Lm & lmr power end disassembly & assembly, Warning – Goulds Pumps AF (Axial Flow) (42"/1200mm/54/60"/66") LM/LMR Bearings - IOM" User Manual
Page 46
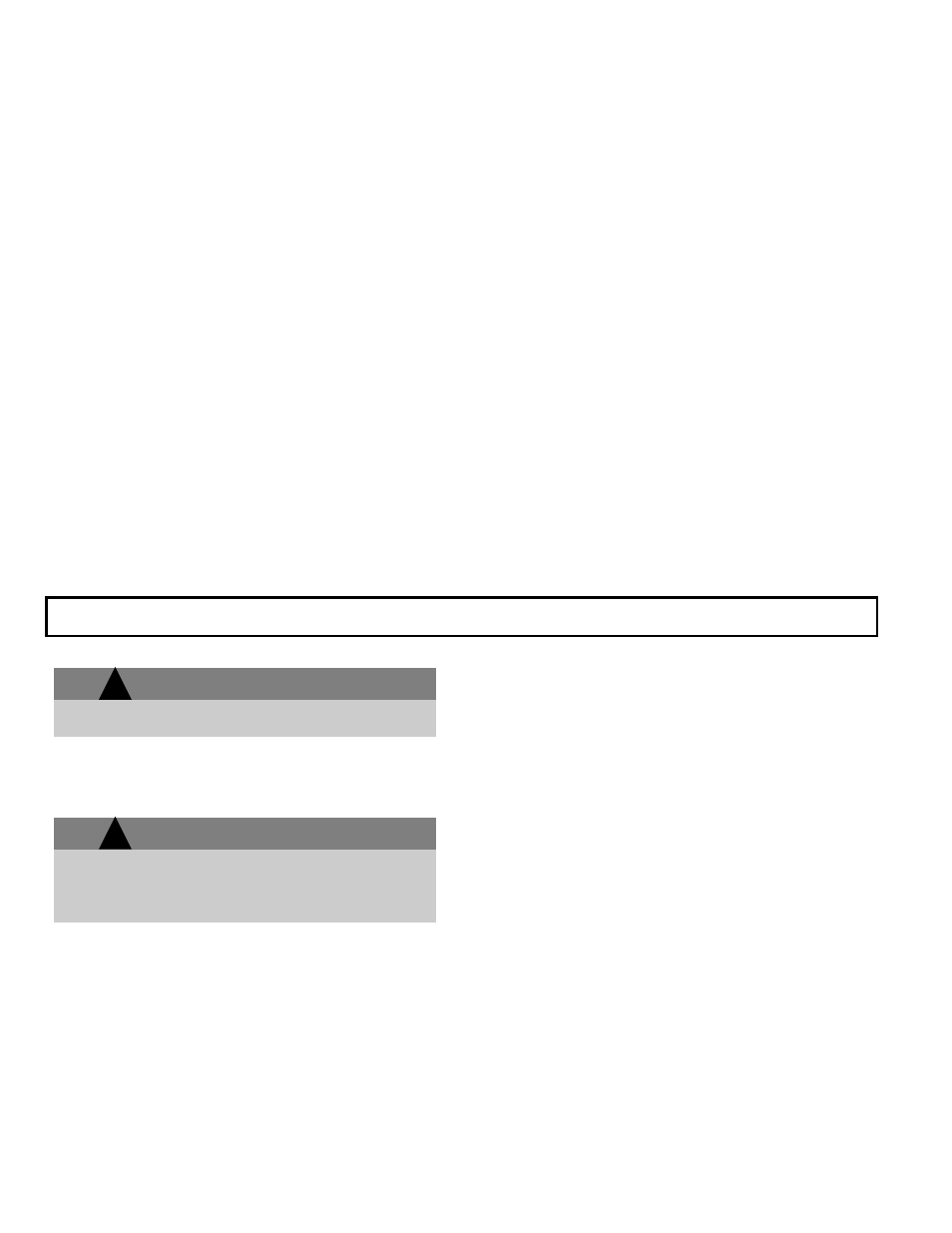
46 AF (42-66) IOM
PUMP RE-ASSEMBLY
1. Be sure shaft (122) and sleeve (126) are clean and
free of all burrs. Slide shaft sleeve (126) over shaft
(122), making sure that O-rings are in place as
indicated on assembly drawing. Secure sleeve with
set screw (222C) and key (128D).
2. Provide adequate support for bearing housing
(134) and shaft (122). Carefully slide shaft through
stuffing box of suction elbow. Bolt bearing housing to
suction elbow (315A).
3. Install shaft O-rings (496C & 496D) on shaft (122).
Place the shaft key (178) in the keyway. Lubricate the
O-rings as required.
4. Carefully install impeller (101) on shaft (122). With
shaft washer (9985) in place, install (4) cap screws
(370C) to secure the impeller to the shaft. Install
impeller end cap (9988) with o-ring (496B) as required.
5. Bolt casing (100) to elbow (315A) with (6) bolts
evenly spaced around bolt circle. Leave bolts loose
enough to shift casing for alignment with impeller. The
actual adjustment of casing is accomplished by turning
the (3) adjusting screws (370B) against casing flange.
6. The procedure for setting impeller clearance is
described in the ALIGNMENT section of these
instructions. When acceptable alignment has been
achieved, secure the initial (6) bolts, then install the
remaining bolts and tighten.
7. Before connecting the coupling halves, check
direction of motor rotation. Manually turn pump shaft
to insure no rubbing. Be sure the pump and gear box
shafts are in alignment according to the previously
discussed alignment procedure.
8. Connect coupling halves and any intermediate
shafting.
9. Assemble discharge piping to casing.
10. If packing is used, assemble gland, packing,
lantern rings and sleeve into stuffing box. Do not
compress too tightly until after start-up. The packing
will need to be "run-in" and adjusted for proper flow of
lubricating water. If a mechanical seal is used, please
see the mechanical seal IOM for proper installation of
seal.
11. Connect seal water and cooling lines to pump. Fill
the oil lubrication system. Be sure bearing housing oil
is level with the center of the sight glass.
LM & LMR POWER END DISASSEMBLY & ASSEMBLY
Power End Disassembly (See Fig.’s 20, 21)
WARNING
Lockout driver power to prevent accidental
startup.
1. Lockout power supply to motor.
2. Close suction and discharge valve.
WARNING
The pump may handle hazardous and/or toxic
fluids. Skin and eye protection may be required.
Precautions must be taken to prevent injury or
environmental damage.
1. Remove piping from pump.
2. Remove coupling guard and coupling (direct
connect) or belt guard and belts (belt drive).
3. Drain oil from bearing housing, disconnect oil
circulation system, and remove pump from sub-base.
4. Wash down pump with appropriate cleaner.
5. Disassemble Pump per instructions per that
section. Discharge piping and impeller (101) will be
disassembled. The power end with the shaft (122) will
be removed from the elbow (315A).
6. Remove cap screws (370H) fastening thrust
bearing retainer (109) to bearing housing (134).
Carefully pull retainer over shaft. Top suction pumps
have thrust bearing (112C) at the outboard location
and the thrust bearing stationary race and (6) small
springs (9890) may be jarred free. Do not damage oil
seal (332).
7. Be sure overhung portion of shaft is supported.
8. Remove cap screws (370F) fastening radial
bearing retainer (119B) to bearing housing (134).
Carefully pull retainer away from bearing housing
without damaging lip seal (333).
!
!