I nstallation, Electrode and work connections, A-17 – Lincoln Electric IM10022 POWER WAVE AC_DC 1000 SD User Manual
Page 26
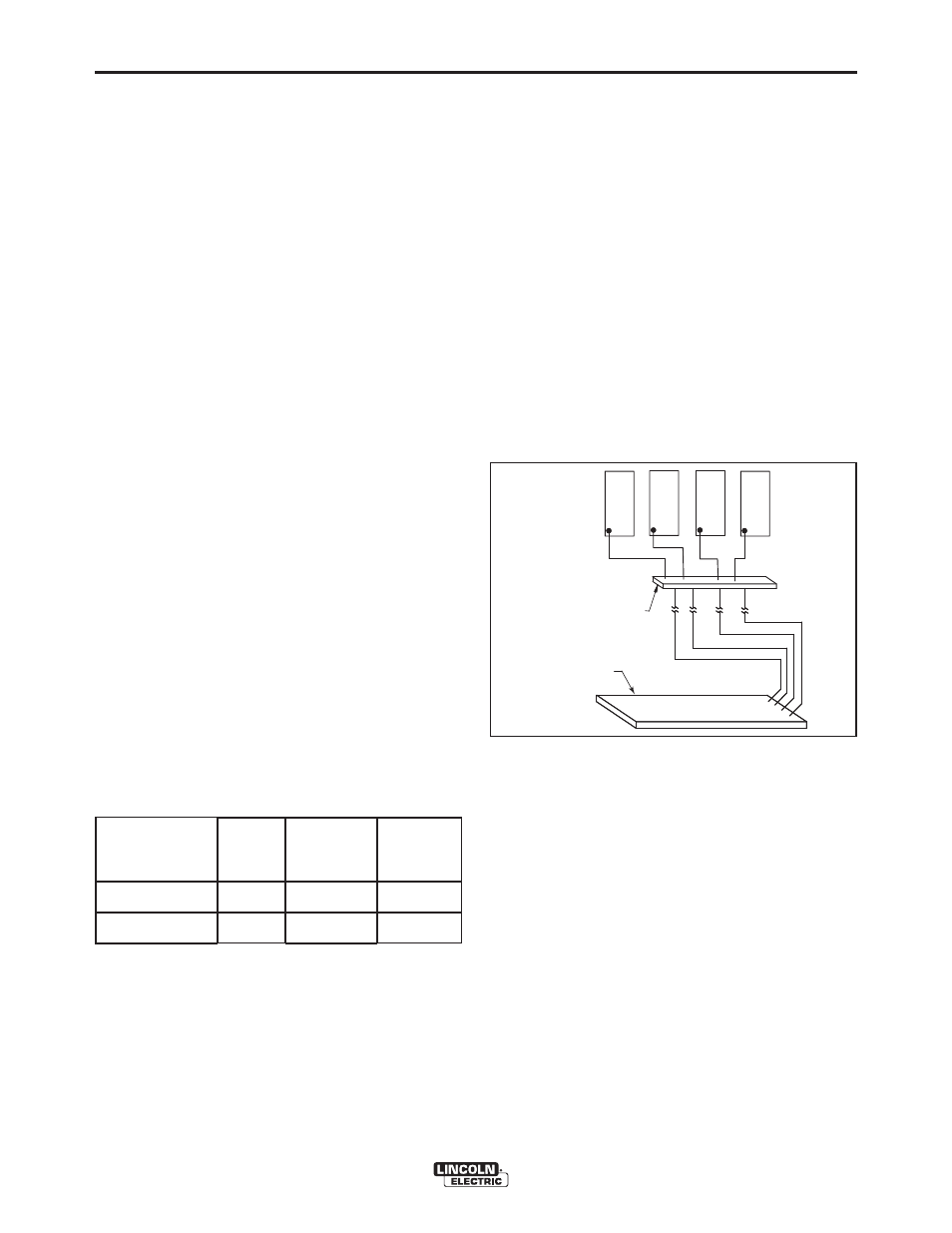
A-17
INSTALLATION
POWER WAVE
®
AC/DC 1000
®
SD
A-17
ELECTRODE AND WORK
CONNECTIONS
General Guidelines
The unique switching structure of the Power Wave
®
AC/DC 1000
®
SD allows it to produce DC positive, DC
negative or AC output waveforms without reposition-
ing the work and electrode leads. Additionally, no DIP
switch changes are required to switch between the dif-
ferent polarities. All of this is controlled internally by
the Power Wave
®
AC/DC 1000 SD, and based exclu-
sively on the weld mode selection.
The following recommendations apply to all output
polarities and weld modes:
• Select the appropriate size cables per the
"Output Cable Guidelines" below. Excessive volt-
age drops caused by undersized welding cables
and poor connections often result in unsatisfactory
welding performance. Always use the largest weld-
ing cables (electrode and work) that are practical,
and be sure all connections are clean and tight.
Note: Excessive heat in the weld circuit indicates
undersized cables and/or bad connections.
• Route all cables directly to the work and wire
feeder, avoid excessive lengths and do not coil
excess cable. Route the electrode and work cables
in close proximity to one another to minimize the
loop area and therefore the inductance of the weld
circuit.
• Always weld in a direction away from the work
(ground) connection.
TABLE A.1 - Output Cable Guidelines
Electrode Connections
Connect cable(s) of sufficient size and length (Per
Table A.1) to the "ELECTRODE" studs on the power
source (located behind the cover plate on the lower
right rear corner). Connect the other end of the elec-
trode cable(s) to the tab of the contact nozzle. Be sure
the connection to the nozzle makes tight metal-to-
metal electrical contact.
Work Connections
Connect cable(s) of sufficient size and length (Per
Table A.1) between the "WORK" studs (located
behind the cover on the lower left rear corner) and the
work piece. Be sure the connection to the work makes
tight metal-to-metal electrical contact.
NOTE: For parallel and/or multiple arc applications
with excessive ground path lengths, a com-
mon work connection bus should be used. The
common work connection serves to minimize
voltage drops associated with resistive losses
in the ground paths. It should be made out of
copper, and located as close as possible to
the power sources (See Figure A.10).
Total Cable Length
ft (m)
Electrode and Work
Combined
0 (0) to 250 (76.2)
0 (0) to 250 (76.2)
Duty Cycle
80%
100%
Number of
Parallel Cables
2
3
Cable Size
Copper
4/0 (120 mm
2
)
3/0 (95 mm
2
)
WORK PIECE
COMMON CONNECTION
(LOCAT ED CLOSE TO
POWER SOURCES)
FIGURE A.10