Aerovent ES-2-06 User Manual
Page 8
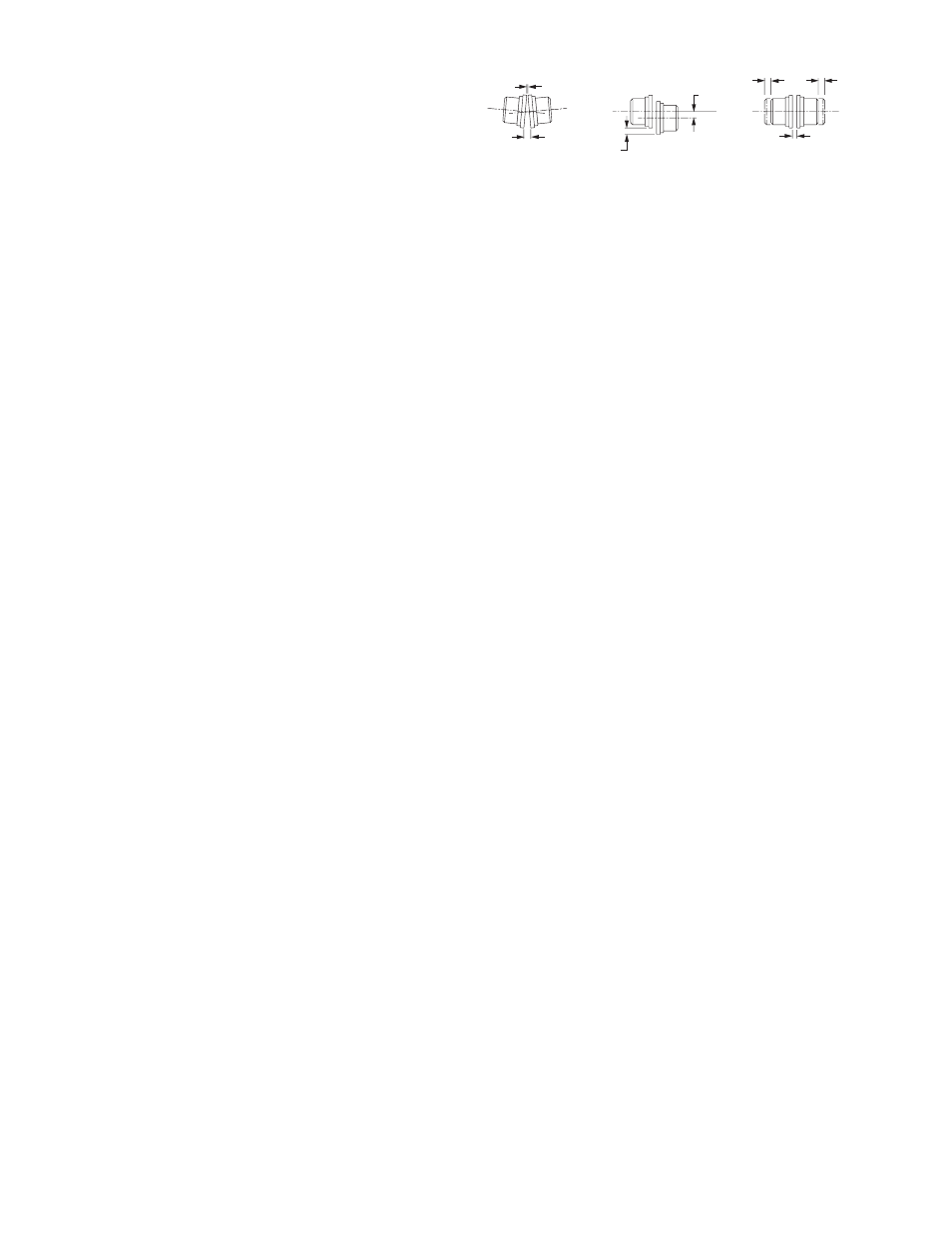
8
Twin City Fan Companies Engineering Supplement 2-06
Grouting
Grouting is the final installation step. Check all shims
before grouting to make sure that the fan is resting
evenly on all points with anchor bolts secured to hold
the shim. Use forms with sufficient space allowed for
working the grout. The concrete foundation should be
clean and well moistened before pouring grout. Use a
commercial grade non-shrinking grout and be especially
sure when pouring grout that the anchor bolt sleeves are
filled. Refer to Figure 2 for a detail of a proper founda-
tion, grout allowance and anchor bolt sleeves.
Drive Mounting
Mount drives as follows:
1. Slip (do not pound) proper sheave onto correspond-
ing shaft.
CAUTION: Placing fan sheave on motor can
overspeed wheel and cause structural failure.
2. Align sheaves with straightedge extended along
sheaves (see Fig. 5), just making contact in two
places on outside perimeters of both sheaves. This
“four-point” alignment may also be checked with a
string tied to the shaft behind one of the sheaves.
The string is then pulled taut over the faces of the
sheaves to check the alignment at the four points
at the outside perimeters. Each sheave should be
rotated about one-half revolution during this check
to look for excessive runout or a bent shaft. Parallel
alignment should be within 5mm per meter of center
distance. Angular Misalignment should be less than 1
degree.
3. Install and tighten the belts. Proper belt tension is
specified on the included documentation. Belts are
tensioned as follows:
Post type, saddle base, slide rails, and slide base
types use one or more bolts held by retaining nuts to
adjust the motor position. Loosen the retaining nuts
and adjust the bolts to push or pull the motor until
the belts reach their specified tension. Tighten the
retaining nuts per torque specifications in Table 1.
4. Run the drive for a few minutes to seat the belts.
When tightening the belts, slide the motor in to slip
the belts on. Do not use a pry bar, as this may dam-
age the belt cords. Retighten the belts to the proper
tension if necessary. Recheck sheave alignment.
5. After initial installation of belts, recheck belt tension
and alignment as indicated in Table 7.
Flexible Couplings
These instructions are general for the installation of
several types of flexible couplings and should not be
used as a substitute for more specific manufacturer’s
instructions. The coupling manufacturer’s installation data
is included with the supplied datasheet (when applicable)
and will give specific dimensions for alignment limits,
lubricants, etc.
Before preparing to mount the coupling, make sure
that all bearings, inlet vanes, shaft seals, or other com-
ponents have been installed on the shaft.
When mounting and keying the coupling halves to
the shaft, follow supplied instructions for heating and
shrink fitting. Set the coupling halves for the normal gap
specified by the manufacturer. Coupling gap is illustrated
in Figure 6.
The two types of misalignment are illustrated above.
Typically angular alignment is checked with feeler gaug-
es between the hub faces. When angular alignment has
been adjusted to manufacturer’s specification by shim-
ming, if necessary, parallel alignment can be checked
with a straightedge and feeler gauges on the hub halves’
O.D. When shimming has brought parallel alignment
within specification, angular alignment and gap should
again be checked, and adjustments made if necessary.
A dial indicator may be used to more accurately take
the measurements described above.
Special adjustments may need to be made for cou-
plings used with some equipment. As an example, when
used with motors of over 300 HP, couplings may require
provisions for limiting end float. Larger drivers may grow
in operation (due to heat expansion) requiring the driver
side to be set slightly low when not operating. Specific
instruction manuals or assembly drawings will indicate
these requirements when applicable.
Thoroughly clean the coupling halves after completion
of alignment. Reassemble the coupling and tighten bolts,
washers and locknuts. Lubricate per manufacturer’s rec-
ommendations.
Duct Connections
The fan support structure is normally not designed to
carry loads imposed by the weight of ducts, silencers,
stacks, etc. Supporting these loads on the fan can
cause housing distortion and may cause performance
problems due to the relation of fan housing to wheel.
Use of flexible connections is recommended.
Where hazardous materials will be conveyed in the
fan, all connections made by the user shall be com-
pletely sealed with material suitable for the gas or vapor
to be handled.
Guards and Enclosures
When advised of the need for guards fully complying
with the machinery directive, Twin City Fan Companies,
Ltd. will supply the guarding identified as being required.
In most cases, Twin City Fan Companies, Ltd. is not
aware of the end use and installation of the fan, which
typically eliminates the need for more restrictive guard-
ing to be compliant with EN 294 and EN 811. For this
reason, the user is must verify that the final installation
is compliant with EN 953, EN 294, and EN 811. This is
especially true of plug and plenum fans. Specific items
that should be considered include but are not limited
to the following:
• Outlet ducting / enclosure. The ducting or enclosure
must be compliant to the requirements of EN 953
and EN 294 and EN 811. This is not assured by
Twin City Fan Companies, Ltd. unless specifically
notified by the end user at the time of the order.
• Inlet guards. Inlet guarding relies on the additional
safety distance provided by inlet ducting or other
enclosure increasing the safety distance to 850 mm
or greater. This is because the installation usually
eliminates the need for excessive guarding on the
inlet of the fan. In addition, excessive guarding on
the inlet of the fan would significantly deteriorate
performance and is therefore not desirable.
Y
X
P
P
F
F
GAP
ANGULAR
PARALLEL
GAP AND
MISALIGNMENT
MISALIGNMENT
END FLOAT
X-Y = ANGULAR MISALIGNMENT
P = PARALLEL OFFSET (MISALIGNMENT)
F = END FLOAT
Figure 6. Coupling Alignment