Goulds Pumps 3408A - IOM User Manual
Page 32
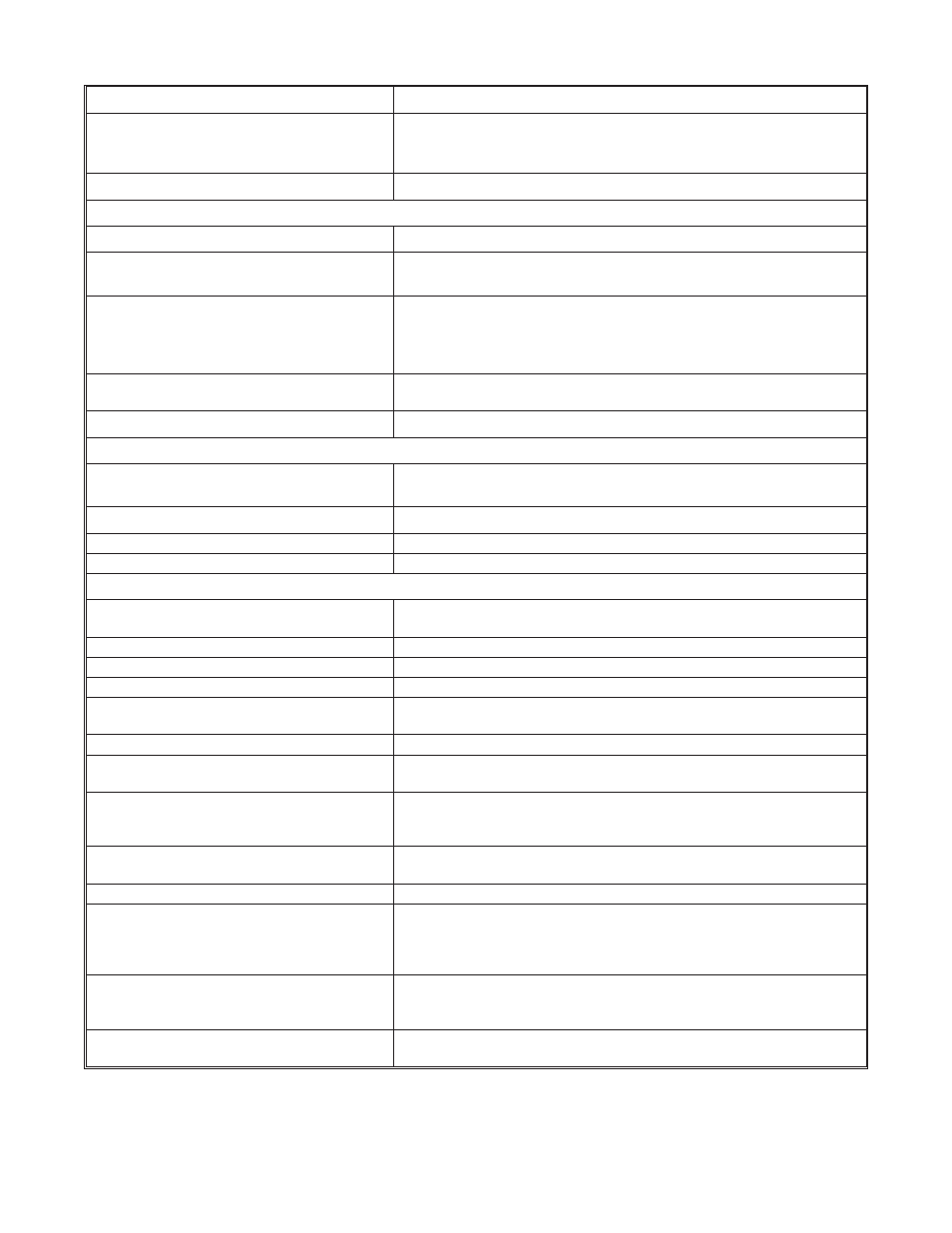
CAUSES
CURES
18. Too small impeller diameter (probable
cause if none of the above)
Check with the factory to see if a larger impeller can be used; otherwise,
cut the pipe losses or increase the speed, or both as needed. Be careful not
to overload the driver.
19. Air leaks in suction piping
See item 8.
Not Enough Pressure
20. Mechanical defects
See items 14 and 15.
21. Obstruction in liquid passages
Dismantle pump and inspect passages of impeller and casing. Remove
obstruction.
22. Air or gases in liquid (Test in laboratory,
reducing pressure on liquid to pressure in
suction line. Watch for bubble formation.)
May be possible to overrate pump to the point where it will provide
adequate pressure despite condition. Better to provide gas separation
chamber on suction line near pump, and periodically exhaust accumulated
gas. See item 13.
23. Too small impeller diameter (Probable
cause if none above)
See item 18.
24. Speed too low
See item 5.
Pump Operates For Short Time, Then Stops
25. Incomplete priming
Free pump, piping and valves of all air. If high points in suction line
prevent this, they need correcting. See the section entitled Suction Piping.
26. Suction lift too high
See item 3.
27. Air leaks in suction piping
See item 8.
28. Air or gases in liquid
See item 22.
Pump Takes Too Much Power
29. Head lower than rating; thereby pumping
too much liquid
Machine impeller’s OD to size advised by factory.
30. Cavitation
See item 13.
31. Mechanical defects.
See items 14 and 15.
32. Suction inlet not immersed enough
See item 16.
33. Liquid heavier (in either viscosity or
specific gravity) than allowed for
Use larger driver. Consult factory for recommended size. Test liquid for
viscosity and specific gravity.
34. Wrong direction of rotation
See item 6.
35. Casing distorted by excessive strains from
suction or discharge piping
Check alignment. Examine pump for friction between impeller and
casing. Replace damaged parts.
36. Shaft bent due to damage – through
shipment, operation, or overhaul
Check deflection of rotor by turning on bearing journals. Total indicator
run-out should not exceed 0.002” on shaft and 0.004” on impeller wearing
surface.
37. Mechanical failure of critical pump parts
Check bearings and impeller for damage. Any irregularity in these parts
will cause a drag on shaft.
38. Misalignment
Realign pump and driver.
39. Speed may be too high (brake hp of pump
varies as the cube of the speed; therefore, any
increase in speed means considerable increase
in power demand.)
Check voltage on motor.
40. Electrical defects
The voltage and frequency of the electrical current may be lower than that
for which the motor was built; or there may be defects in motor. The
motor may not be ventilated properly due to a poor location.
41. Mechanical defects in turbine, engine or
other type of drive exclusive of motor
If trouble cannot be located, consult factory.
24
3408A IOM 6/08