Pump troubleshooting, Connection of sealing liquid, Table 3 – Goulds Pumps AF (Axial Flow) (42"/1200mm/54/60"/66") LM/LMR Bearings - IOM" User Manual
Page 43
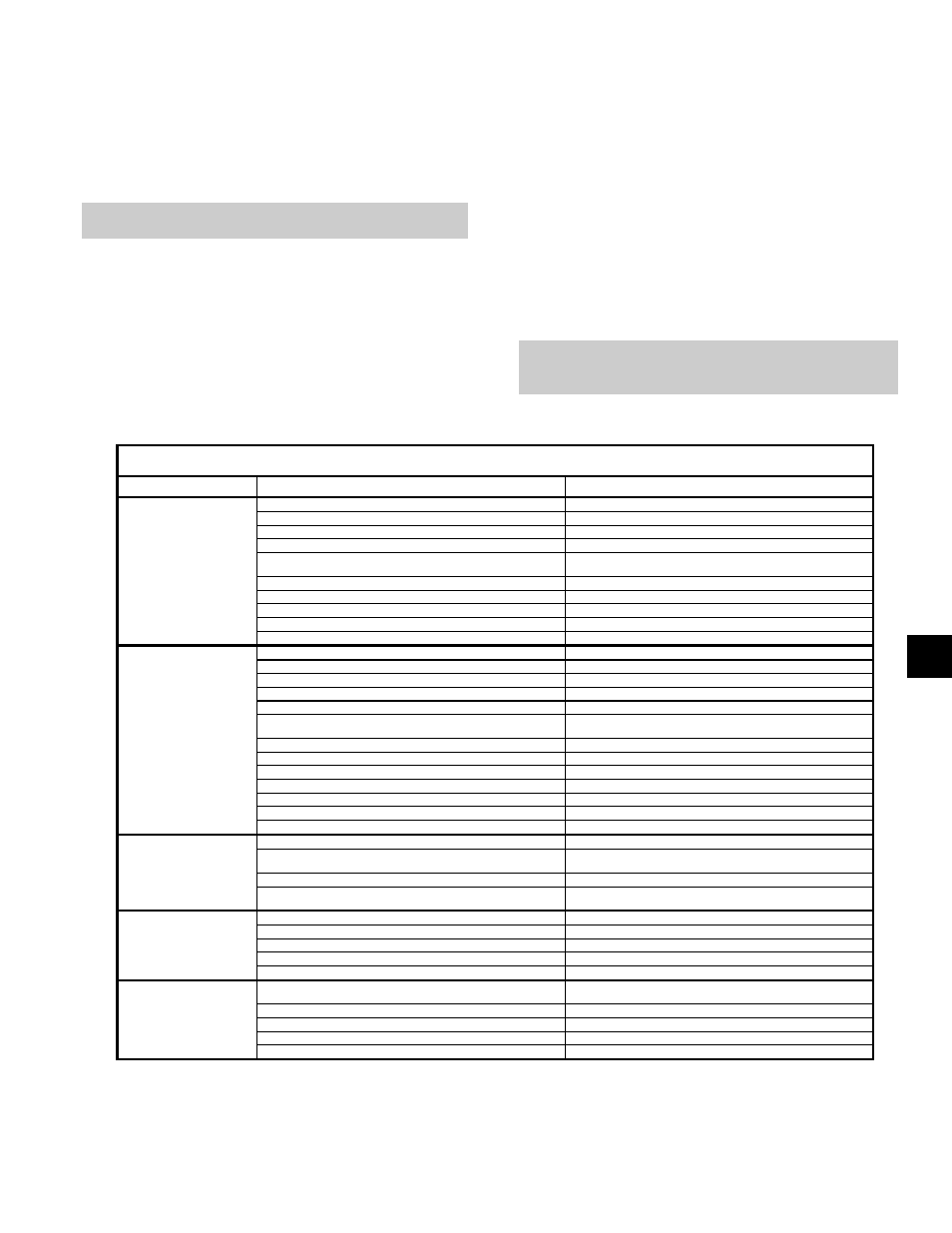
AF (42-66) IOM 43
CONNECTION OF SEALING LIQUID
If stuffing box pressure is above atmospheric pressure
and the pumpage is clean, normal gland leakage of 40-
60 drops per minute is usually sufficient to lubricate and
cool packing and sealing liquid is not required.
NOTE: Otherwise an external flush should be used
to lubricate and cool packing.
An external sealing liquid is required when:
1. Abrasive particles in the pumpage could score
the shaft sleeve.
2. Stuffing box pressure is below atmospheric
pressure due to pump running when suction
source is under vacuum. Under these
conditions, packing will not be cooled and
lubricated and air will be drawn into the pump.
If an outside source of clean compatible liquid
is required,
The pressure should be 15-20 psi
(1.1-1.4 kg/cm
2
) above suction
pressure. The piping should be
connected to the stuffing box flush
port inlet.
3. Under extreme temperature and pressure a
pipe should also be connected to the flush
port outlet.
NOTE: Most packing requires lubrication. Failure
to lubricate packing may shorten the life of the
packing and pump.
Pump Troubleshooting
PROBLEM
PROBABLE CAUSE
REMEDY
Pump not primed or prime lost, liquid level does not completely fill elbow Fill system piping completely so the impeller is submerged
Suction inlet clogged
Remove obstructions from pump inlet
Impeller clogged with foreign material
Back flush pump or manually clean impeller
Suction and /or discharge valve closed or clogged
Open valves to remove shut-off condition
No liquid delivered or
intermittent flow
Wrong direction of rotation
Change rotation to concur with direction indicated by the arrow on the
bearing housing
Suction piping incorrect
Replace or modify suction piping
Insufficient NPSH available
Increase liquid level or lower pump
Air leak in suction line
Test suction piping for leaks
Speed (rpm) too low
New drive or gear box to obtain higher pump speed
Excess air entrapped in liquid
Install vent in piping or eliminate air source
Impeller partly clogged
Back flush pump or manually clean impeller
Insufficient suction head
Fill system piping so the liquid level is above the pump impeller centerline
Pump not primed or prime lost, pump does not completely fill elbow
Fill system piping completely so the impeller is submerged
Suction and/or discharge valve closed or clogged
Open valves to remove partially blocked condition
Suction piping incorrect
Replace or modify suction piping
Pump not producing rated flow
or head
Excessive air entrapped in liquid
Install vent in piping or eliminate air source
Speed (rpm) too low
New drive or gear box to obtain higher pump speed
Incorrect rotation
Check motor wiring
Incorrect impeller or impeller diameter
Check vane angles and/ or impeller clearances
System head too high
Check system curve calculations, reduce system resistance
Instruments give erroneous readings
Check and calibrate instruments, replace if necessary
Worn or broken impeller, bent vanes
Inspect and replace if necessary
Pump assembled incorrectly
Compare pump assembly to instruction manual
Insufficient NPSH available
Increase liquid level or lower pump
Wear of internal wetted parts
is accelerated
Chemicals in liquid other than specified
Analyze pumpage and correct or change pump wet end materials to suit
pumpage composition
Pump assembled incorrectly
Compare pump assembly to instruction manual
Higher solids concentration than specified
Analyze pumpage and correct or change pump wet end materials to
harder composition
Packing gland improperly adjusted
Tighten gland nuts
Excessive leakage
Stuffing box improperly packed
Check packing and re-pack box
from stuffing box
Worn mechanical seal parts
Replace worn parts
Overheating mechanical seal
Check lubrication and cooling lines
Shaft sleeve scored
Re-machine or replace as required
Pump run off design point
Check head and flow, AF’s should normally be run between 75% and
125% of BEP
Packing has short life
Shaft/shaft sleeve worn
Replace shaft or shaft sleeve if necessary
Packing gland not properly adjusted
Replace packing and readjust gland as specified in the operating manual
Packing not properly installed
Check packing manufacturer's instructions.
Pump not assembled correctly
Compare pump assembly to instruction manual
Table 3
5