Drive and motor connection, Motor terminal box connections, Motor thermistor connection – Beijer Electronics BFI-P2 V1.21 User Manual
Page 21
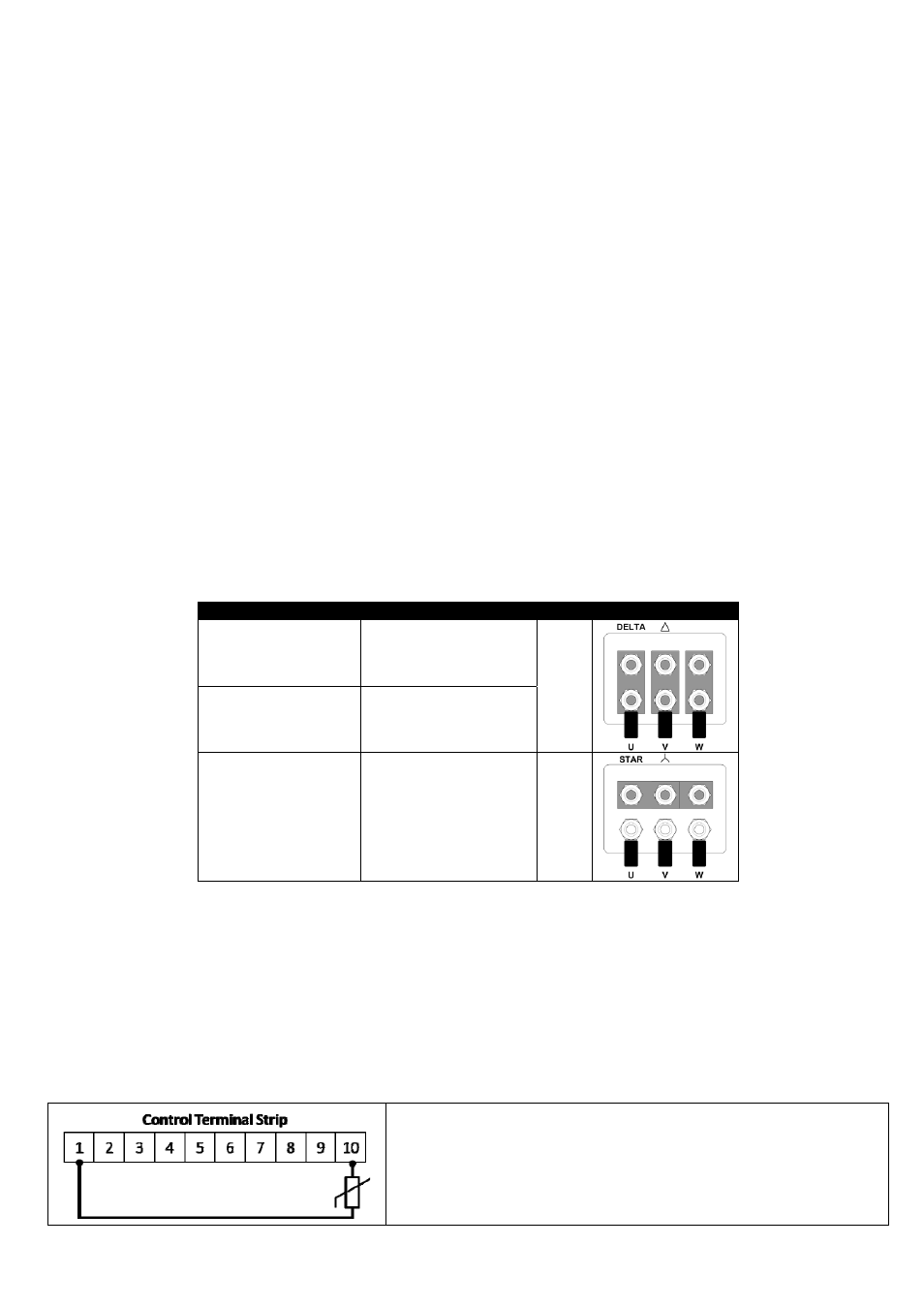
User Guide Revision 1.121
www.beijerelectronics.com
21
4.4. Operation of 3 Phase drives from a Single Phase Supply
A special function of Drive allows all drives designed for operation on 3 phase supplies to be operated on a single phase supply of the correct
rated voltage at up to 50% of the nominal capacity.
For Example, Model Number ODP‐2‐64450‐3KA4N can be operated on a single phase supply, 380 – 480 volts, with the maximum output current
limited to 45 Amps
The supply should be connected to the L1 and L2 terminals of the drive.
4.5. Drive and Motor Connection
•
The drive inherently produces fast switching of the output voltage (PWM) to the motor compared to the mains supply, for motors
which have been wound for operation with a variable speed drive then there is no preventative measures required, however if the
quality of insulation is unknown then the motor manufacturer should be consulted and preventative measures may be required.
•
The motor should be connected to the Drive U, V, and W terminals using a suitable 3 or 4 core cable. Where a 3 core cable is utilised,
with the shield operating as an earth conductor, the shield must have a cross sectional area at least equal to the phase conductors
when they are made from the same material. Where a 4 core cable is utilised, the earth conductor must be of at least equal cross
sectional area and manufactured from the same material as the phase conductors.
•
The motor earth must be connected to one of the Drive earth terminals.
•
For compliance with the European EMC directive, a suitable screened (shielded) cable should be used. Braided or twisted type
screened cable where the screen covers at least 85% of the cable surface area, designed with low impedance to HF signals are
recommended as a minimum. Installation within a suitable steel or copper tube is generally also acceptable.
•
The cable screen should be terminated at the motor end using an EMC type gland allowing connection to the motor body through the
largest possible surface area
•
Where drives are mounted in a steel control panel enclosure, the cable screen may be terminated directly to the control panel using a
suitable EMC clamp or gland, as close to the drive as possible.
•
For IP55 drives, connect the motor cable screen to the internal ground clamp
4.6. Motor Terminal Box Connections
Most general purpose motors are wound for operation on dual voltage supplies. This is indicated on the nameplate of the motor
This operational voltage is normally selected when installing the motor by selecting either STAR or DELTA connection. STAR always gives the
higher of the two voltage ratings.
Incoming Supply Voltage
Motor Nameplate Voltages
Connection
230
230 / 400
Delta
400
400 / 690
400
230 / 400
Star
4.7. Motor Thermistor Connection
4.7.1. Internal Thermal overload protection.
The drive has an in‐built motor thermal overload function; this is in the form of an “I.t‐trP” trip after delivering >100% of the value set in P1‐08
for a sustained period of time (e.g. 150% for 60 seconds).
4.7.2. Motor Thermistor Connection
Where a motor thermistor is to be used, it should be connected as follows:
Additional Information
•
Compatible Thermistor : PTC Type, 2.5kΩ trip level
•
Use a setting of P1‐13 that has Input 5 function as External Trip, e.g. P1‐13
= 6. Refer to section 7 for further details.