supplies liquid. Consult the
manufacturer’s instructions.
2.
Check
safety
thermostat.
See
Safety
Thermostat.
3.
Determine if there is a refrigerant charge in the
system. See Check Refrigerant Charge.
4.
Backseat (open) compressor suction and dis
charge shutoff valves.
5. Open liquid line shutoff valves.
6.
Fill chilled liquid circuit completely with clean
water or other noncorrosive fluid to be cooled.
Bleed all air out of high points of system.
7. Fill cooling tower for condenser cooling water.
8. Set temperature controller.
9. Check tightness of all electrical connections..
10.
Check
compressor
oil
(should be
visible in
bull’s-eye). Refer to Check Oil Charge.
11.
Be sure crankcase of each compressor is warm
(heaters
should
be
on
for
24
hours
before
starting compressors).
12.
Be sure compressors are floating freely. See
INSTALLATION, Step 3.