KB Electronics KBAC-48 User Manual
Page 22
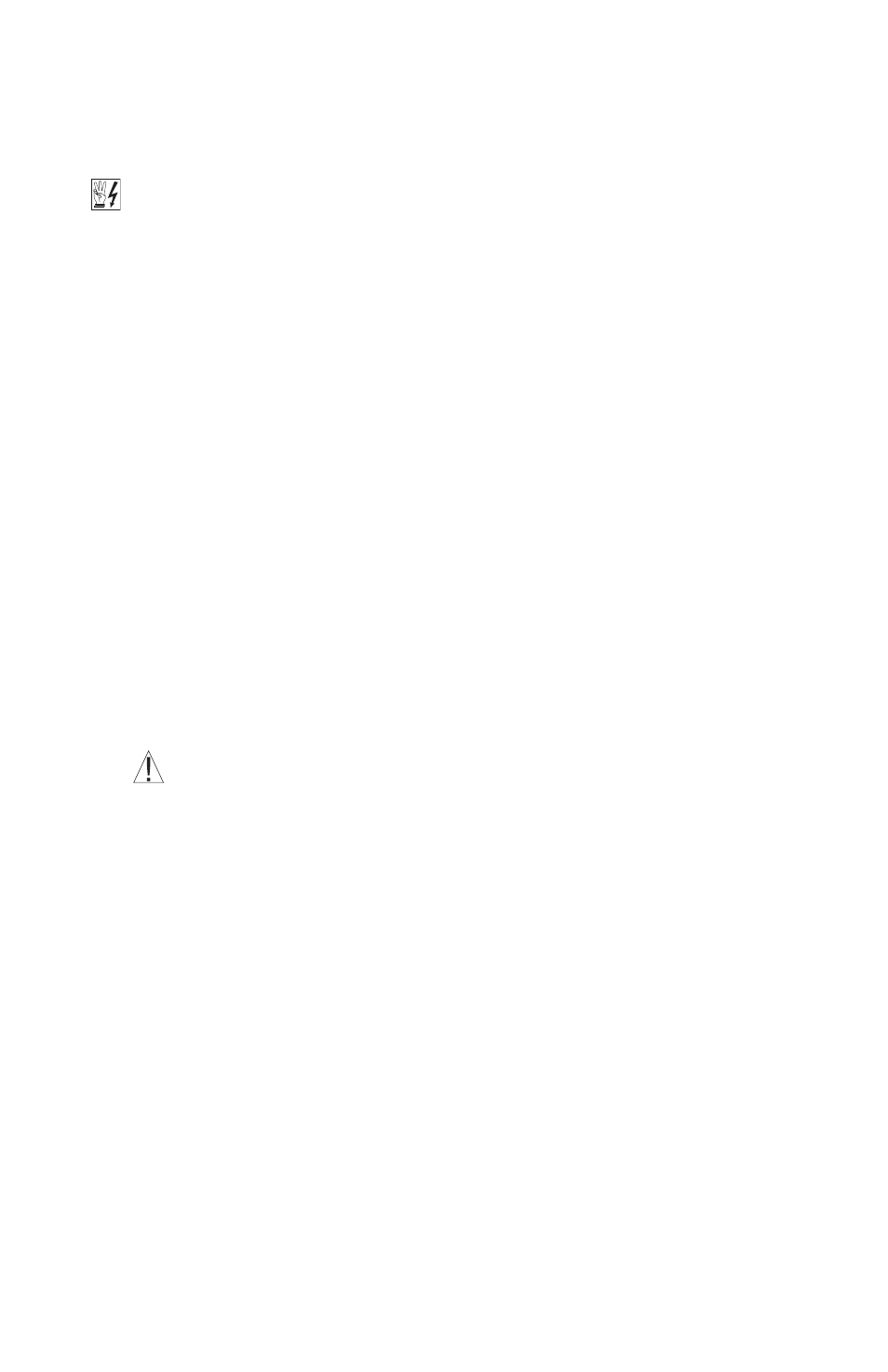
22
8 RECOMMENDED HIGH VOLTAGE DIELECTRIC WITHSTAND TESTING (HI-POT TESTING)
Testing agencies such as UL, CSA, VDE, etc., usually require that equipment undergo a hi-pot test. In order
to prevent catastrophic damage to the drive which has been installed in the equipment, the following
procedure is recommended. A typical hi-pot test setup is shown in Figure 29 on page 21. All drives have
been factory hi-pot tested in accordance with UL requirements.
WARNING! All equipment AC line inputs must be disconnected from the AC power.
8.1 Connect all equipment AC power input lines together and connect them to the H.V. lead of the hi-
pot tester. Connect the RETURN lead of the hi-pot tester to the frame on which the drive and other
auxiliary equipment are mounted.
8.2 The hi-pot tester must have an automatic ramp-up to the test voltage and an automatic ramp-
down to zero voltage.
Note: If the hi-pot tester does not have automatic ramping, then the hi-pot output must be manually
increased to the test voltage and then manually reduced to zero. This procedure must be followed for
each machine to be tested. A suggested hi-pot tester is Slaughter Model 2550.
CAUTION! Instantly applying the hi-pot voltage will cause irreversible damage to the drive, which
will void the warranty.
9 RECONDITIONING THE BUS CAPACITORS
If this drive has been in storage for over one year it is necessary to recondition the power supply bus
capacitors. To recondition the bus capacitors, apply the AC Line, with the drive in the Stop Mode, for a
minimum of one hour. Not following this procedure will cause the bus capacitors to fail.
10 DRIVE OPERATION
10.1 Start-Up Procedure – After the drive has been properly setup (jumpers and trimpots set to the
desired positions) and wiring completed, the start-up procedure can begin. If the AC power has
been properly brought to the drive, the power (PWR) LED will illuminate green. The status (ST) LED
will indicate drive status, as described in Section 12.2 on page 23.
To start the drive, momentarily set the Start/Stop Switch to the “START” position. The motor will
begin to accelerate to the set speed.
WARNING! Using a jumper to eliminate the start/stop function will cause the motor to run at
the Main Speed Potentiometer setting when the AC line is applied. See Section 10.2.
Note: If the motor rotates in the incorrect direction, it will be necessary to disconnect the AC line, reverse
any two motor leads, and repeat the start-up procedure.
10.2 Restarting the Drive After a Fault has been Cleared
1,2
– The drive monitors four faults:
Undervoltage, Overvoltage, Short Circuit at the motor (phase-to-phase), and Overload. See Section
12.2 on page 23 for the Status (ST) LED indication. Also see Section 6.3 on page 18 for Automatic
Ride-Through or Manual Restart selection with Jumper J3.
To restart the drive after a fault has been cleared, use the Start/Stop Switch
2,3
.
If the Start/Stop Switch has been eliminated (bypassed), see Section 5.6 on page 16.
4
The drive
can be restarted (after the fault has been cleared) by disconnecting the AC power, and all LEDs are
no longer illuminated, and then reconnecting the AC power.
Notes: 1. For an Overload Fault, be sure the fault has been cleared before restarting the drive. Check the
motor current with an AC RMS responding ammeter. Also, the CL setting may be set too low. See Section
13.7 on page 25. 2. For an Overvoltage Fault, if the drive is set for Automatic Ride-Through, the drive will
automatically restart when the AC line voltage returns to below the specified Overvoltage Trip Point. 3.
If the Forward-Stop-Reverse Switch has been installed, it can be used to restart the drive. 4. If the Start/
Stop Switch has been eliminated (bypassed), the AC line must be used to restart the drive after an
Overload Fault has been cleared.
11 AC LINE FUSING
The drive does not contain line fuses. Most electrical codes require that each ungrounded conductor
contain circuit protection. Do not fuse neutral or ground connections. It is recommended to install