BMR Suspension AA033 User Manual
BMR Suspension For the car
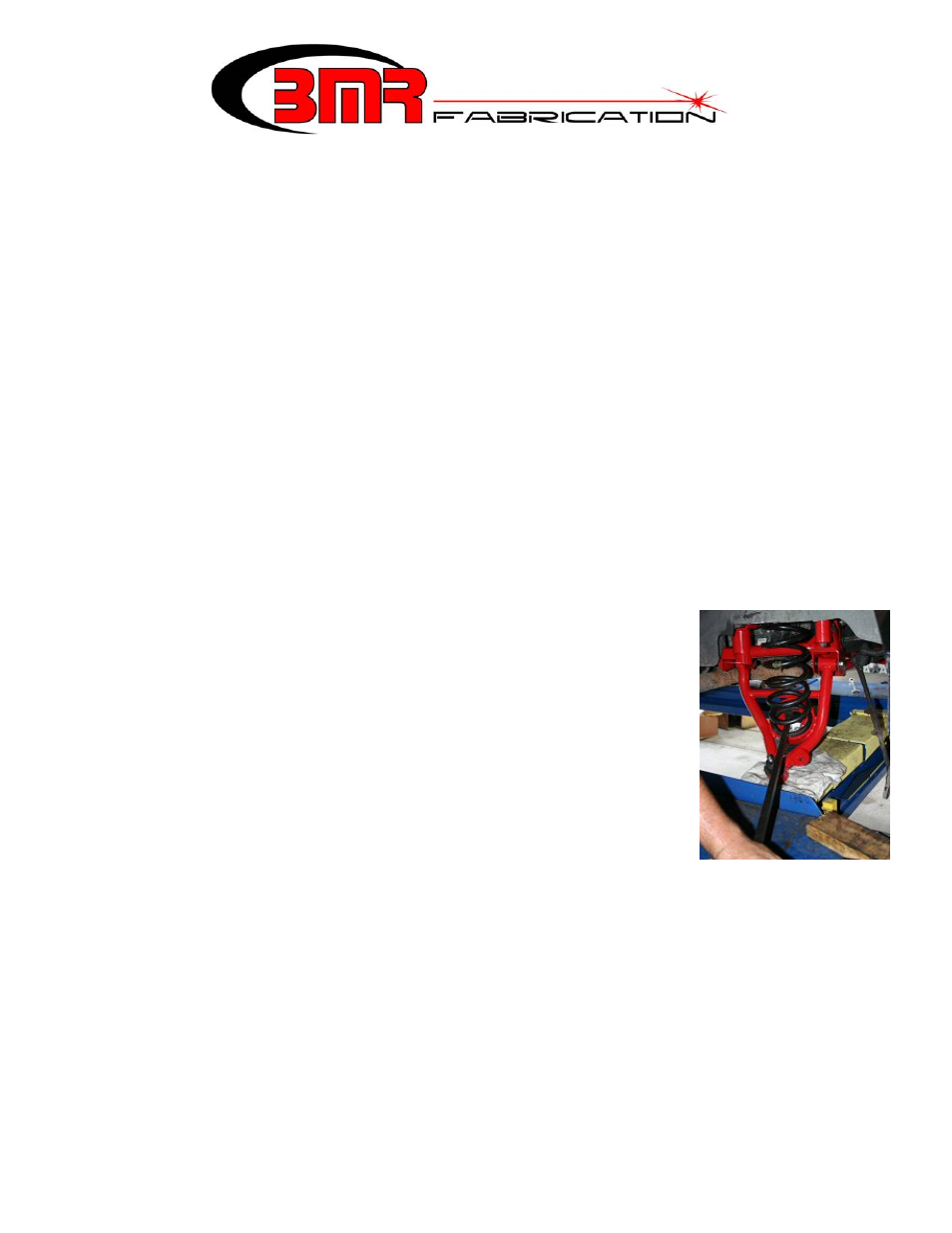
BMR A-ARM INSTALLATION INSTRUCTIONS FOR GENERAL MOTORS TYPE SUSPENSIONS
NOTE: This installation is recommended for experienced installers only. Improper spring removal techniques can result in
serious injury or death. If you are unfamiliar with any portion of this installation, consult a reputable alignment shop.
LOWER A-ARMS
1. Lift vehicle and support with jack stands under the frame locations. Remove wheels and tires.
2. Begin with one side of the vehicle. Remove the two caliper bolts and slide the caliper off the rotor. Leaving the brake line
connected, tie the caliper up out of the way using a bungee cord or zip tie.
3. Remove the cotter pin from the outer tie rod end where it attaches to the spindle. Loosen the castle nut and remove it. Using
a brass hammer, hit the spindle around the tie rod mounting hole until the tie rod breaks loose. Lower the tie rod out of the
way.
4. Loosen the shock upper mounting nut and remove the bushing and washer. Loosen the two lower shock bolts and remove the
shock through the bottom of the A-arm.
5. Locate the outer swaybar end link where it attaches to the A-arm. Remove the end link mounting bolts from the A-arm.
NOTE: An inside spring compressor is the recommended tool for removing coil springs. Disregard steps 6-8 if you are using a spring
compressor.
6. Turn the spindle in one direction to gain access to the castle nut of the lower ball joint. Remove the cotter pin and loosen the
castle nut but DO NOT remove it. Using a brass hammer, hit the spindle around the ball joint mounting hole until the ball
joint pops loose. A pickle fork may also be used for loosening the ball joint.
7. Position a floor jack under the A-arm and lift the A-arm until there is no spring tension on the ball joint. Remove the castle
nut.
8. Carefully lower the A-arm as far as it will go. Using a pry-bar, carefully pop the spring out of the spring pocket and set it
aside.
9. Loosen and remove both A-arm mounting bolts and remove the lower A-arm.
10. Lightly sand or wire wheel the bushing surfaces inside the frame to remove all dirt and
scale. Once cleaned, apply supplied grease to both inner sides of the mounting points.
11. Identify the proper side BMR A-arm replacement by comparing the swaybar and bump-
stop locations with the OE arms. Apply grease to the outside mating surfaces of the BMR
A-arm bushings but do not fill the grease fittings until the installation is complete. Mount
the A-arms to the frame but do not tighten. NOTE: BMR A-arms use polyurethane
bushings that are much more resistant to flex than rubber. This resistance may make it
necessary to tap the A-arms into place using a rubber mallet.
12. Disregard this step if using a spring compressor. Swing the A-arm up and position a
hydraulic jack underneath the A-arm. Lift the spring up and position it onto the upper
spring pocket, allowing the bottom of the spring to rest on the A-arm pocket. Using a long
pry-bar, pry the spring until it pops into position in the spring pocket. NOTE: It may be
necessary to lift the A-arm in order to get the spring pocket at the correct angle for the
spring to pop into place. With the spring in position, the end of the spring should butt up
against the stop in the spring cup.
13. Once the spring is seated properly in the cup, carefully lift the A-arm until the ball joint seats into the spindle. Install the
castle nut and tighten. Insert a new cotter pin.
14. Re-install shock.
15. Re-connect the outer tie rod end to the spindle. Install a new cotter pin.
16. Re-install the caliper.
17. Repeat steps 2-16 for the other side.
18. To reconnect the swaybar, it is necessary to have the suspension loaded. The simplest way to do this is to drive the vehicle
onto ramps. Install the wheels and tires
19. With the suspension loaded, tighten the lower control arm bushings. NOTE: the vehicles weight must be on the suspension
before tightening the control arm bolts. Failure to do so will result in improper bushing preload causing irregular ride
height and accelerated bushing wear.
20. Re-install the swaybar end links. Tighten the bolt until the bushings just start to bulge.
21. Insert 5-6 pumps of grease into the lower ball joint. Insert 3-4 pumps of grease into each control arm bushing.
22. Lower vehicle.
PAGE 1