Start-up, Start-up -2 – Rockwell Automation 20D DC SCR Precharge Module User Manual
Page 24
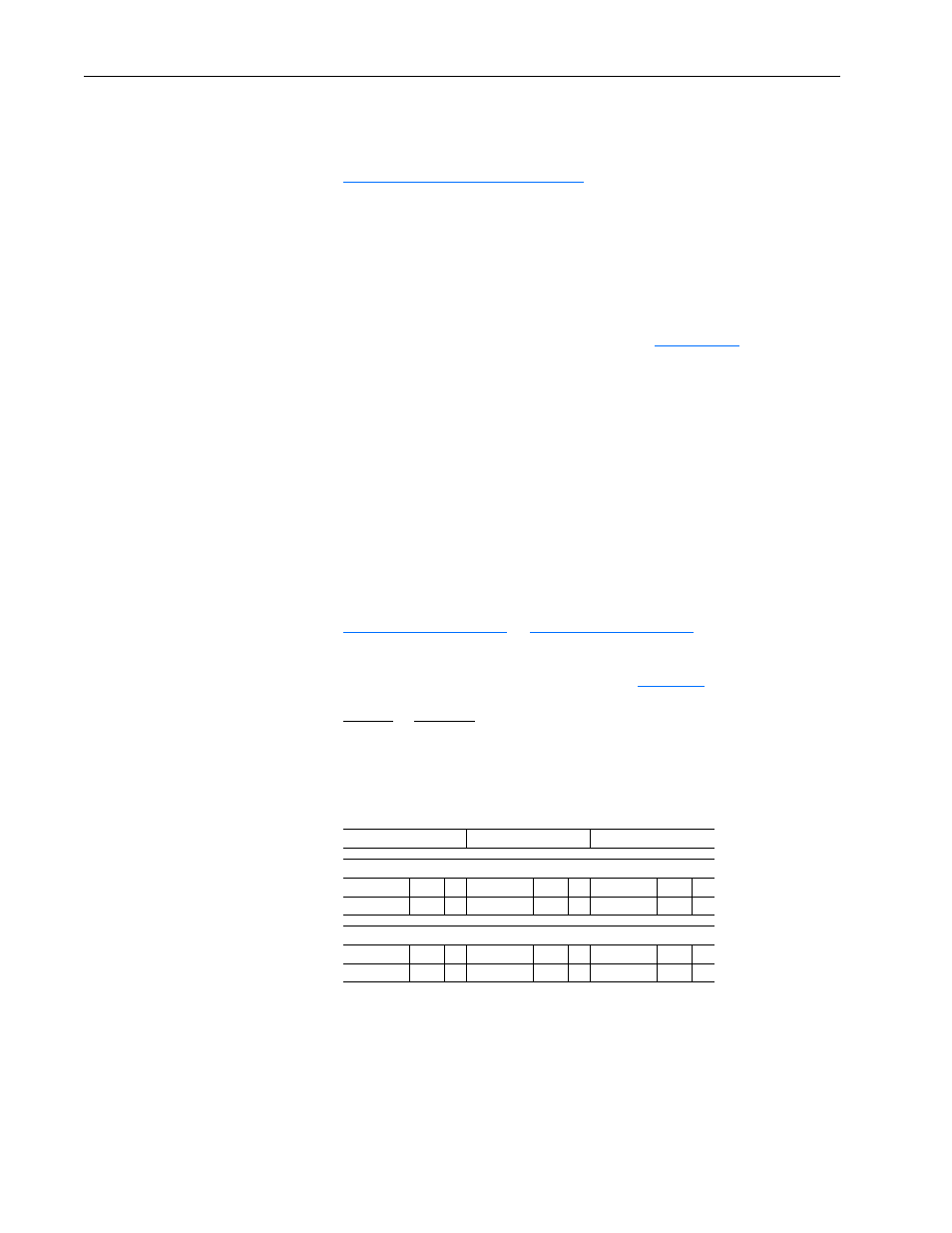
2-2
Start-Up / Troubleshooting
Start-Up
Before Applying Power to the DC SCR Precharge Module
❏ 1. Verify that a minimum of one drive is connected to the DC bus. See
Minimum Capacitance on page 1-4
for details.
❏ 2. Verify that all inputs are connected to the correct terminals and are
properly torqued.
❏ 3. Using an ohmmeter or other continuity testing device, verify that shorts
do not exist between the “+DCin,” “+DCout,” and “-DC” terminals.
❏ 4. Verify that AC line power at the disconnect device is within the rated
value of the DC SCR Precharge Module. See
for product
electrical specification.
❏ 5. Verify that control power voltage is correct.
❏ 6. Verify that the enable precharge relay coil “CR” is correctly wired.
❏ 7. Verify that these two outputs are correctly wired:
– DC SCR Precharge Overtemperature (TB2-9 and TB2-10)
– Precharge Enable (TB2-6 and TB2-7)
These NC (normally closed) and NO (normally open) contacts are used
to set alarms and to stop the drive(s). Verify that they have been wired
correctly according to the user’s specification. Refer to
❏ 8. Verify that the “W1”, “W2,” and “W3” jumpers on the Precharge Control
Board A2 are set to the positions shown in
Table 2.A
.
Jumper
Function
W1
System control voltage selection
W2
Interlock enable/bypass
W3
Handshake normal/bypass
Table 2.A A2 Precharge Board Jumper Settings
❏ 9. Verify that the jumpers between control terminals TB2A-1 and TB2A-3,
and TB2A-2 and TB2A-4 are present.
Important: When supplying 24 VDC control power, these jumpers must
be removed from the terminals on TB2A, and 120 VAC
power must be wired to terminals TB2A-3 and TB2A-4.
(W1) JMP1
(W2) JMP2
(W3) JMP3
For PowerFlex 700H/700S Drive Applications
24 VDC
1-2
INTLK
1-2
X
NORMAL
1-2
X
120 VAC
2-3
X
BYPASS
2-3
BYPASS
2-3
For 1336 PLUS II Drive Applications
24 VDC
1-2
INTLK
1-2
NORMAL
1-2
120 VAC
2-3
X
BYPASS
2-3
X
BYPASS
2-3
X