Ultra-cut 100 xt – Tweco 100 XT Ultra-Cut Plasma Cutting System User Manual
Page 30
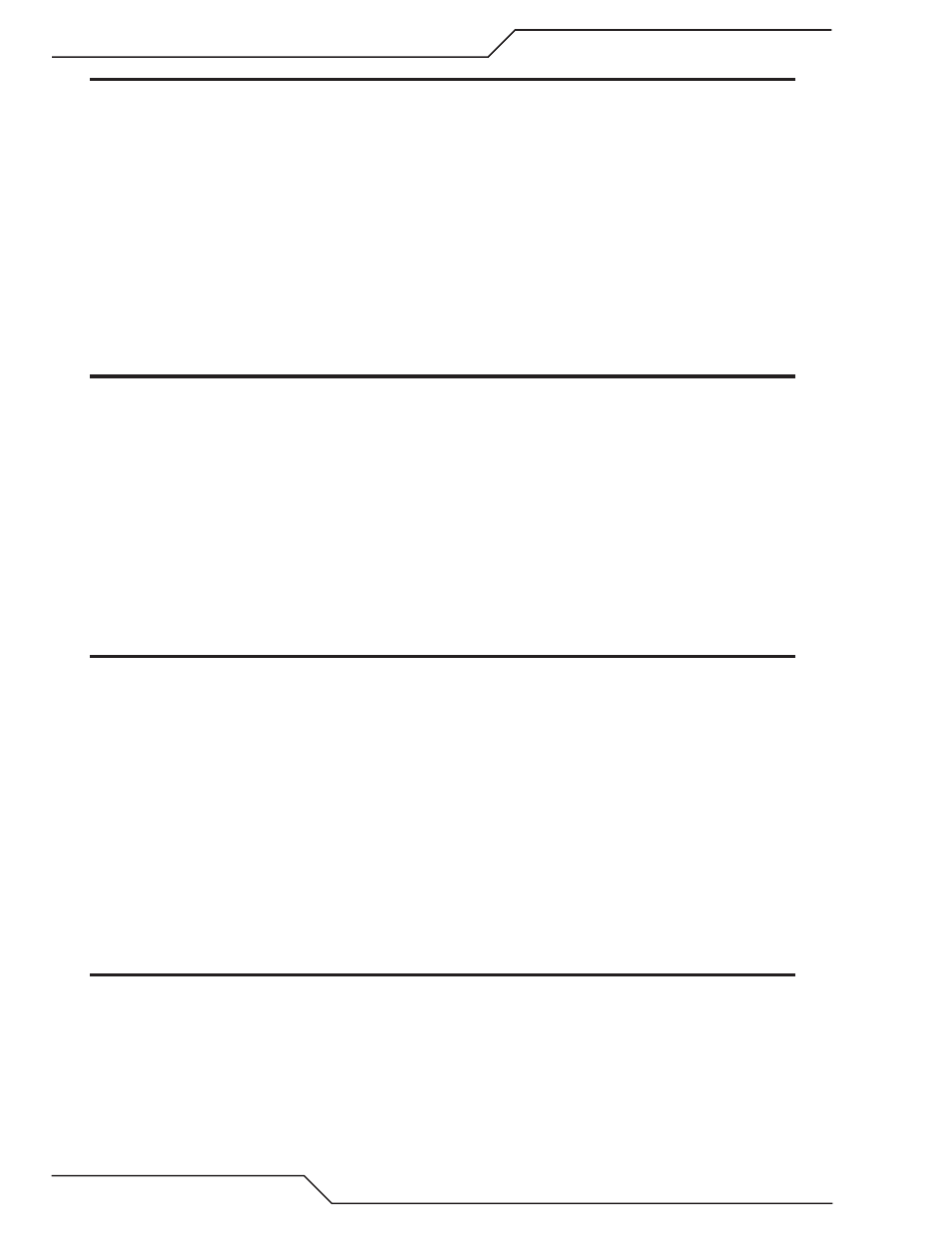
ULTRA-CUT 100 XT
��
INSTALLATION
Manual 0�5272
NOTE
Do Not connect the work cable directly to the ground rod. Do not coil up excess ground or power cables. Cut to
proper length and reterminate as needed.
5. Make sure work cable and ground cables are properly connected. The work cable must have a solid connection
to the cutting table. The work and ground connections must be free from rust, dirt, grease, oil and paint. If
necessary grind or sand down to bare metal. Use lock washers to keep the connections tight. Using electrical
joint compound to prevent corrosion is also recommended.
6. The plasma power supply chassis is connected to the power distribution system ground as required by electrical
codes. If the plasma supply is close to the cutting table (see NOTE) a second ground rod is not usually needed,
in fact it could be detrimental as it can set up ground loop currents that cause interference.
When the plasma power supply is far away from the ground rod and interference is experienced, it may help
to install a second earth ground rod next to the plasma power supply. The plasma power supply chassis would
then be connected to this ground rod.
NOTE
It is recommended that the Plasma Power Supply be within 20 - 30 ft (6.1 – 9.1 m) of the cutting table, if possible.
7. The plasma control cable should be shielded with the shield connected only at the cutting machine end. Con�
necting the shield at both ends will allow ground loop currents which may cause more interference than with
no shield at all.
Creating An Earth Ground
1. To create a solid, low resistance, earth ground, drive a 1/2 in (12 mm) or greater diameter copper clad ground
rod at least 6 � � ft (1.� � 2.4 m) into the earth so that the rod contacts moist soil over most of its length. Depend�
ing on location, a greater depth may be required to obtain a low resistance ground (see NOTE). Ground rods,
typically 10 ft (.0 m) long, may be welded end to end for greater lengths. Locate the rod as close as possible
to the work table. Install a ground wire, 1/0 AWG (European 50 mm2) or greater, between the ground rod and
the star ground point on the cutting table.
NOTE
Ideally, a properly installed ground rod will have a resistance of three ohms or less.
D. Low Cost Ground Rod Tester
1. A key component of reduced EMI is a good low resistance earth ground rod. There are several very expensive
instruments to measure the ground but cost from several hundred to a few thousand dollars. Below is a low
cost alternative which can be constructed by qualified personnel familiar with established electrical construction
and safety practices. Previously suggested method using an incandescent light bulb will not work with GFCI
outlets which are increasingly being used and the bulbs are becoming obsolete.
2. This method, as well as the light bulb method and some of the expensive instruments, assumes the utility ground
is perfect, Zero ohms. It connects the rod being tested in series with the utility ground and measures the resis�
tance of both in series. If the utility ground is not zero ohms, no matter how good your rod is, you won’t get a
low reading due the higher resistance of the utility ground. Fortunately this is rare. Also if your rod is right next
to another earth grounded structure you may get a false lower reading of only resistance between that structure
and your rod rather than to gnd.
NOTE
In the United States most standard AC outlets are 120 VAC 60 Hz. Elsewhere most outlets are 220 VAC 50Hz.
. Obtain a transformer rated for at least 25 VA with primary voltage and frequency matching your standard outlets.
The transformer should have an isolated secondary of either 220 VAC (220 �240 is OK) or 120 VAC (110�120 is
OK) and be rated for at least 100 ma. The transformer could also have dual 115VAC primaries wired in series
for 220V or in parallel for 120 VAC. An example is Triad N�6�X, shown below, rated 50VA, 50/60 Hz.