4 common vent test — boilers, 1 gas supply and piping – LAARS Rheos RHCV - Install and Operating Manual User Manual
Page 15
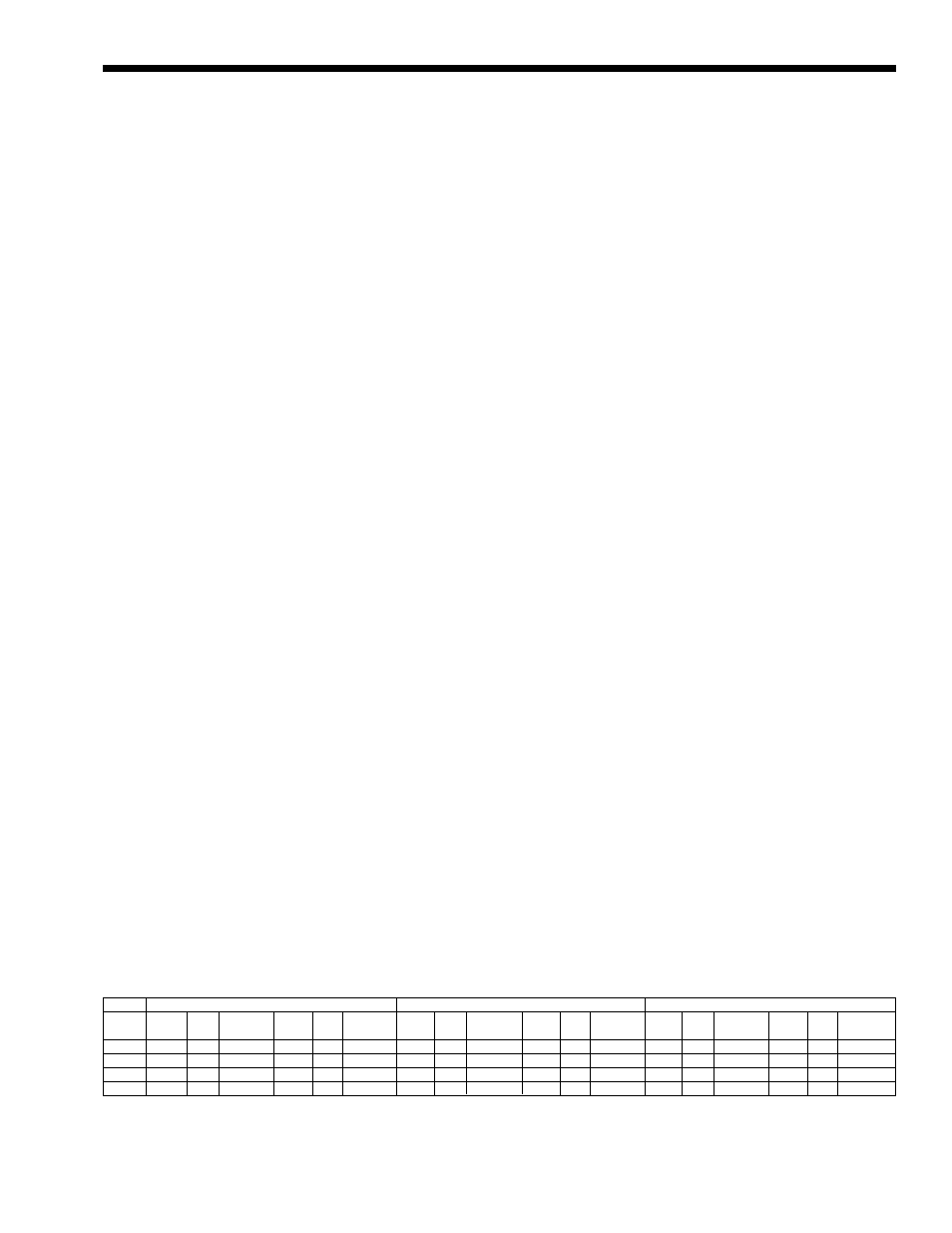
Rheos Boiler and Water Heater
Page 15
2.3.4 Vertical Combustion Air Terminal
When combustion air is taken from the roof, a
field-supplied rain cap or an elbow arrangement must
be used to prevent entry of rain water (see Figure 2).
The opening on the end of the terminal must be at least
12" (30cm) above the point at which it penetrates the
roof, and high enough above the roof line to prevent
blockage from snow. When the vent terminates on the
roof, the combustion air must terminate at least 12"
(30cm) below the vent terminal.
2.4 Common Vent Test — Boilers
NOTE: This section does not describe a method for common
venting Rheos units. It describes what must be done when a unit is
removed from a common vent system. Rheos units require special
vent systems and fan for common vent. Contact the factory if you
have questions about common venting Rheos units.
When an existing boiler is removed from a
common venting system, the common venting system
is likely to be too large for proper venting of the
appliances remaining connected to it.
At the time of removal of an existing boiler, the
following steps shall be followed with each appliance
remaining connected to the common venting system
placed in operation, while the other appliances
remaining connected to the common venting system
are not in operation.
1. Seal any unused openings in the common venting
system.
2. Visually inspect the venting system for proper
size and horizontal pitch and determine there is
no blockage or restriction, leakage, corrosion and
other deficiencies which could cause an unsafe
condition.
3. Insofar as it is practical, close all building doors
and windows and all doors between the space in
which the appliances remaining connected to the
common venting system are located and other
spaces of the building. Turn on clothes dryers
and any appliance not connected to the common
venting system. Turn on any exhaust fans, such
as range hoods and bathroom exhausts, so they
will operate at maximum speed. Do not operate a
summer exhaust fan. Close fireplace dampers.
4. Place in operation the appliance being
inspected. Follow the lighting instructions.
Adjust thermostat so appliance will operate
continuously.
5. Test for spillage at the draft hood relief opening
after 5 minutes of main burner operation. Use
the flame of a match or candle, or smoke from a
cigarette, cigar or pipe.
6. After it has been determined that each appliance
remaining connected to the common venting
system properly vents when tested as outlined
above, return doors, windows, exhaust fans,
fireplace dampers and any other gas burning
appliance to their previous conditions of use.
7. Any improper operation of the common venting
system should be corrected so that the installation
conforms to the National Fuel Gas Code, ANSI
Z223.1/NFPA 54 and/or CSA B149.1, Installation
Codes. When resizing any portion of the common
venting system, the common venting system
should be resized to approach the minimum size
as determined using the appropriate tables in Part
II of the National Fuel Gas Code, ANSI Z223.1
NFPA 54 and/or CSA B149.1, Installation Codes.
SECTION 3.
Gas Supply and Piping
3.1 Gas Supply and Piping
Gas piping should be supported by suitable
hangers or floor stands, not the appliance.
Review the following instructions before
proceeding with the installation.
1. Verify that the appliance is fitted for the proper
type of gas by checking the rating plate. Laars
Heating Systems appliances are normally equipped
to operate at elevations up to 2000 feet (610m).
However, the appliance will function properly
without the use of high altitude modification at
elevations up to 10,000 feet (3050 m).
2. The maximum inlet gas pressure must not exceed
13" W.C. (3.2kPa). The minimum inlet natural
gas pressure is 4" W.C. (1.0kPa) and minimum
inlet propane gas pressure is 6" (1.5kPa).
3. Refer to Table 7, size supply.
Hard Water
Normal Water
Soft Water
Model Flow H/L Temp
Flow H/L Temp
Flow H/L Temp
Flow H/L Temp
Flow H/L Temp
Flow H/L Temp
(Size)
gpm feet Rise (°F) lpm
m Rise (°C) gpm feet Rise (°F) lpm
m Rise (°C) gpm feet Rise (°F) lpm
m Rise (°C)
1200
119
20
18
449 6.1
10
93
12
23
351 3.7
13
65
6.0
32
246 1.8
18
1600
161
29
17
609 8.8
10
132
20
21
500 6.1
12
89
8.9
31
336 2.7
17
2000
182
22
19
690 6.7
11
149
15
23
565 4.6
13
100 6.6
35
379 2.0
19
2400
237
23
18
898 7.0
10
186
14
23
703 4.3
13
129 6.9
32
488 2.1
18
Note:
Soft Water: 1 to 7.5 grains per gallon
Note: Headloss is for heater’s heat exchanger only.
Normal Water: 7.6 to 17 grains per gallon
Hard Water: More than 17 grains per gallon
Table 9. Water Flow Requirements, RHCV (Water Heater).