2 using bac valves/solenoids, 4 dual intake valve control (div) – Haltech F10 User Manual
Page 80
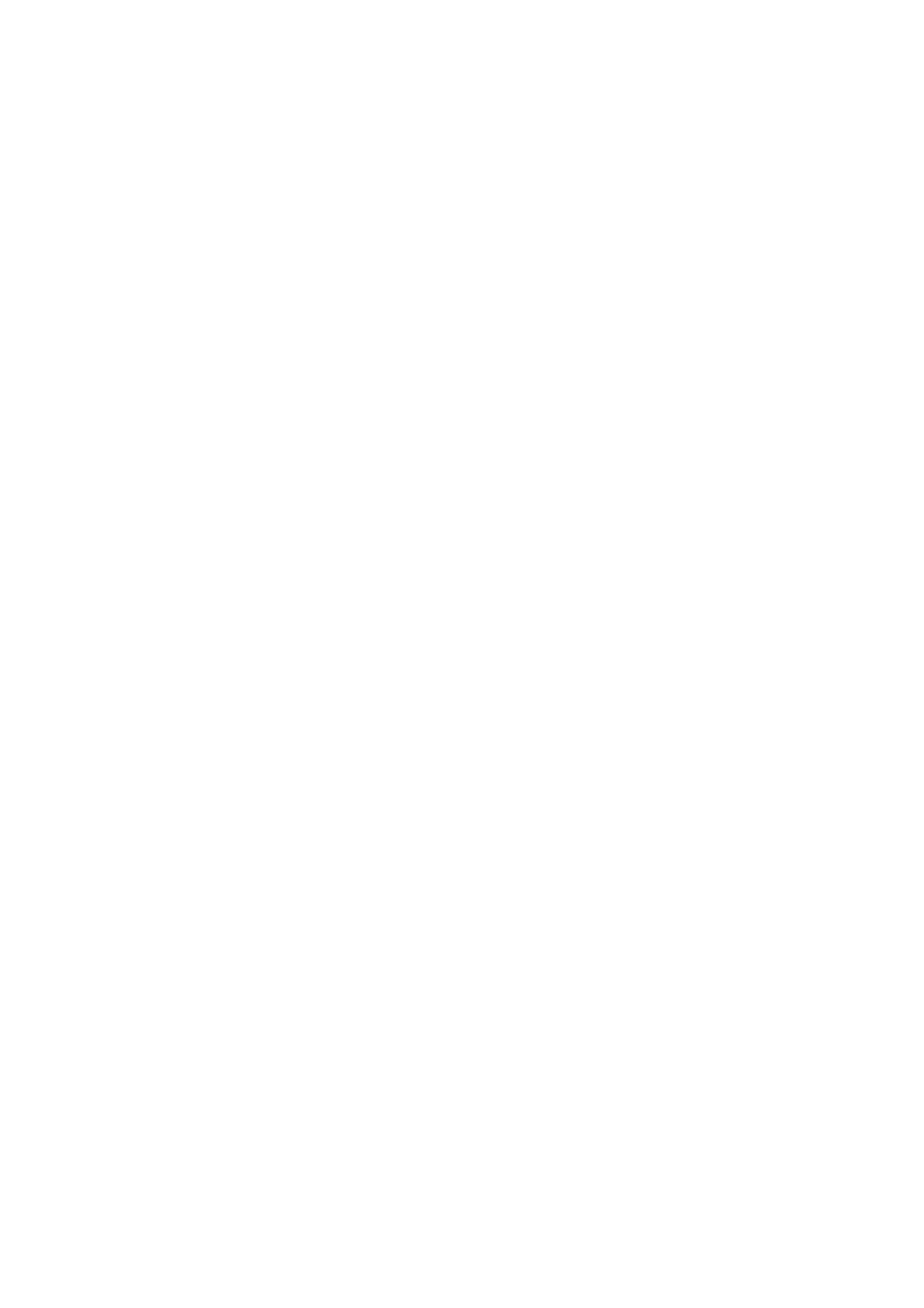
75
The operation is fairly straightforward: each BAC solenoid/valve will have its own operating
frequency. By continually operating the valve at this frequency, you can then vary the duty
cycle to move the valve in or out. The duty cycle will therefore vary from 0 to 100% whilst
the operating frequency is maintained constant.
16.3.2 Using BAC Valves/Solenoids
The BAC settings are mostly done in the Idle Air Control section on the Output Options Page.
Firstly, set a PWM output to operate as BAC and set the operating period. Then go to the
Output Options Page. Select the Idle Air Control. Note that the Idle Speed will be disabled
because you are using a BAC output to do Idle Control and not an IAC Stepper motor. Go
through the settings as you would do if you were configuring Idle Control for a stepper motor.
A full description of the procedure is available in Section 14.2. Remember that you are using
a BAC valve/solenoid and not a stepper motor so not all of the settings in 14.2 will relate to
BAC.
16.4 Dual Intake Valve Control (DIV)
Some late model engines possess two tuned intake manifolds. One intake tract remains shut at
lower rpm where there is less airflow, then opens as airflow demands increase. This provides
a broader torque curve. The DIV function controls the solenoid that operates this valve.
In order to use the DIV function, you will need the following:
- a two wire solenoid valve mounted in the air intake (already on the engine);
- F10 programming software and cable.
Wire the solenoid to the appropriate output, taking note of voltage polarity. (Some solenoids
are non-polar.) Run the F10 programming software in ONLINE mode and select the Dual
Intake Valve function on the appropriate channel. There are two values to be set.
Switch On RPM
This is the engine speed at which the solenoid is to be energised.
Switch Off RPM
This is the engine speed at which the solenoid is to be de-energised.
There are two ways in which this feature can be used:
The first application is to have two RPM ranges; one high and one low. In the lower range
the solenoid is disabled and in the upper range the solenoid is enabled. Using this application
the On RPM should be set to the lower RPM limit of the upper range and the Off RPM should
be set to at least 200 RPM below On RPM, forcing hysteresis in the switching to prevent the
solenoid from oscillating.
The second application is to enable the solenoid for a range of RPM and to disable the
solenoid when the RPM falls outside this range. To do this the On RPM is set to the lower
RPM limit of the range and the Off RPM is set at the upper RPM limit, when the RPM is
lower than On RPM the solenoid is disabled, when the RPM is greater than On RPM but less
than Off RPM the solenoid is enabled, when the RPM is greater than On RPM and Off RPM
then the solenoid is disabled.