Warner Electric ER 825 and 1225 Normal Duty User Manual
Page 6
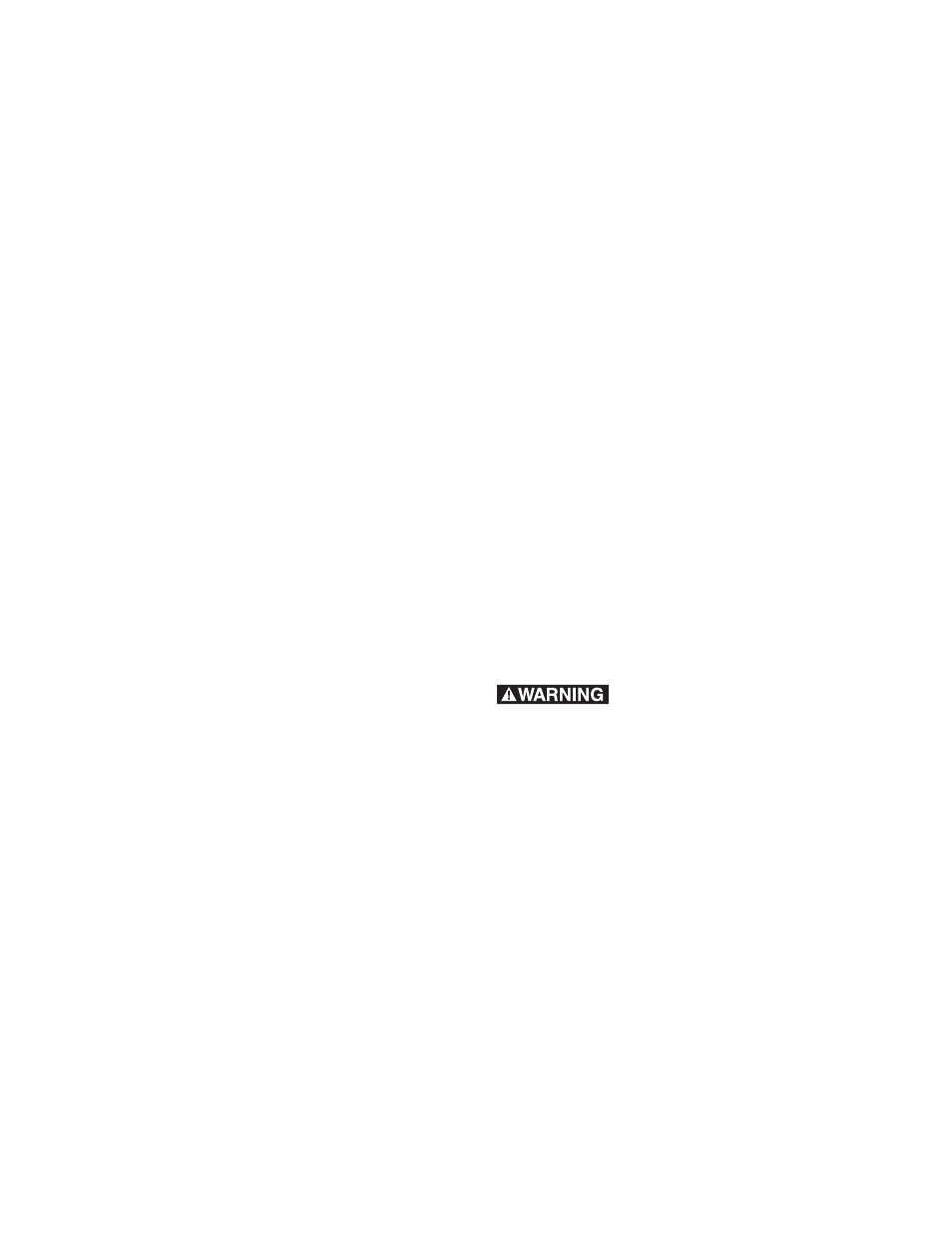
A. 115 VAC supply to terminals 1 and 4. Jumpers
to connect terminal 1 with terminal 2 and
terminal 3 with terminal 4. Recommended fuse
is 3/4A slow blow.
or:
230 VAC supply to terminals 1 and 4.
Jumper to connect terminal 2 with terminal 3.
Recommended fuse is 3/4A slow blow.
B. A chassis ground should be provided as a
non-current conducting ground wire (color
coded green).
C. Switching. Follow instructions per control
models listed.
MCS-805-1 Standard Control Operation
1. For switching DC side: Switch connected to
terminals 7 and 8. Switch open will allow brake
to be engaged. Switch closed will enable the
release of the brake.
2. For switching AC side: Line power off will allow
brake to be engaged. Line power on will
release brake. A jumper connection must be
made between 7 and 8.
3. Slower brake actuation will result when
switching the AC side.
MCS-805-2 Two Step Control Operation
1. With switch connected to terminals 7 and 8
and switch is open with AC power applied,
brake will be partial engaged.
2. With switch connected to terminals 7 and 8
and switch is closed with AC power applied,
brake will be fully released.
3. With switch connected to terminals 7 and 8
and switch closed with AC power removed,
brake will be fully engaged.
D. ER brakes are polarity sensitive. Connect the
plus terminal of the brake to terminal 6 on the
control and the minus terminal of the brake to
terminal 5 on the control.
6
Warner Electric • 800-825-9050
P-250 • 819-0122
Step 7:
Apply power to the brake and remove
shims. Note: It may be required at this point to
adjust voltage to brake, to release the armature
and remove shims. Set the airgap by pressing
the armature into contact with the magnet and
then releasing. The armature should spring back
approximately 1/32-3/64 (.031-.045) inch. If the
airgap is outside of that range, reposition the
armature hub assembly by procedure Section IV
and steps 4 and 5 of the assembly procedure
Section I.
Note: If armature does not spring back proceed
to voltage adjust procedure.
Step 8: Brake Release Voltage Adjustment. When
setting the brake power supply, the objective is
to achieve armature release by adjusting the coil
voltage so it counteracts the permanent magnet
to the maximum extent possible.
Two different release procedures are used,
depending on whether an ER-825 or ER-1225 is
involved. For ER-825 brakes, follow the
procedures outlined in Step 9 below. For ER-
1225 brakes, follow the procedures outlined in
Step 10.
Step 9: For ER-825 Brakes
Put machine in a safe condition
so that when voltage is applied to control and
switch closures are made the brake does not
rotate and machine does not run.
Step 9A:
Attach multimeter to brake to monitor DC
voltage observing proper procedure for hookup
of multimeter per manufacturing instruction.
Step 9B:
Apply power to control and close switch
connections that allow DC voltage from control
to be applied to brake.
Step 9C:
Depending on variable control used and
output channel that brake is hooked up to, turn
voltage adjust knob or screw, counter-clockwise
to 0VDC, at this point slowly increase voltage
control clockwise until brake armature
disengages. (Releases) Record this voltage,
continue to increase voltage until brake
armature engages.