SANDPIPER M1F Non-Metallic User Manual
Page 21
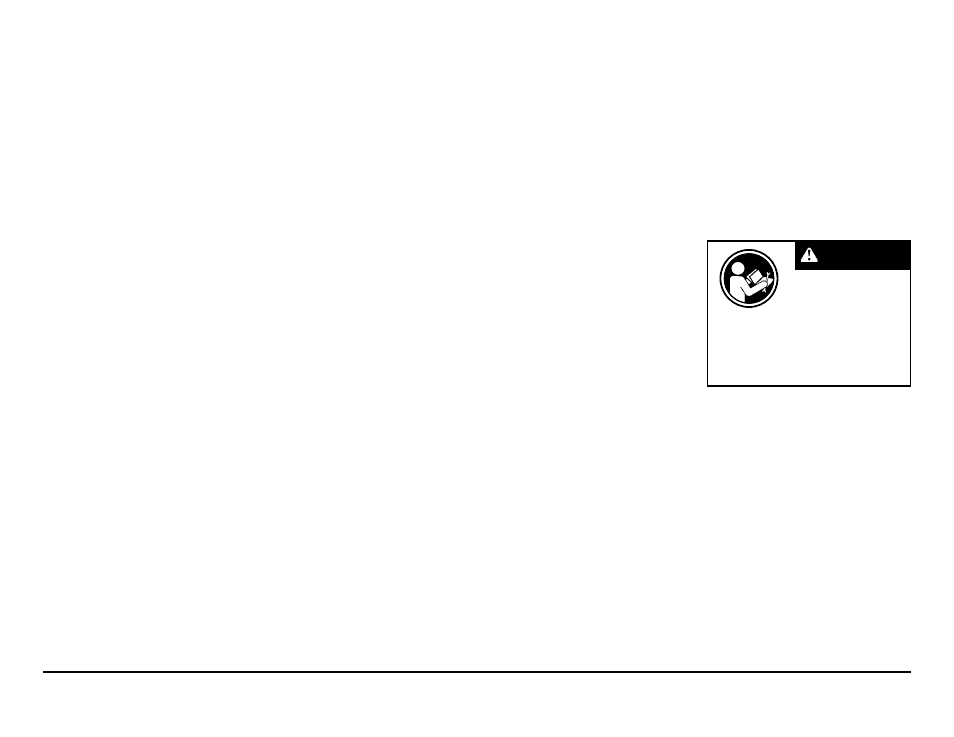
m1fnmdl3sm-rev0713
Model M1F Non-Metallic Page 19
OPTION FOR TPE EQUIPPED
PUMPS CONCEPT
The spill containment option
prevents the air end components from
being contaminated or damaged when
a pumping diaphragm ruptures while
pumping caustic or toxic materials. It
also helps to protect the environment.
With the installation of optional leak
detectors (either mechanical or
electronic) the diaphragm rupture can
be detected. The pump can then be
shut down and repaired before any
caustic or toxic materials can enter
the air end and be exhausted into the
surrounding environment.
OPTION DIAPHRAGM SERVICING
To service the diaphragms first
shut off the suction, then shut off the
discharge lines to the pump. Next shut
off the compressed air supply, bleed
the pressure from the pump, and
disconnect the air supply line from the
pump. Drain any remaining pumped
liquid from the pump. Remove the pump
before servicing.
Next, drain the fluid from the spill
prevention chambers. This can be done
by removing the bottom plug (item 50)
from each spill prevention chamber.
After the fluid from the spill prevention
chambers has been drained, the wet
end components can now be removed.
See diaphragm servicing section
for detailed instructions. The spill
prevention option has two additional
TPE pumping diaphragms (item 55).
These diaphragms are installed with
the natural
concave curve toward
the outer chamber (items 15 from the
pump assembly drawing). The molded
directional arrows on the diaphragms
must point vertically.
FILLING CHAMBERS WITH LIQUID
THE CHAMBERS ARE FILLED
WITH WATER AT THE FACTORY.
If you prefer to substitute another
liquid, to prevent system contamination
consult the factory first to determine
compatibility of the substitute with
pump construction.
Follow the steps listed here to
replace the liquid in the pump after
disassembly or liquid loss:
1. Drain the fluid in the spill
prevention chambers by removing
the bottom two boss plugs (items 50).
Replace the bottom two boss plugs
after the fluid is drained.
2. Remove the eight capscrews
(item 10) fastening the discharge
manifold and elbows to the outer
chambers (items 15). The discharge
manifolds and elbows can now be
removed.
3. Remove the top two boss
plugs (items 50). The spill prevention
chambers are filled through the
exposed ports.
4. Apply air pressure to the air
distribution valve. Install safety clip
(item 1-K) into the smaller unthreaded
hole in one end cap (item 1-E). This
locks the valve spool to one side,
keeping the pump from shifting.
5. Face the side of the pump with
the installed safety clip. If the safety clip
is installed in the top end cap, fill the left
spill prevention chamber. If the safety
clip is installed on the bottom end cap,
fill the right spill prevention chamber.
6. Loosely reinstall one boss plug
(item 50) to the filled spill prevention
chamber.
7. Shut off air supply. Remove safety
clip. Adjust the air line regulator so that
air pressure slowly fills the pump. The
diaphragm expands, forcing the fluid
in the chamber to be slowly displaced.
When the pump shifts to the opposite
side, quickly install the safety clip.
8. Loosen the top boss plug on the
filled chambers. This allows fluid in the
chamber to purge trapped air from the
chamber. This can be seen by watching
the column of fluid in the sight tube.
When fluid appears at the top of the
port, quickly tighten the boss plug. Fluid
loss of 1 to 2ml is acceptable.
9. Tilt the pump so the uppermost
pipe tee (item 52) is in the vertical
position. Loosen the pipe plug (item
49). This will allow trapped air to
purge through the pipe tee. When fluid
appears at the tee opening, reinstall
the pipe plug.
NOTE: If all air is not purged using
this procedure, remove the check valve
components from the top port of the
outer chamber (item 15). Apply manual
pressure to the pumping diaphragm by
inserting a blunt instrument into the top
port of the outer chamber and applying
pressure to the diaphragm. Loosen the
pipe plug (item 49) allowing the fluid
to purge any remaining trapped air.
Reinstall the plug.
10. Repeat steps 5 through 9 to fill
opposite spill prevention chamber.
11. Reinstall the check valve
components, discharge manifold and
elbows to the pump. The pump is now
ready for operation.
Read these instructions
completely, before
installation and start-up.
It is the responsibility
of the purchaser to retain this manual
for reference. Failure to comply with the
recommendations stated in this manual
will damage the pump, and void factory
warranty.
IMPORTANT