Checkline ESM301 User Manual
Page 21
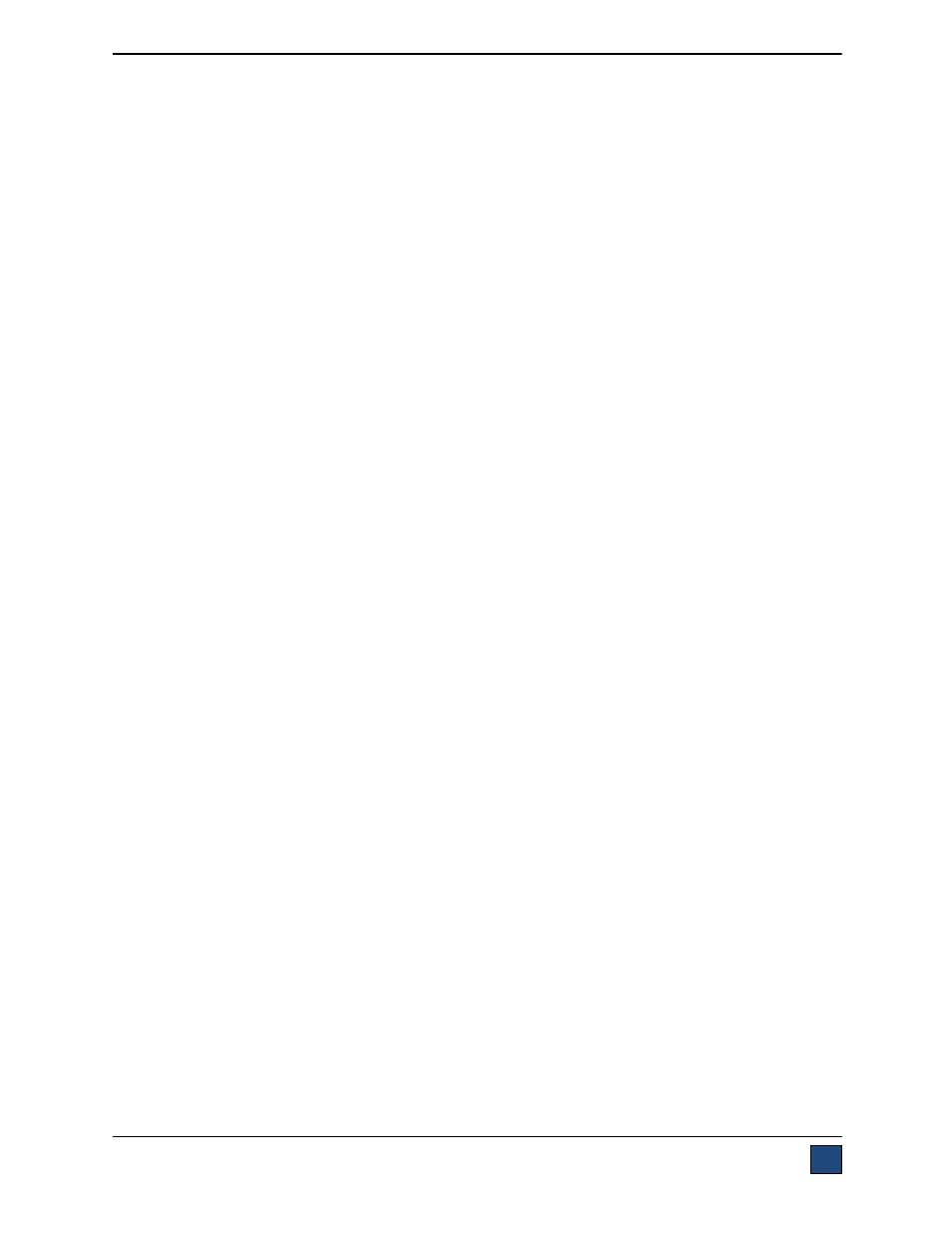
Model ESM301 / ESM301L Version 2 Test Stand
User’s Guide
21
lower limit switch.
Note 2: Preload
and Load Holding cannot be enabled simultaneously.
5.6 Load Holding Mode
In this mode, the crosshead moves until the set point value programmed in the force gauge is reached.
The crosshead then dynamically adjusts its position to maintain a programmed force. The force gauge’s
capacity should be as close as possible to the intended load, for best performance.
In the force gauge, both set points must be set. The upper set point refers to a force limit in the up
(tension) direction. The lower set point refers to a force limit in the down (compression) direction. The
opposite set point must be set to any value in the opposite measuring direction. For example, for a test
requiring load holding at 10 lbF of compression force, set the upper set point to 30 lbF tension (as an
example), and the lower set point to 10 lbF compression.
If the CYCLING option has been enabled, load holding will be active for the period of time as defined in
the Dwell Time settings. If CYCLING has not been enabled, load holding will continue indefinitely.
Before the start of a load holding sequence, the crosshead must be positioned at either the upper limit
switch to begin compression load holding or at the lower limit switch to begin tension load holding.
The test speed should be adjusted according to the sample under test. Fine tuning may be necessary to
ensure optimal crosshead dynamic adjustment. Stiff samples require a lower test speed; softer samples
can be tested at higher speeds. If the speed of approach is too high for a given sample stiffness, the
crosshead may overshoot the set point value, requiring an adjustment sequence where the crosshead
reverses, then moves again in the original direction multiple times before settling at the set point value. A
high enough speed may cause this correction cycle to repeat indefinitely.
For softer samples the amplitude of oscillation will be smaller, but could still be present for the duration of
the load holding period. This is typical for samples which may relax, such as rubber, foam, etc. Lowering
the test speed will reduce the oscillation.
For non-relaxing materials such as metal springs, the oscillation should stop shortly after the holding force
is reached.
Note: Preload
and Load Holding cannot be enabled simultaneously.
5.7 Break Detection Mode
In this mode, the crosshead will stop when a sample break has occurred. The test stand is triggered when
the force has decreased to a specified percentage of peak.
For example: A sample is pulled until 50 lbF, then breaks. The break detection percentage drop setting is
programmed to 50%. After the sample breaks, the force rapidly decreases, reaches 25 lbF (50% of peak),
then triggers the test stand to stop.
Break detection becomes active only after 5% of the force gauge’s full scale has been reached. For
example, if a force gauge with 50 lbF capacity is used, the break detection feature will not become active
until 2.5 lbF has been reached.
If enabled, an auto-return sequence or single-cycle sequence may follow break detection.
5.8 PC Mode
The ESM301 can be controlled by a PC via serial communication. A list of supported ASCII commands is
provided below. All commands must be lowercase.
a
Request speed
b
Set travel units to inches
c
Enter cycle mode