Dwyer ULTM User Manual
Page 4
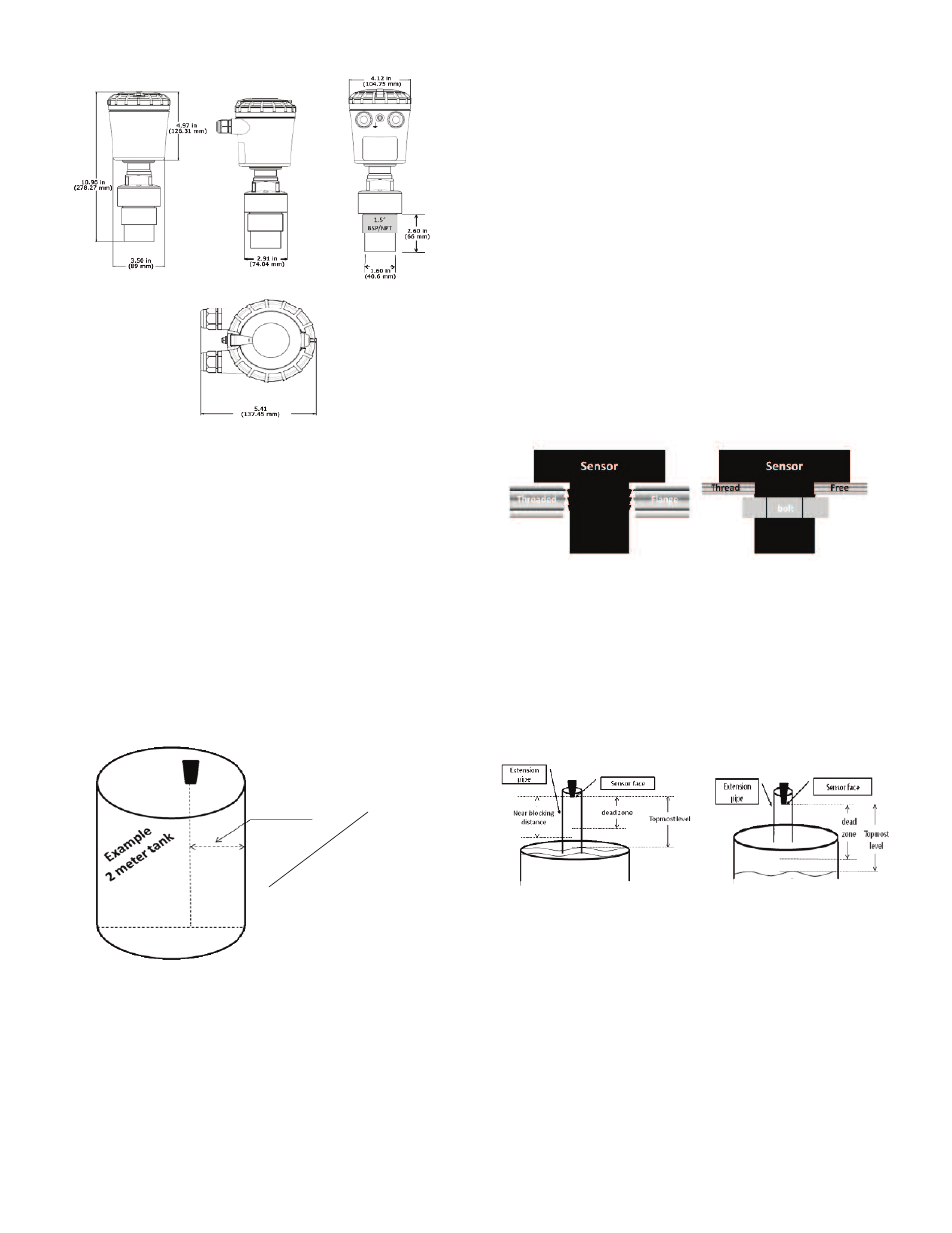
Chapter 2. Physical and Electrical Installation Guidelines
This chapter is a list of guidelines for proper physical installation of the Series ULTM
on tanks, including electrical connections. In the final section of this chapter, there
is a short and concise list of instructions–the “Must-Be pamphlet”. Always ensure
that the Series ULTM is installed in an area that meets the stated ratings of this
product including temperature and technical specifications.
1. Physical Guidelines
• ULTM systems are installed above the target (e.g. water, fuel) being measured
and should not make contact with the target at any time. Typically, the unit is
installed on top of a tank through a hole on the roof of the
tank. In outdoor applications, the ULTM may be attached to a metal arm
extending above the target attached nearby.
• Series ULTM should be located as far as possible from vertical tank walls and
from other physical obstructions such as filling inlets. Keep a minimum gap of: 12
in (30 cm) plus 4 in (10 cm) for each 3.3 ft (1 m) of measurement range.
• For best results, place the unit away from sources of acoustic noise or
sources of vibrations.
• Series ULTM should be perpendicular to the surface of a liquid target. The angular
displacement should be less than 5° from the vertical axis.
• Proper physical installation is accompanied by software setup. Setup includes
defining parameters such as tank height, and may include additional parameters
such as Near Blocking Distance (NBD), Far Blocking Distance (FBD), False echo
scan and more. For additional information refer to the section in Chapter 8
reference guide: “Application Dimensions and Constraints” (p.14).
2. Tank Fitting
Series ULTM is equipped with a 1.5˝ BSP or 1.5˝ NPT thread allowing for two fitting
options: direct fitting in a threaded flange, or fastened with a 1.5˝ BSP / 1.5˝ NPT
nut through a thread-free flange.
For outdoor installations, use a stable arm and firmly attach the sensor to the arm
using a through-hole and threaded nut. Alternatively, it may be possible to attach
the sensor to a threaded hole which is built-in the arm.
Always verify thread compatibility between the Series ULTM and flange or nut. Do
not use excessive force when using threads. Preferably, tighten by hand only. If a
wrench is used, grip Series ULTM at the wrench grip surfaces only (see Figure 1
Series ULTM parts) and exert light force.
3. Dead Zone
Refer to Chapter 8 reference guide: “Application Dimensions and Constraints”
(p.14). A gap must be kept between the face of sensor and the topmost level of the
target. This gap must be at least the size of the specified “dead zone”. If the target
level passes the dead zone, measurements may be unpredictable. Therefore, it is
recommended to keep a marginal gap between the expected topmost level and the
dead zone border. In the case where the top most level is too close to the tank roof,
an extension pipe is required for the installation of the unit as described below.
4. Extension Pipe
Refer to Chapter 8 reference guide: “Application Dimensions and Constraints”
(p.14). An extension pipe is required for installation where the top most target level
is too close to the roof of the tank. In such cases, an extension pipe is installed on
the tank and the sensor is installed on top of the extension pipe at a safe distance
from the top most level of the target. The lower border of the dead zone may fall
inside the tank as seen in the right hand side of the figure below. In this case no
further software settings are required. The lower border of the dead zone may also
fall within the extension pipe as described in the left hand side of the figure below.
In such cases, the Near Blocking Distance (NBD) should be configured in the
software.
Page 3
Figure 2: Series ULTM Dimensions.
Figure 3: Minimum Gap.
Figure 4: Threaded Flange (left) Thread-Free Flange (right).
Figure 5: Possible Extension Pipe Fittings.
Mi
nim
um
of
12
˝ (
30
cm
)
4˝(
10
cm
) p
er
ea
ch
m
ete
r
To
tal
of
17
.72
˝ (
45
cm
)