NOVUS Controlador N960 User Manual
Page 2
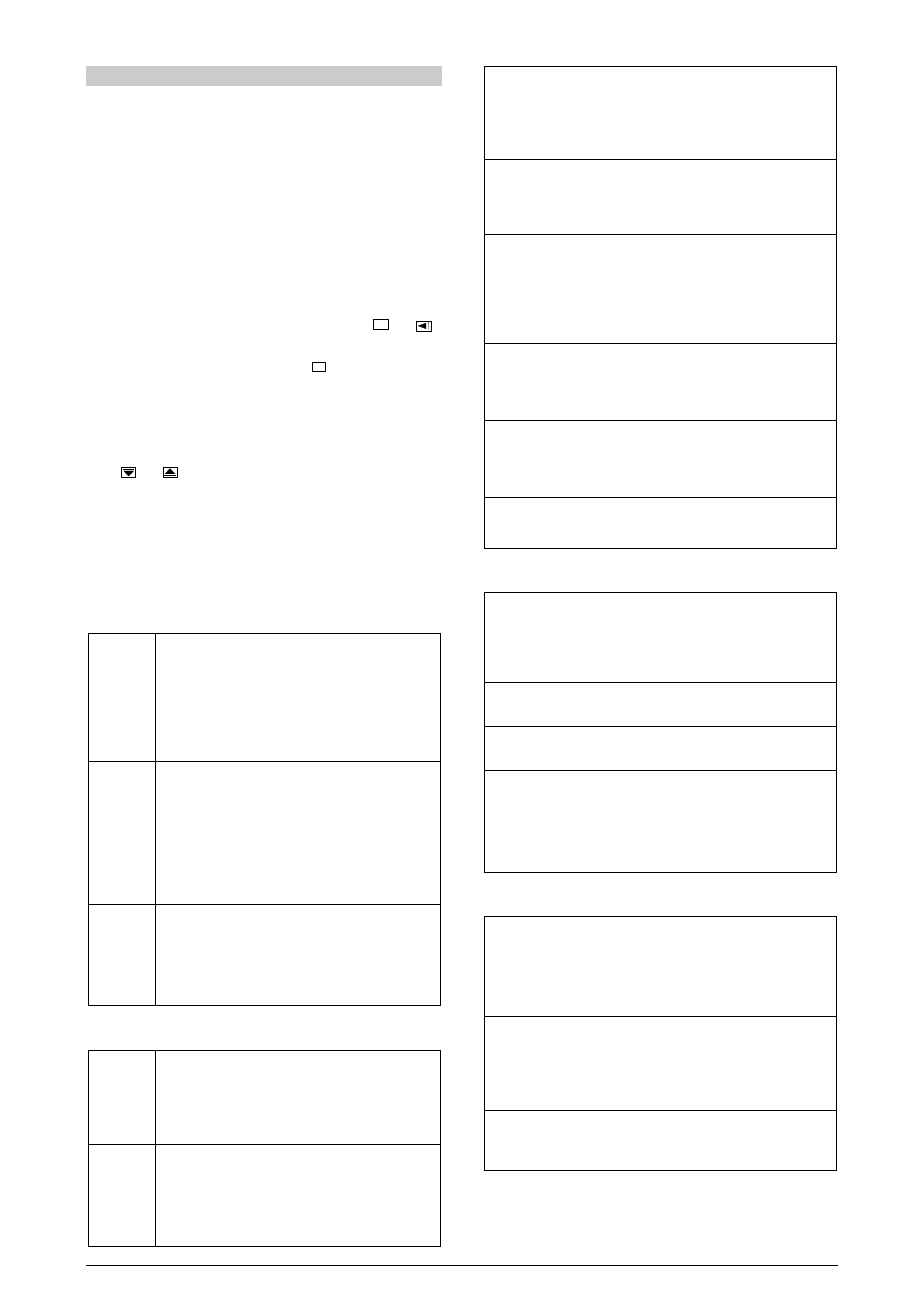
Controlador N960
NOVUS AUTOMATION
2/4
SET UP AND OPERATION
The controller must be configured before use. The user must assign
each parameter a condition presented as, for example, type of
temperature sensor (“TYPE”), required work temperature (“SP“),
temperature values for alarm triggering (“AISP”), etc.
PARAMETERS ORGANIZATION
The controller parameters are organized in six levels (parameter sets):
Operation / Tuning / Program / Alarm / Output / Calibration
When the controller is turned on, the Operation level is displayed and
remains activated during normal operation. The other levels can be
accessed when changes are required in the controller set up.
To access the other levels, press together the keys
P
and
.
When you reach the required level, which can be identified through
the first parameter shown, use the key
P
to access the other
parameters in this level. At the end of each level, the controller
returns to the Operation level, showing the process temperature.
When the keyboard is not activated for more than 20 seconds, the
controller returns to the Operation level, showing the process
temperature.
Using
and the operator is allowed to change the value of each
parameter shown.
Set up changes are saved in a protected memory and the controller
will use them as soon as the user passes to the next parameter or in
case no key is pressed within 20 seconds. This is not valid for the
RvN
parameter, whose setting changes are immediately taken by the
controller.
OPERATION LEVEL
TEMPERATURE
AND
SP
Temperature and SP Display: The upper display
shows the current measured temperature. The lower
display indicates the control SP value.
If the measured temperature exceeds the sensor
range limits or the input is open (broken sensor), the
screen will display “- - - -“. In hardware faults, the
screen will display “Er1”
Pr n
Program Execution: Determines the immediate
execution of the ramp and soak program elaborated
at the program level.
no
– does not run the program;
yes
– runs the program created;
When the control is enabled (run=yes) the selected
program will run immediately.
rVN
Run: In this screen it is possible to enable or disable
the controller action, turning on or off the alarm
control outputs.
0
– Does not enable outputs;
1
– Disable outputs.
TUNING LEVEL
ATVN
Auto-Tune: Enables the auto tune of PID
parameters.
0– Auto-tune disabled;
1
– Auto-tune enabled.
pb
Proportional Band: P parameter of the PID
control mode. Expressed as a percentage of the
maximum range of the type of sensor used.
Adjustable from 0 to 500 %.
To use the control mode ON/OFF, set zero (0).
ir
Integral Rate: Value of the integral parameter (I) of
the PID control mode. Expressed as repetitions per
minute. Adjustable from 0.00 to 55.20 repetitions per
minute. It is not displayed when the ON/OFF control
is selected (Pb=0).
dt
Derivative Time: Value of the derivative parameter
(D) of the PID control mode, in seconds. Adjustable
from 0 to 250 s. It is not displayed when the ON/OFF
control is selected (Pb=0).
(t
PWM Cycle Time: Value in seconds of the PWM of
the control output: Adjustable from 0.0 to 99.9
seconds. In processes that use power contactors, this
value must be higher than 10s. In process with solid
state relays, it is possible to use lower values. It is not
displayed if the ON/OFF control is selected (Pb=0).
kyst
Control Hysteresis: It is the ON/OFF control
hysteresis (programmed in a temperature unit). Used
only when the controller is set to ON/OFF control
(pb=0).
Act
Control Action:
rE
– Reverse Action usually used for heating.
dir
– Direct Action usually used for cooling.
Ai.sp
a2.sp
Alarm 1 and 2 Setpoints: Temperature values that
trigger alarm 1 and 2.
PROGRAM LEVEL
Ptol
Program Tolerance: Maximum deviation between
the program PV and SP. If it is exceeded, the
program is aborted (stops counting the time) until the
deviation falls within the tolerance range. Set zero to
disable this function.
Psp0
Psp7
Program SPs, 0 to 7 Set of 8 SP values that define
the ramp and soak program profile.
Pt1
Pt7
Program Segments Time, 1 to 7 Defines time, in
minutes, of each program segment.
Loop
Program Loop: Option for automatic restart of the
ramp and soak program.
yes
– Restart the program automatically.
No
– Does not restart the program
automatically.
CONFIGURATION LEVEL
Fva1
Fva2
Function of Alarm 1 and 2 Selects the function for
Alarms. See Table 2 for a description of functions
and their code, which will be programmed in this
screen.
oFF, iErr, Lo, xi, DiFL, DiFx, DiF
Bla1
bla2
Initial Alarm Blocking Initial alarm blocking function
for alarms 1 to 4.
YES
– enables the initial blocking
NO
– disables the initial blocking
xya1
xya2
Alarm Hysteresis: Defines the difference between
the temperature value that enables and the one that
disables the alarm.