Final alignment, Warning, Optional alignment procedure – Goulds Pumps 3408A - IOM User Manual
Page 23: Caution, Doweling, Suction and discharge piping
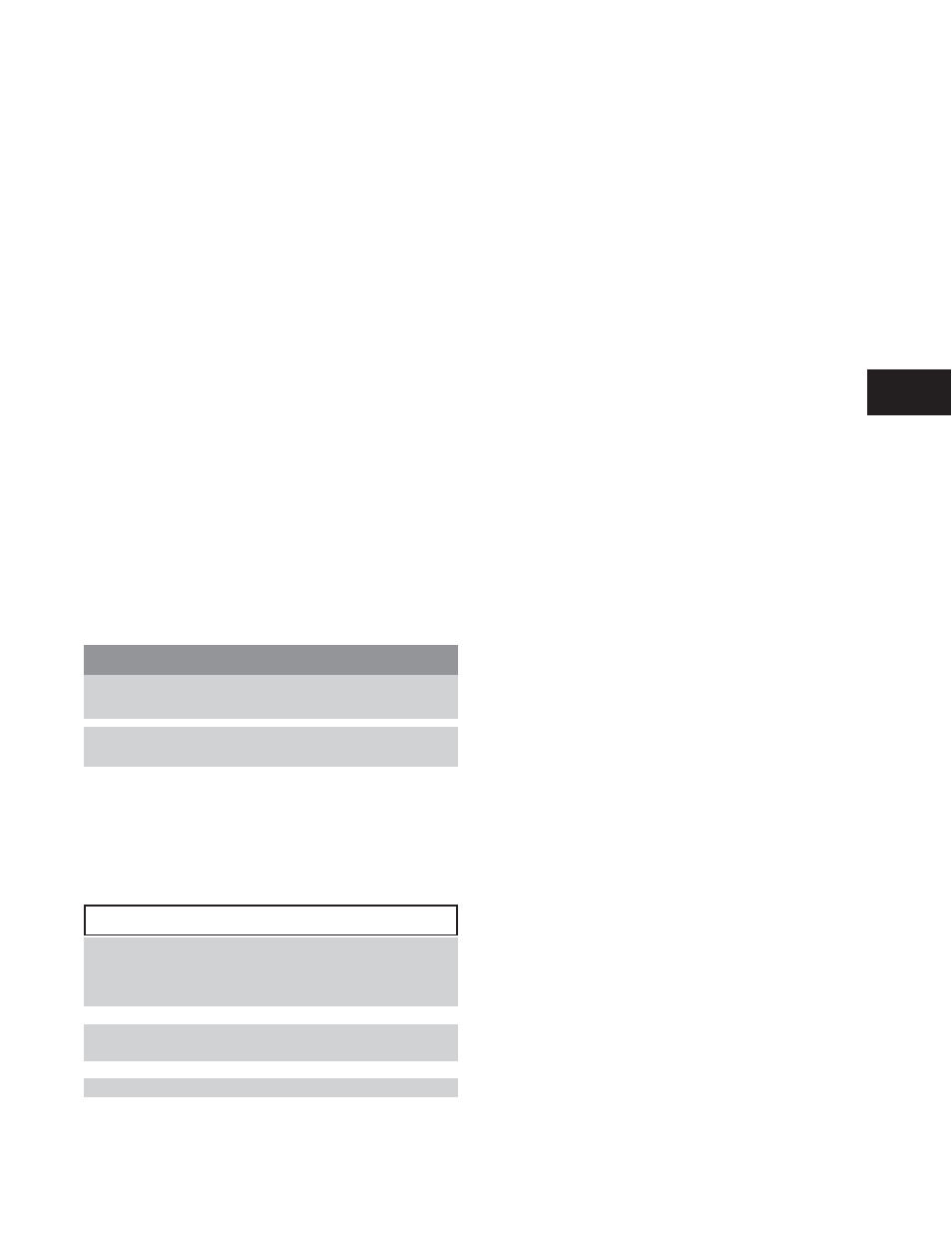
3.
Scribe index lines on coupling halves as shown in
Figure 8.
4.
Mount dial indicator on one hub as shown for parallel
alignment. Set dial to zero.
5.
Turn both coupling halves so that index lines remain
matched. Observe dial reading to see whether driver
needs adjustment. See paragraph i below.
6.
Mount dial indicator on one hub as shown for angular
alignment. Set dial to zero.
7.
Turn both coupling halves so that index lines remain
matched. Observe dial reading to see whether driver
needs adjustment. See paragraph i below.
8.
Assemble coupling. Tighten all bolts and set screw(s).
It may be necessary to repeat steps c through f for a
final check.
9.
For single element couplings, a satisfactory parallel
misalignment is .004" T.I.R., while a satisfactory
angular misalignment is .004" T.I.R. per inch of radius
R. See Figure 8.
Final Alignment
Final alignment cannot be accomplished until the pump has
been operated initially for a sufficient length of time to
attain operating temperature. When normal operating
temperature has been attained, secure the pump to re-check
alignment and compensate for temperature accordingly. See
the section entitled Alignment Procedure.
s
!
WARNING
Rotating Components Hazard
Do not operate pump without all guards in place.
Failure to follow these instructions could result in seri-
ous personal injury or death, or property damage.
OPTIONAL Alignment Procedure
If desired, the pump and motor feet can be doweled to the
base after final alignment is complete. This should not be
done until the unit has been run for a sufficient length of
time and alignment is within the tolerance. See the section
entitled Doweling.
$
!
CAUTION
Extreme Temperature and/or
Flying Debris Hazard
Eye protection and gloves required.
Failure to follow these instructions could result in
property damage and/or moderate personal injury.
NOTE: Pump may have been doweled to base at factory.
DOWELING
Dowel the pump and driving unit as follows:
1.
Drill holes through diagonally opposite feet and into
the base. Holes must be of a diameter 1/64 inch less
than the diameter of the dowel pins. Clean out the
chips.
2.
Ream the holes in feet and base to the proper diameter
for the pins (light push fit). Clean out the chips.
3.
Insert pins to be approximately flush with feet.
SUCTION AND DISCHARGE PIPING
When installing the pump piping, be sure to observe the
following precautions:
Piping should always be run to the pump.
Do not move pump to pipe. This could make final
alignment impossible.
Both the suction and discharge piping should be supported
independently near the pump and properly aligned, so that
no strain is transmitted to the pump when the flange bolts
are tightened. Use pipe hangers or other supports at
necessary intervals to provide support. When expansion
joints are used in the piping system, they must be installed
beyond the piping supports closest to the pump. Tie bolts
should be used with expansion joints to prevent pipe strain.
Do not install expansion joints next to the pump or in any
way that would cause a strain on the pump resulting from
system pressure changes. It is usually advisable to increase
the size of both suction and discharge pipes at the pump
connections to decrease the loss of head from friction.
Install piping as straight as possible, avoiding unnecessary
bends. Where necessary, use 45-degree or long sweep
90-degree fitting to decrease friction losses.
Make sure that all piping joints are air-tight.
Where flanged joints are used, assure that inside diameters
match properly.
Remove burrs and sharp edges when making up joints.
Do not “spring” piping when making any connections.
Provide for pipe expansion when hot fluids are to be pumped.
3408A IOM 6/08
15
3