BMR Suspension TAS011 User Manual
Page 12
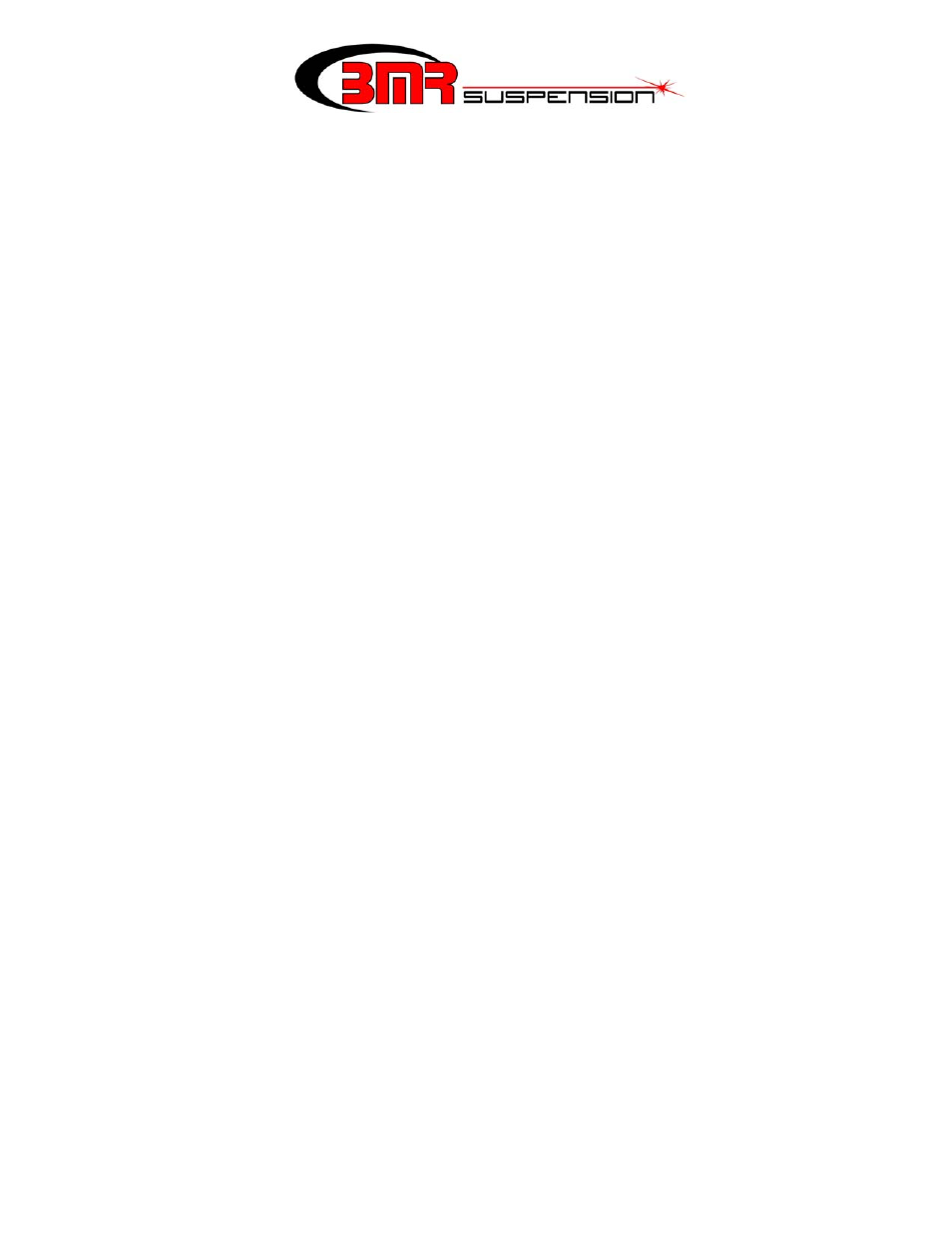
12
(CONTINUED)
11) Driveline angle. For quiet operation and long u-joint life, driveline angle should not
exceed 2-3 degrees negative. The following step involves setting the driveline angle.
While this process is actually very simple, it is difficult to explain so we have provided
detailed instructions and examples below. Driveline angle is the difference between the
pinion angle and the driveshaft angle. Zero degrees means there is no angle and the
pinion and driveshaft are straight as viewed from the side. If the angle is negative, the
driveshaft and the rear-end will form a “V”. If it is positive, the driveshaft and rear-end
will form an “upside down V”.
To check the angle, begin by placing the supplied angle finder onto the rear Watts
link mounting plate and record your reading. Take your reading from the drivers’ side of
the car. Since the Watts link mounting plate is 90 degrees perpendicular to the pinion,
this angle represents the angle of the pinion gear minus 90 degrees. Now place the
angle finder on the top of the driveshaft and record the reading from the drivers’ side of
the car. This angle represents the driveshaft angle. The goal angle to reach is a 2-3
degree difference between the two recorded angles. For example, our test car used for
these
instructions
had
the following readings:
The rear angle on the Watts link mounting plate was 88 degrees. You need to
subtract 90 degrees from this to get your pinion angle, resulting in -2. The driveshaft
angle just happened to be at 0 degrees. The difference between these two angles is -2,
right where we want to be. If your resulting angle is anywhere between 0 and -3, it is an
acceptable angle. To adjust this angle, begin by loosening the three cross-bolts at the rear
of the torque arm. Do not remove them, they only need to be loosened enough to allow
the rear end to be pivoted up or down. Using a pry-bar between the third member and the
torque arm, adjust the pinion until the proper angle is achieved. Re-tighten the cross-
bolts to 80 ft/lbs.
3. Shock settings. An entire book could be written on this subject but we will just touch on
the basics. Your AFCO shocks have adjustments for both compression and rebound. It
is important to understand that a shocks job is to control the motions of the spring. For
optimal control, you never want the spring to collapse or extend too fast. Determining
those settings will be different for everybody since vehicle corner weights, desired ride
quality, driving behavior, etc. play a role in finding what is optimal for that individual. It
is generally best to start with softer settings and work your way up. The idea is to keep
the tire firmly planted to the asphalt. Too much of either adjustment will not only create
a harsh ride but will force the tires to bounce and lose traction during aggressive driving.
The following recommendations are very basic and intended for street driving. Begin
with the compression settings at full soft and the rebound settings 2-4 clicks from zero.
Drive the car over varying road conditions and work your way up to a setting that feels
firm yet still comfortable without excessive bounce over road irregularities. Once the
rebound is set, begin adjusting the compression until ride quality begins to suffer then
back a click or two. These settings should provide good all-around handling and ride
quality, further adjustment may be necessary for very aggressive driving habits such as
road course and autocross racing.
4.
Roll Center (Watts Link Height). Roll center (RC) works in conjunction with the
vehicles center-of-gravity (CG) height. Front RC also plays a role in determining an optimal rear