Chapter 6 operating procedures, Input data – Hardy HI 1769-FC User Manual
Page 55
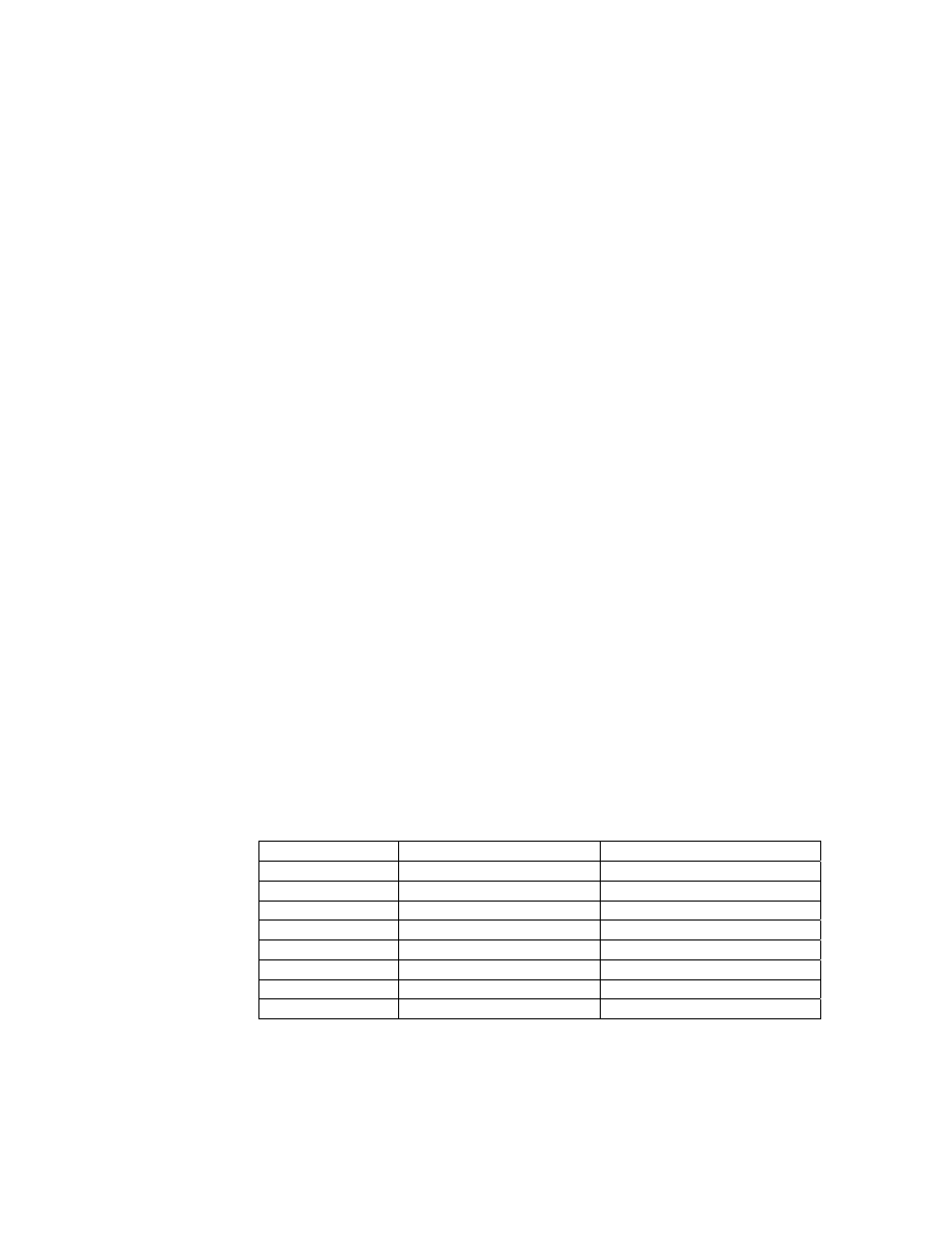
50
●
●
●
●
●
Chapter 7
Chapter 6 Operating Procedures
● ● ● ● ●
Information contained in Chapter 6 pertains to the operation of the HI 1769-FC Feeder
Control module. The Operating Procedures include reading data transferred to the PLC
from the Feeder Control module.
The HI 1769-FC module monitors load sensors for weight readings, refill process and
calculating a rate of change for material fed. Using PID calculations the module will
generate an output percentage to control the feeder motor in order to maintain the
requested rate of change. This Output Percentage will need to be re-directed to the feeder
motor control. The type of signal to the motor control will be determined by the motor
control of the feeder. This could be analog, either current or voltage, EIP, DeviceNet,
etc.
NOTE:
The HI 1769-FC module does not have any I/O. The user determines the type of motor
signal needed for their feeder control, provides the module and directs that signal to the
motor control.
The HI 1769-FC module does not have any input I/O. Signals from the Processor to run
commands like Start, Stop, Pause, etc. will need to be programed. These commands may
be generate by the user through inputs such as switches, buttons, HMI screens, etc. It is
the users responsibility to provide the method of inputting the signal from the user to the
PLC and ultimately to the HI 1769-FC module.
Input Data
This is the discrete input data which is in module defined data type, LOCAL:X:I (where
X is the slot number) or Local:X:I.CH0 (if using the Add on Profile (AOP)).
NOTE:
Word # is if the module is set up as a generic module, tag name is if the module is set up
using the AOP. If set up as a generic module, the 32 bit values use two word locations
and will be ordered as Least Significant Word (LSW) first and Most Significant Word
(MSW) second. If using the AOP, this will be a Double Integer (DINT) register.
AOP Tag Name
Input table word location
Description
OP
5
Output Percentage
ROC
6 & 7
Rate of Change
Gross
8 & 9
Gross Weight
Setpoint
10 & 11
ROC setpoint
ControllerState
12
State of module
Version
13
Firmware Version
ControllerStatus
14
Module Status
Counter
15
counter