Fabricator 181i – Tweco 181i Fabricator User Manual
Page 73
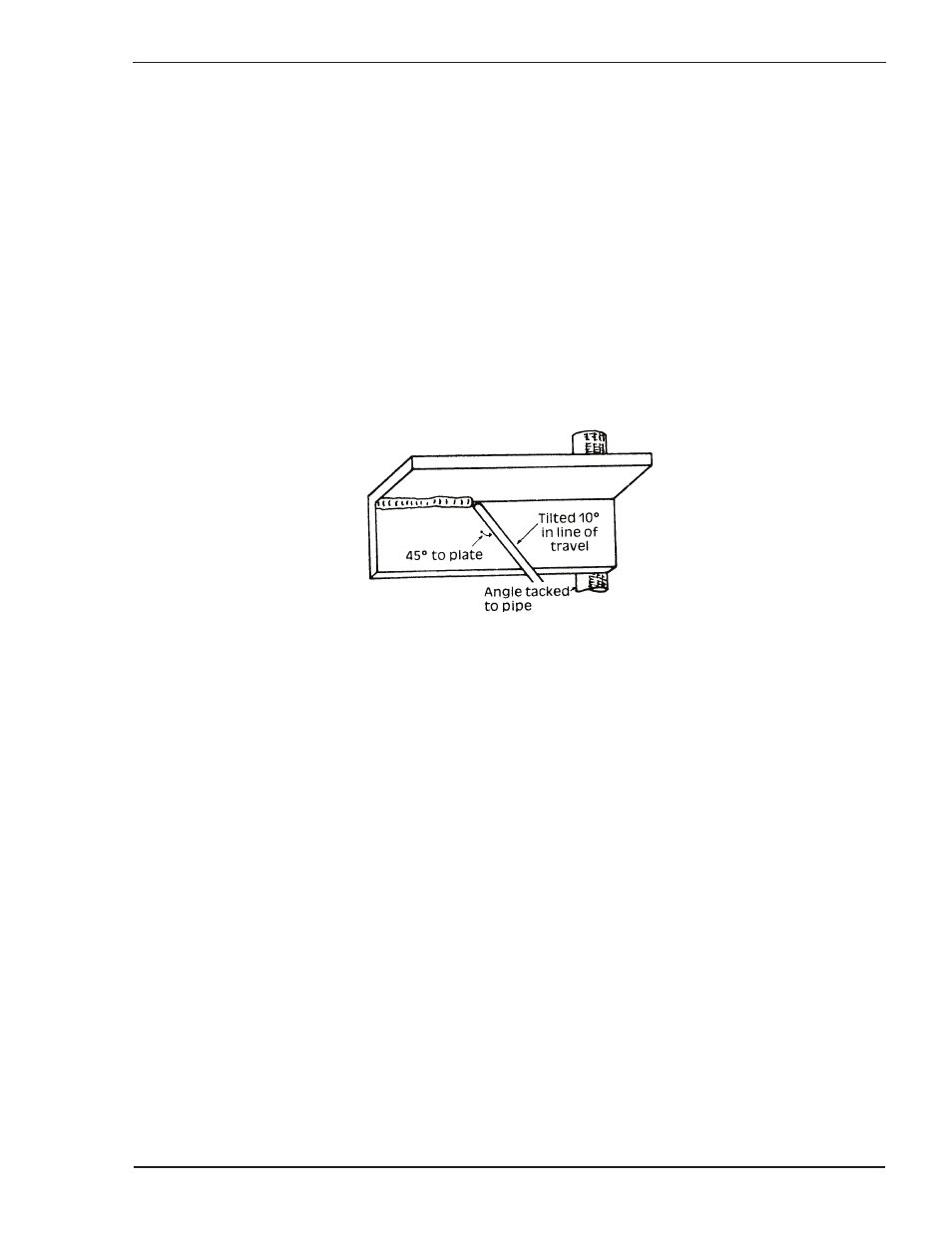
Fabricator 181i
Manual 0-5191
4-15
BASIC WELDING GUIDE
2. Vertical Down
The
E7014 Stick electrode makes welding in this position particularly easy. Use a 1/8"(3.2mm) electrode
at 100 amps. The tip of the electrode is held in light contact with the work and the speed of downward
travel is regulated so that the tip of the electrode just keeps ahead of the slag. The electrode should point
upwards at an angle of about 45º.
3. Overhead Welds
Apart from the rather awkward position necessary, overhead welding is not much more difficult that
downhand welding. Set up a specimen for overhead welding by first tacking a length of angle iron at right
angles to another piece of angle iron or a length of waste pipe. Then tack this to the work bench or hold in
a vice so that the specimen is positioned in the overhead position as shown in the sketch. The electrode
is held at 45º to the horizontal and tilted 10º in the line of travel (Figure 4-28). The tip of the electrode may
be touched lightly on the metal, which helps to give a steady run. A weave technique is not advisable for
overhead fillet welds. Use a 1/8"(3.2mm) E6013 Stick electrode at 100 amps, and deposit the first run by
simply drawing the electrode along at a steady rate. You will notice that the weld deposit is rather convex,
due to the effect of gravity before the metal freezes.
Art # A-07704
Figure 4-28: Overhead Fillet Weld
Distortion
Distortion in some degree is present in all forms of welding. In many cases it is so small that it is barely perceptible,
but in other cases allowance has to be made before welding commences for the distortion that will subsequently
occur. The study of distortion is so complex that only a brief outline can be attempted hear.
The Cause of Distortion
Distortion is caused by:
A. Contraction of Weld Metal:
Molten steel shrinks approximately 11 per cent in volume on cooling to room temperature. This means that a
cube of molten metal would contract approximately 2.2 per cent in each of its three dimensions. In a welded
joint, the metal becomes attached to the side of the joint and cannot contract freely. Therefore, cooling causes
the weld metal to flow plastically, that is, the weld itself has to stretch if it is to overcome the effect of shrinking
volume and still be attached to the edge of the joint. If the restraint is very great, as, for example, in a heavy
section of plate, the weld metal may crack. Even in cases where the weld metal does not crack, there will still
remain stresses "Locked-up" in the structure. If the joint material is relatively weak, for example, a butt joint
in 5/64" (2.0mm) sheet, the contracting weld metal may cause the sheet to become distorted.