Programming, Typical counter applications – Red Lion GEMINI 2 User Manual
Page 3
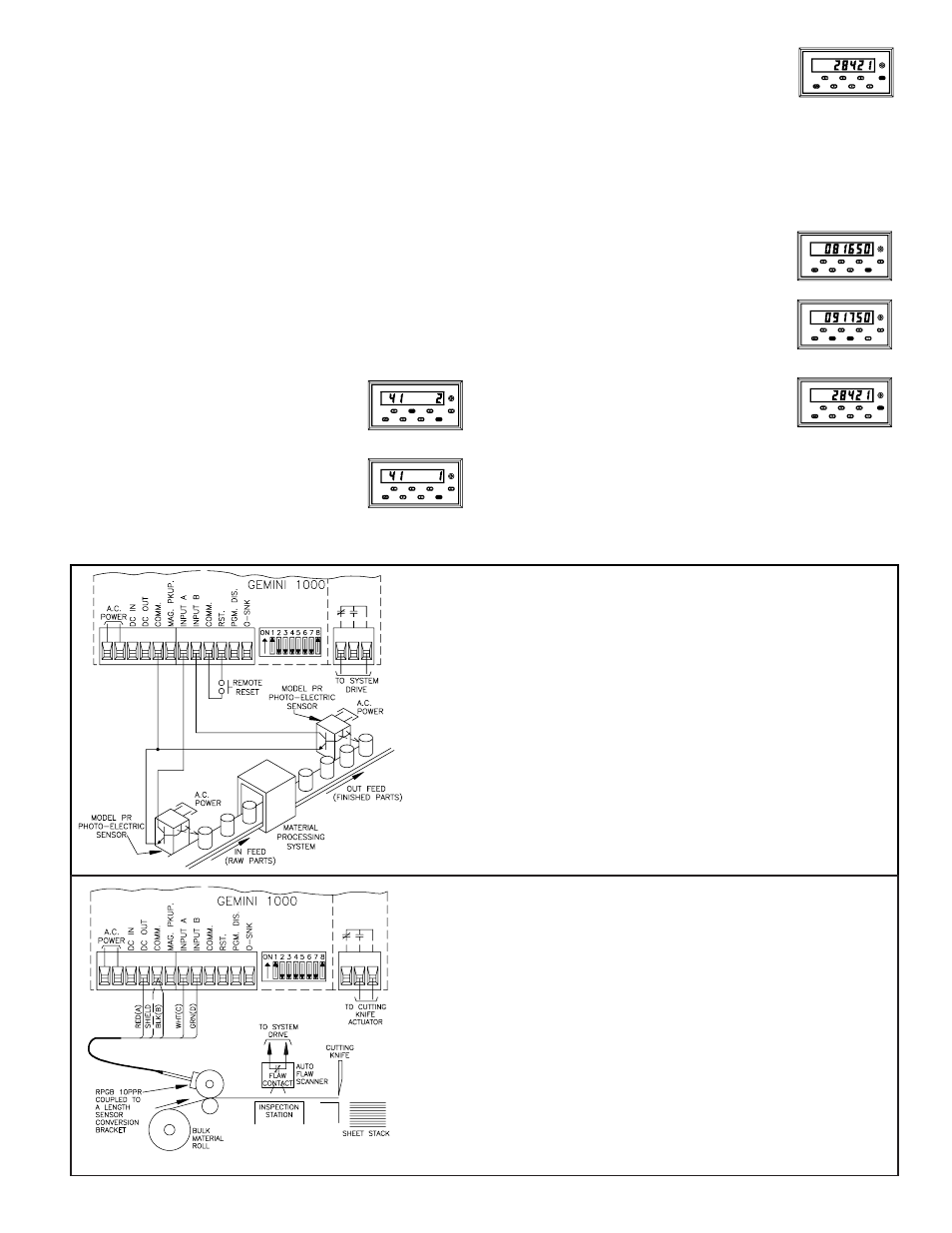
3
12. ENVIRONMENTAL CONDITIONS:
Operating Temperature: 0 to 50°C
Storage Temperature: -40 to 80°C
Operating and Storage Humidity: 85% max. relative humidity (non-
condensing) from 0 to 50°C.
Altitude: Up to 2000 meters
13. CONSTRUCTION:
Metal die-cast bezel, plastic case. This unit is rated for NEMA 4/IP65 indoor
use. Installation Category II, Pollution Degree 2
14. WEIGHT: 2.1 lbs. (0.9 kg)
PROGRAMMING
The Gemini 1000/2000 input circuit set-up is programmed using DIP
switches on the rear of the unit. All other functions are programmed through the
front panel pushbuttons.
To program or interrogate a function, the user first enters a two-digit function
code. The unit will then display that function code along with a single-digit
representing the present mode of operation. Programming changes are made by
changing the single-digit mode identifier.
EXAMPLE: The function code representing the “Unit Personality” is 41. The
mode identifiers for this function are:
Counter (1) and Rate Indicator (2).
To interrogate the Unit Personality, Press “41”:
Unit displays function code along with mode identifier
(Rate Indicator).
To change the Unit Personality to Counter mode,
Press “1”:
Unit displays the new mode identifier (Counter).
Press “E”:
Unit enters new mode and returns display to the present
count value.
The most commonly used functions, Preset(s) and Scale Factor, are initialized
through single front panel pushbuttons rather than a two-digit function code.
Pressing the “1” or “3” pushbuttons will immediately display the current Preset
or Scale Factor value for the selected display. To change any digit, the user
presses the pushbutton directly below that particular digit, which is then scrolled
until the desired value is obtained. Each digit is changed, if necessary, in the
same manner until the complete Preset or Scale Factor value is registered on the
display. Pressing the “E” pushbutton completes the entry sequence.
To interrogate the Preset value, Press “1”:
Unit displays current Preset value.
To change the Preset value:
Any digit may be changed by pressing the pushbutton
directly below it. Release the pushbutton when the digit
reaches the desired value.
Press “E”:
Unit enters new Preset value and returns display to the
present count.
“IN PROCESS” MONITORING SYSTEM
Some applications require continuous monitoring of items “in-process”. In this example, a
material processing system is equipped with an in-feed photo-electric scanner to count raw parts
going into the system, and an out-feed scanner to count finished parts leaving the machine. The
number of parts between the in-feed and out-feed is displayed by the GEMINI 1000 operating
in the Anti-Coincidence Add/Subtract mode. In this mode, counts applied to INPUT A are
added while counts applied to INPUT B are subtracted.
Before start-up, the system is completely empty of parts and the counter is reset to zero.
When the operation begins, raw parts move through the in-feed scanner field of view with each
part generating an “up” count. After processing, finished parts appearing at the out-feed scanner
generate “down” counts so the counter continuously displays the number of “in-process” parts.
The GEMINI 1000 preset value is set to the maximum system capacity and the output is used
to control power to the system drive. Therefore, if a jam-up occurs within the system and the
maximum capacity is reached, the counter output will shut down the system drive until the
problem can be corrected.
Conversely, the counter could be used in the Reset-to-Preset mode which delivers an output
at zero. If the supply of raw parts is interrupted, the system will eventually empty and the
counter will reach zero. At this point, the counter output will shut down the system drive until
the supply of raw parts is replenished.
TYPICAL COUNTER APPLICATIONS
“CUT-TO-LENGTH” WITH FLAW DETECTION
In this application, sheets of material are to be cut to length as per customer order with any
flaws being corrected by the vendor. Sales are both domestic and foreign and require lengths to
be measured in either yards or meters.
A rotary pulse generator (RPG) with a 10 pulse/revolution (PPR) quadrature output is
coupled to a length sensor conversion bracket with a 4/10 yard wheel. The GEMINI 1000 is set
up in the Quadrature x4 mode which effectively increases the RPG output to 40 PPR. With the
4/10 yard wheel, the information rate becomes 100 pulses/yard and allows the material to be cut
to the nearest 1/100 yard. The counter display is programmed for two decimal places to provide
a readout in 1/100 yard increments.
The Preset value on the GEMINI 1000 is set to the desired length of material and the output
is used to control power to the cutting knife. The counter is programmed to automatically reset
to zero at the preset value which allows the process to run continuously without losing counts.
If a flaw is detected, a contact in the flaw detector is used to shut down power to the system
drive allowing the material to be “backed-up” to the point at which the flaw occurred. As the
material is rewound, the counter will count “down” to maintain a readout of the total length of
material “in-process”.For metric orders, the scale factor on the GEMINI 1000 is set to 0.9144
which provides the conversion from yards to meters (1 yard = 0.9144 meters). Otherwise, all
equipment and settings remain as above.