Impeller alignment – Goulds Pumps AF (Axial Flow) (42"/1200mm/54/60"/66") LM/LMR Bearings - IOM" User Manual
Page 27
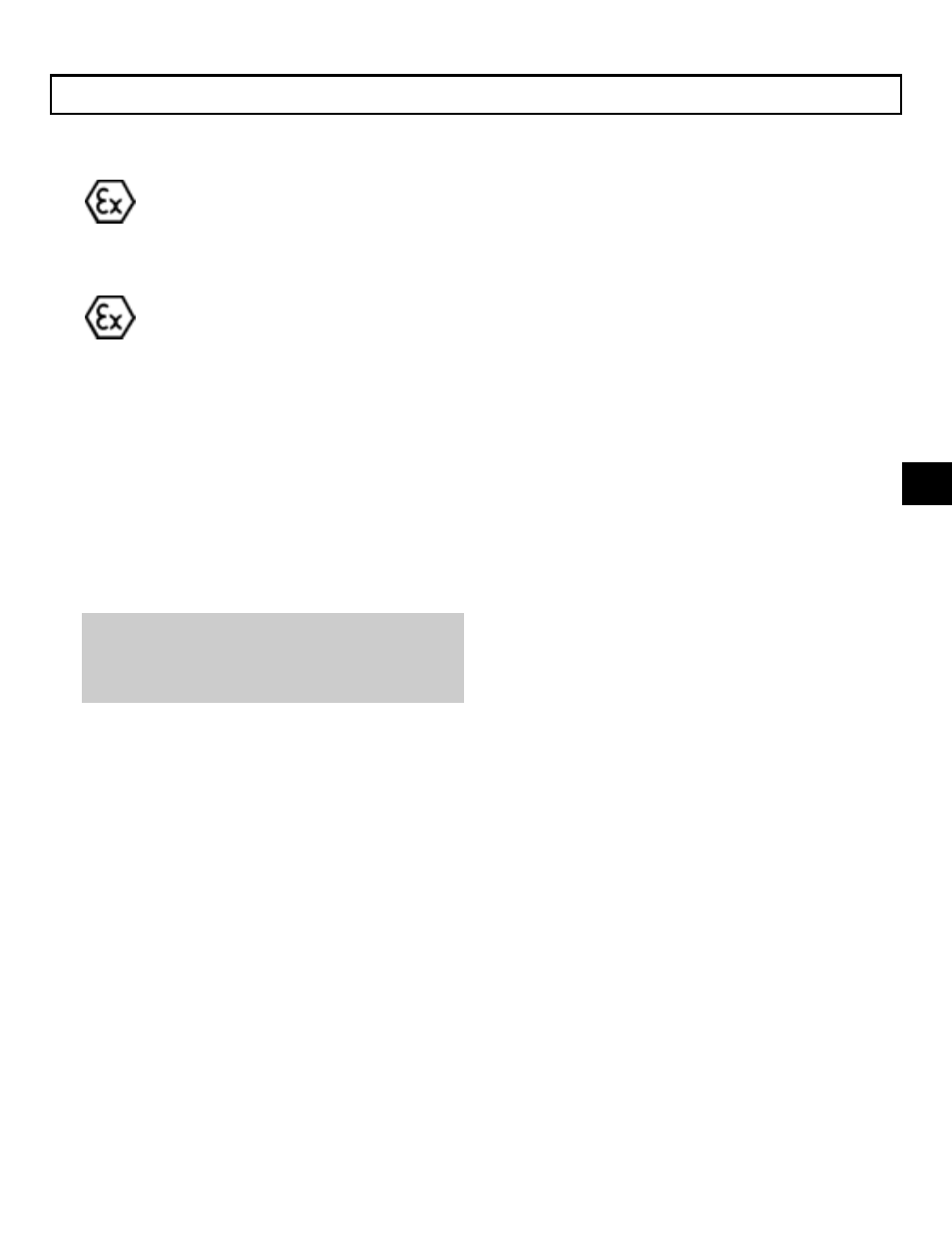
AF (42-66) IOM
27
IMPELLER ALIGNMENT
GENERAL
Improper impeller adjustment could cause
contact between the rotating and stationary
parts, resulting in a spark and heat
generation.
The impeller clearance setting procedure
must be followed. Improperly setting the
clearance or not following any of the proper
procedures can result in sparks, unexpected
heat generation and equipment damage.
The AF impeller has been aligned at the factory but
should be checked prior to pump operation. The
impeller requires several thousandths of and inch of
clearance to prevent rubbing due to the action of
hydraulic forces when the pump is operating. Many
corrosion-resistant alloys will gall and build up if
rubbing occurs, therefore, pumps using these alloys
need to be free from any rubbing.
Turn the shaft by hand, if the impeller rubs the inside of
the casing it must be realigned. The following steps
are used to align the impeller.
Note: Impeller rubbing is often caused by pipe
strain or belt tension. Pipe strain must be
eliminated prior to impeller alignment. The
impeller should aligned after proper belt
tensioning.
Clearance measurement - The alignment worksheet
on page 27 is used to align the impeller of the AF
pump. The measurement procedure is as follows:
Make sure the cap screws fastening the casing to the
elbow are tight, so an accurate measurement of the
impeller clearances can be made prior to adjustment.
Mark each blade 1, 2, 3 and 4 and then align the
impeller blades as shown on the impeller alignment
worksheet (approx. 2, 4, 8, and 10 o’clock)
Rotate the shaft and measure the gap between each
blade and the casing at all four clock positions
indicated on the worksheet. The value of interest is
the largest value of feeler gage thickness that will slide
easily the whole length of the vane tip.
Add the measurements for all positions together and
divide by the number of measurements. This will give
the average measurement.
Divide the average measurement by 2. This will give
the minimum clearance.
If any blade has a clearance in any position smaller
than the calculated minimum clearance the prop is not
sufficiently centered and should be adjusted.
Impeller Alignment
1. Loosen the bolts that attach the casing to the
elbow.
2. Use the adjusting bolts attached to the elbow to
adjust the impeller clearance. The adjusting bolts
are used to raise and lower the casing and shift the
casing left to right relative to the impeller.
3. Move the casing relative to the impeller until the
impeller is centered. At this point it is
recommended that the Impeller Alignment
Worksheet (on the following page) be filled out and
filed with the pump maintenance records for future
reference.
4. Tighten the bolts between the casing and the
elbow and re-check the clearance to be sure the
adjustments have centered the impeller. If the
impeller is centered the casing may be taper
pinned to the elbow to maintain alignment.
3