3 offline tuning / startup, 4 online tuning / startup – Rockwell Automation 9329 Drive Application Software Inertia Comp Imperial Units User Manual
Page 22
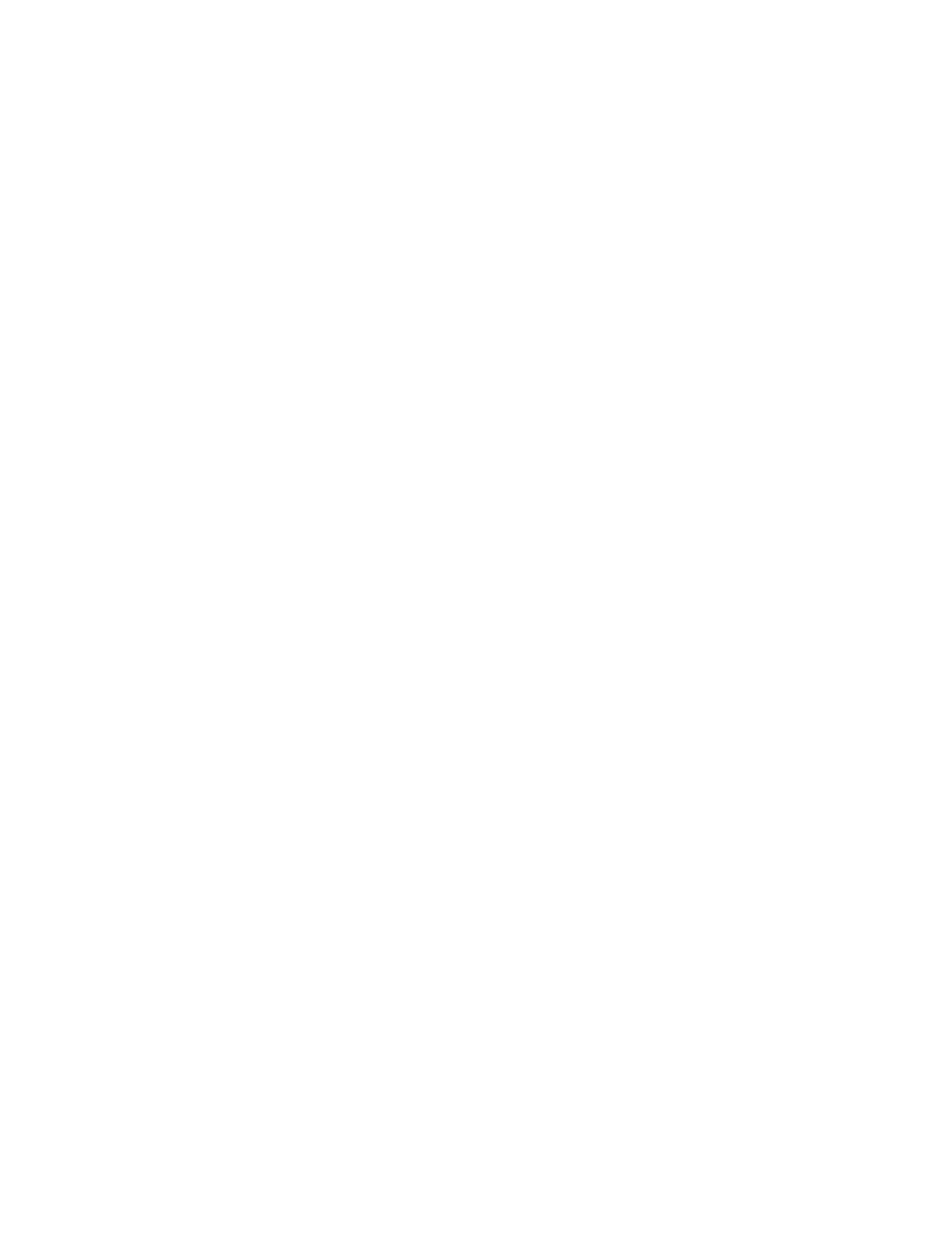
FM – Inertia Compensation
Drive Application Software – page 22 of 28
6.3 Offline Tuning / Startup
Verify that the number and order of JSR input parameters and JSR return parameters agree
with the JSR rung comment and section 4 of this user manual.
Verify that the data type of all JSR instruction input and return parameters agree with the data
type described in the JSR instruction rung comment and section 4 of this user manual. If
immediate values are used for input parameters, the immediate value data type can be
controlled by using or excluding a decimal point. For example, if the JSR instruction input
parameter is designated as type REAL, and the desired value is zero, use “0.0” in the JSR
instruction input parameter. An Input entered a “0” is used as an INTEGER value.
Check the value of all JSR instruction input parameter tags. If the tag is calculated by other
Logix instructions, verify that the tag will be calculated in the correct engineering units. If the
tag is not calculated by other Logix instructions, preset the tag per section 4 of this user
manual.
6.4 Online Tuning / Startup
The following JSR inputs can be adjusted online:
1. JCalc In1
- Empty Core Reflected Inertia [Pound-Feet**2]
2. JCalc In2
- Material Density [Pounds/Feet**3]
3. JLossComp In4
- Number of Differentiator Moving Average Samples
4. JLossComp In8
- Total Reflected Inertia [sec]
5. JLossComp In9
- Inertia Compensation Gain Quadrant 1 and 2
6. JLossComp In10 - Inertia Compensation Gain Quadrant 3 and 4
7. JLossComp In11 - Friction Loss [Percent Load]
8. JLossComp In12 - Windage Loss [Percent Load/RPM]
All other JSR inputs will only require offline tuning.
The following steps can be followed when tuning these parameters:
1. Configure drive to run as a speed regulator with the Drive Torque Reference Inertia and
Losses Torque Part (JLossComp – Ret4) used as a feed forward signal. See the
Tension Regulator Reference Manual for selecting operation as speed mode. Do not
change drive configuration parameters to activate speed control.
2. Set Friction Loss (JLossComp - In11) and Windage Loss (JLossComp - In12) to zero.
3. Set Inertia Compensation Gain Quadrant 1 and 2 (JLossComp - In9) and Inertia
Compensation Gain Quadrant 3 and 4 (JLossComp – In10) to 1.0.
4. If Enable Differentiator (JLossComp – In3) is true, set the Number of Differentiator
Moving Average Samples (JLossComp – In4) to 2.
5. If a center winder application, set up the winder with an empty core or mandrel and
preset the diameter calculator to minimum empty core diameter so that the Normalized
Diameter is 1.0.
6. Setup a trend with the Line Speed Reference (JLossComp - In11) and speed regulator PI
output signal.
7. If a center winder application, accelerate/decelerate the drive and adjust the Empty Core
Reflected Inertia (JCalc - In1) until deviations in the speed PI output are minimized. If a
constant diameter application, accelerate/decelerate the drive and adjust Total Reflected
Inertia (JLossComp - In1) until deviations in the speed PI output are minimized.
8. If Enable Differentiator (JLossComp – In3) is true, add the Torque Reference Inertia Part
to the trend, run the drive at a steady speed, and adjust the the Number of Differentiator
Moving Average Samples (JLossComp – In4) to minimize signal noise.
9. If a constant diameter application, skip to step 13.
10. Place the largest diameter roll available on the winder and set Material Width (JCalc -
In5) to the actual roll width.
11. Accelerate/decelerate the drive and adjust the Material Density (JCalc - In2) until
deviations in the speed PI output are minimized.
12. Remove the roll.