Warner Electric ER 825 and 1225 Normal Duty User Manual
Page 4
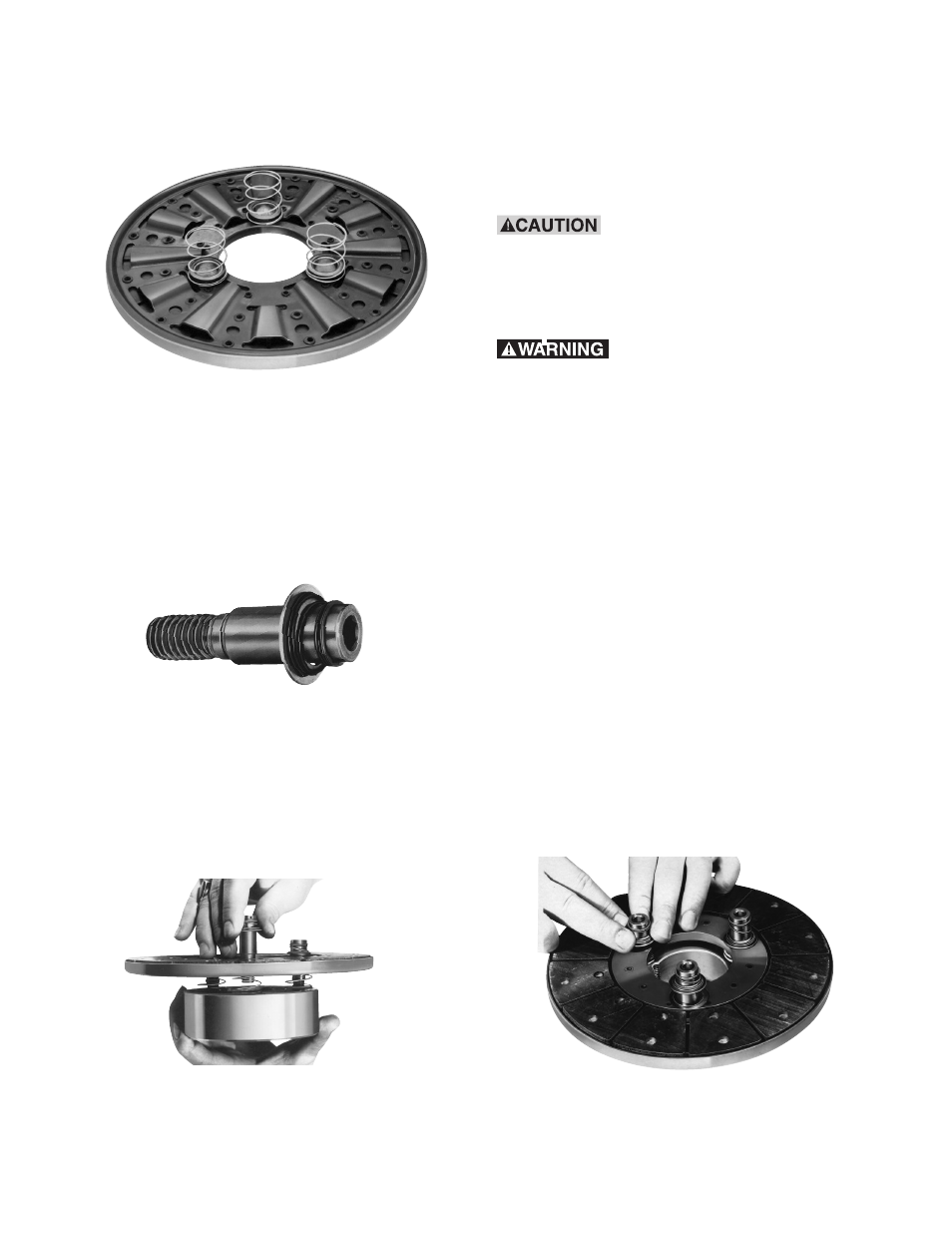
4
Warner Electric • 800-825-9050
P-250 • 819-0122
Step 3B: Compress each heavy spring (red) by
sliding each detent spring and retainer toward
the pin heads.
Figure 2
Step 3C: Insert the assembled drive pins with
springs compressed through the armature,
through the white springs and into threaded
holes in the armature hub. Keep the armature
segments oriented away from the hub and the
armature hub tapered bore oriented to open
away from the armature.
Figure 3
Step 3D: Draw the drive pins up tightly until the
pin shoulder is against the hub face (threads
are class 3 and may seem to bind).
CAUTION: Be sure the straight white springs do
not get caught under the drive pin shoulder.
Figure 4
Step 3E: Compress the armature against the hub
face and slide each detent spring retainer
against the armature face.
NOTE: Do not disturb this position during com-
pletion of assembly.
.062 inch thick steel shims are
recommended for shim stock selection. Do
not use shims thicker than .125 inch or you
will shorten brake life by reducing available
armature travel.
Shim stock must be clean and
free of any contamination (oil, grease). Keep
fingers clear of the area between the magnet
and the armature as the armature will be
pulled sharply toward the magnet after the
gap is closed to approximately 1/2 inch.
Step 4: Place three steel shims 120 degrees apart
on the magnet as shown in Figure 3. Insert the
taper-lock bushing (Figure 3, item 5) into the hub
(Figure 3, item 2).
Slip the armature hub assembly onto the brake
shaft until armature makes contact with shims.
Step 5: Using an allen wrench, tighten the hub
bushing screws alternately and evenly until tight.
The airgap between armature and magnet must
be .062 to .125 inch. If the airgap is outside of
that range, reposition the armature hub assembly
by repeating steps 1 and 2 of the disassembly
procedure and steps 4 and 5 of the assembly
procedure.
Figure 5