Instruction manual tu_us, Sauter gmbh – KERN & SOHN TU 300-0.01US User Manual
Page 6
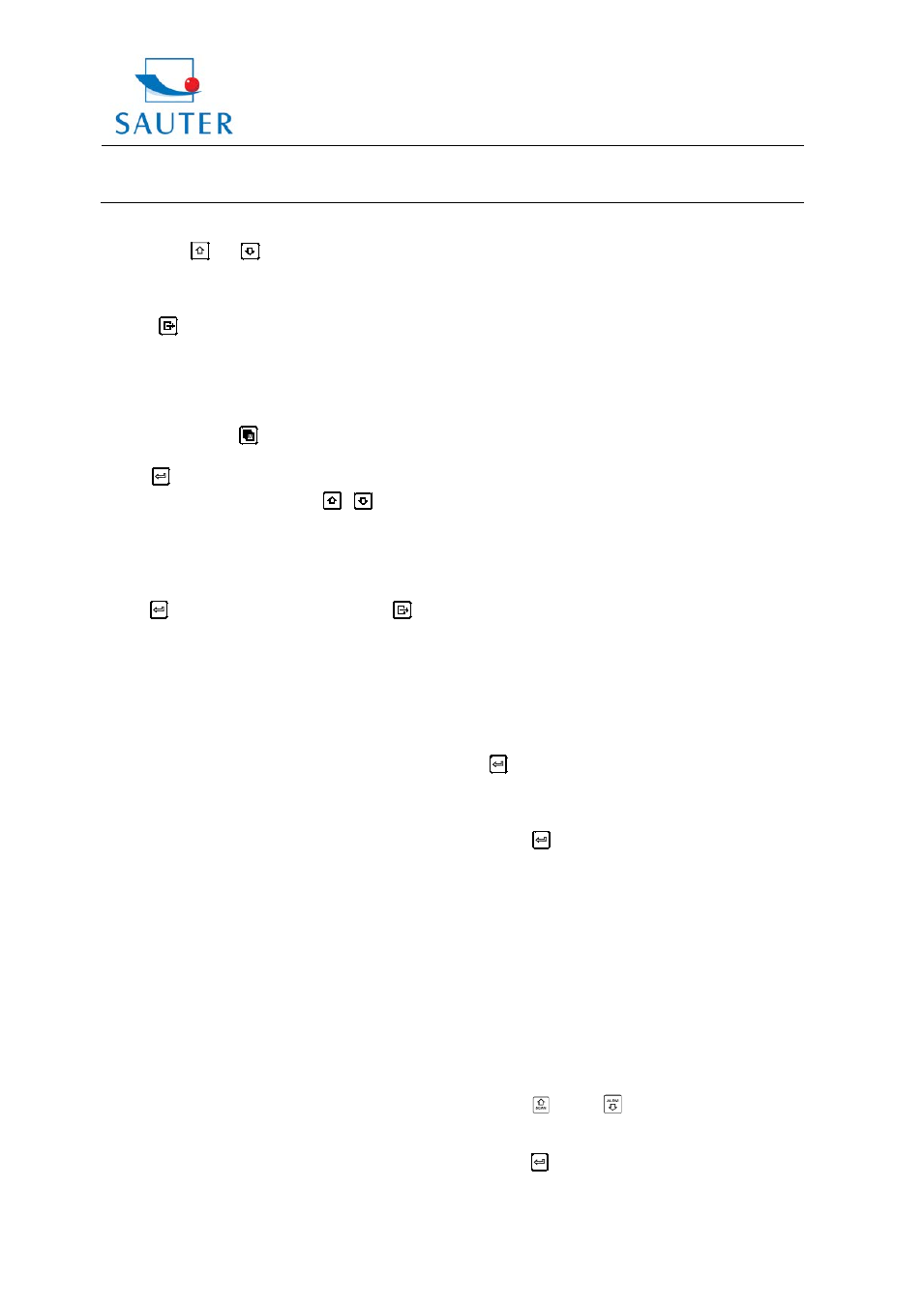
Sauter GmbH
Ziegelei 1
D-72336 Balingen
E-Mail: [email protected]
Tel: +49-[0]7433- 9933-199
Fax: +49-[0]7433-9933-149
Internet: www.kern-sohn.com
Instruction Manual
TU_US
TU_US-BA-e-1212
6
velocity value can be overwritten, if essential, up or down
with the keys
and
until the sound velocity of the
material to be measured is matched. This value may be
above or below the preset sound velocity for a special
material (see table in Appendix A).
3. The
key has to be pressed to exit from the
calibration mode. The instrument is now ready to perform
measurements.
Another method to set the instrument with a known sound
velocity is as follows:
1) The submenu item 【 Test Set】 ->【 Velocity Set】 has to
be highlighted and the
key has to be pressed to enter
the sound velocity set screen.
2) The
key has to be pressed multiple times to tab to
the numeric digit to be changed. The
/
keys have
to be used to increase/ decrease numeric values on the
display until the sound velocity of the material being
measured is matched. An auto repeat function is built in,
so that when the key is held down, numeric values will
increment/ decrement at an increasing rate.
3) The
key has to be pressed to confirm or the
key
hast to be pressed to cancel the calibration.
To achieve the most accurate measurement results, it is
generally advisable to calibrate the instrument to a sample
piece of known thickness. The composition of materials
(and thus, its sound velocity) sometimes varies from lot to
lot and from manufacturer to manufacturer.
Calibration to a sample of known thickness ensures that
the instrument is set as closely as possible to the sound
velocity of the material being measured.
4.5 How to perform measurements
The instrument always stored the last measured value until
a new measurement is made. In order for the transducer
working in the right way there may not be any gaps
between the contact area of the sensor and the surface of
the material being measured. This is accomplished with
the coupling fluid, commonly called “couplant”. This fluid
serves to “couple” or transfer the ultrasonic sound waves
from the transducer, into the material and back again.
Therefore a small amount of couplant should be applied
onto the surface of the material, before measurements are
performed. Typically, a single droplet is sufficient.
After the couplant is applied, the transducer has to be
pressed firmly against the area being measured. The
coupling status indicator should appear on the display as
well as a digit number. If the instrument has been “zeroed”
properly and if it has been set to the correct sound velocity,
the actual thickness of the material directly beneath the
transducer will be indicated as a number in the display.
If the coupling status indicator doesn’t appear or if it isn’t
stable or if the numbers on the display doesn’t seem to be
correct, it has to be checked whether there is an adequate
film of couplant beneath the transducer and whether the
transducer is placed flat onto the material.
If conditions persist, sometimes it is necessary to select a
different transducer (size or frequency) for the material
intended to be measured.
While the transducer is in contact with the material, the
instrument will perform four measurements every second,
updating its display as it does so.
If the transducer is removed, the display will hold the last
measurement performed.
Note: Occasionally a small film of couplant will be drawn
out between the transducer and the surface, as the
transducer is removed. If this happens, the instrument may
perform a measurement through this couplant film,
resulting in an erroneously measurement. This is
comprehensible because one thickness value is observed
while the transducer is in place and the other value is
observed after the transducer is removed.
In addition, measurements performed through very thick
paint or coatings may result in the paint or coating being
measured rather than the material intended.
The responsibility for a proper use of the instrument, as
well as the recognition of these types of phenomenon
solely depend on the user of this instrument.
4.6 Two-point Calibration
Note: This procedure requires that the testing person has
got two known thickness points on the test piece which are
representative of the range being measured.
1) On the 【 Test Set】 ->【 2-Point Cal】 submenu item the
key has to be pressed to switch ON the Two-point
mode. The exit from the menu to the measurement screen.
The string “DPC” will appear on the operation hint area of
the main measurement screen.
2) The
key has to be pressed to start the calibration
procedure. The string “NO1” will appear on the operating
hint area, indicating measuring the first point.
3) A small amount of couplant has to be applied to the
sample piece.
4) The transducer has to be pressed against the sample
piece at the first / second calibration point. It has to be
made sure that the transducer is placed flat on the surface
of the sample. Now the display should show any (probably
incorrect) thickness value and the coupling status indicator
should appear steadily.
5) As soon as a stable measurement is achieved, the
transducer is to be removed. If the displayed thickness
distinguishes from the value shown while the transducer
was coupled, step 4 is to be repeated.
6) The
and the
key are to be used to adjust the
material thickness up and down until it matches the
material thickness of the sample piece.
7) The
key has to be pressed to confirm. The hint will
change to “NO2” indicating to be ready to measure the
second calibration point.