02 cleaning the feed rolls, 03 basic troubleshooting, 04 solving problems beyond the welding terminals – Tweco 350 4R Wirefeeder User Manual
Page 47
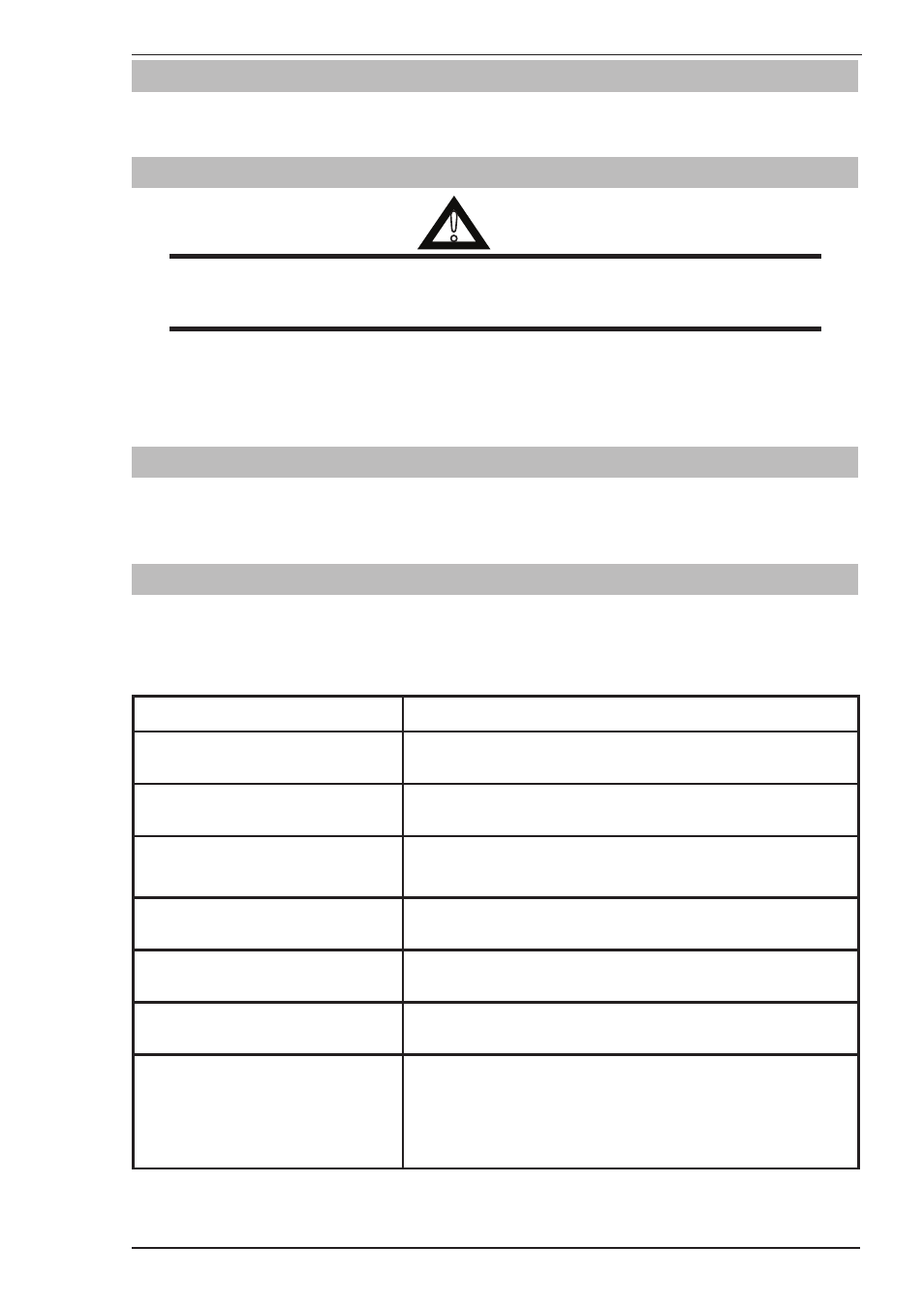
7-3
Manual 0-5182
service weldskill 250, 350
Service
7.02 Cleaning the Feed Rolls
Clean the grooves in the drive rolls frequently. This can be done by using a small wire brush. Also wipe off, or
clean the grooves on the upper feed roll. After cleaning, tighten the feed roll retaining knobs.
7.03 Basic Troubleshooting
!
WARNING
There are dangerous voltage and power levels present inside this product. Do not attempt to open
or repair unless you are a qualified electrical tradesperson and you have had training in power
measurements and troubleshooting techniques.
If major complex subassemblies are faulty, then the Welding Power Source must be returned to an Accredited
CIGWELD Service Provider for repair.
The basic level of troubleshooting is that which can be performed without special equipment or knowledge
and without removing the covers from the Wirefeeder.
7.04 Solving Problems Beyond the Welding Terminals
The general approach to fix Gas Metal Arc Welding (GMAW) problems is to start at the wire spool then work
through to the MIG torch. There are two main areas where problems occur with GMAW, Porosity and Incon-
sistent wire feed.
7.05 Solving Problems Beyond the Welding Terminals - Porosity
When there is a shielding gas problem the result is usually porosity within the weld metal. Porosity always stems
from some contaminant within the molten weld pool which is in the process of escaping during solidification
of the molten metal. Contaminants range from no shielding gas around the welding arc to dirt on the work
piece surface. Porosity can be reduced by checking the following points.
FAULT
CAUSE
1 Shielding gas cylinder contents
and flow meter.
Ensure that the shielding gas cylinder is not empty and the flow
meter is correctly adjusted to 15 litres per minute.
2 Gas leaks.
Check for shielding gas leaks between the regulator/cylinder
connection and in the shielding gas hose to the Power Source.
3 Internal shielding gas hose in the
Power Source.
Ensure the hose from the solenoid valve to the torch adaptor
has not fractured and that it is connected to the torch adaptor.
4 Welding in a windy environment.
Shield the weld area from the wind or increase the shielding
gas flow.
5 Welding dirty, oily, painted, oxidised
or greasy plate.
Clean contaminates off the work piece.
6 Distance between the MIG torch
nozzle and the work piece.
Keep the distance between the MIG torch nozzle and the work
piece to a minimum.
7 Maintain the MIG torch in good
working order.
A
B
C
Ensure that the shielding gas holes are not blocked and
shielding gas is exiting out of the torch nozzle.
Do not restrict shielding gas flow by allowing spatter to build
up inside the torch nozzle.
Check that the MIG torch O-rings are not damaged.