Ransburg, Micropak - operation, Determining if a di/dt overload occurred – Ransburg MicroPak LECU5004 User Manual
Page 19: Voltage boost mode, Voltage regulation, Current regulation
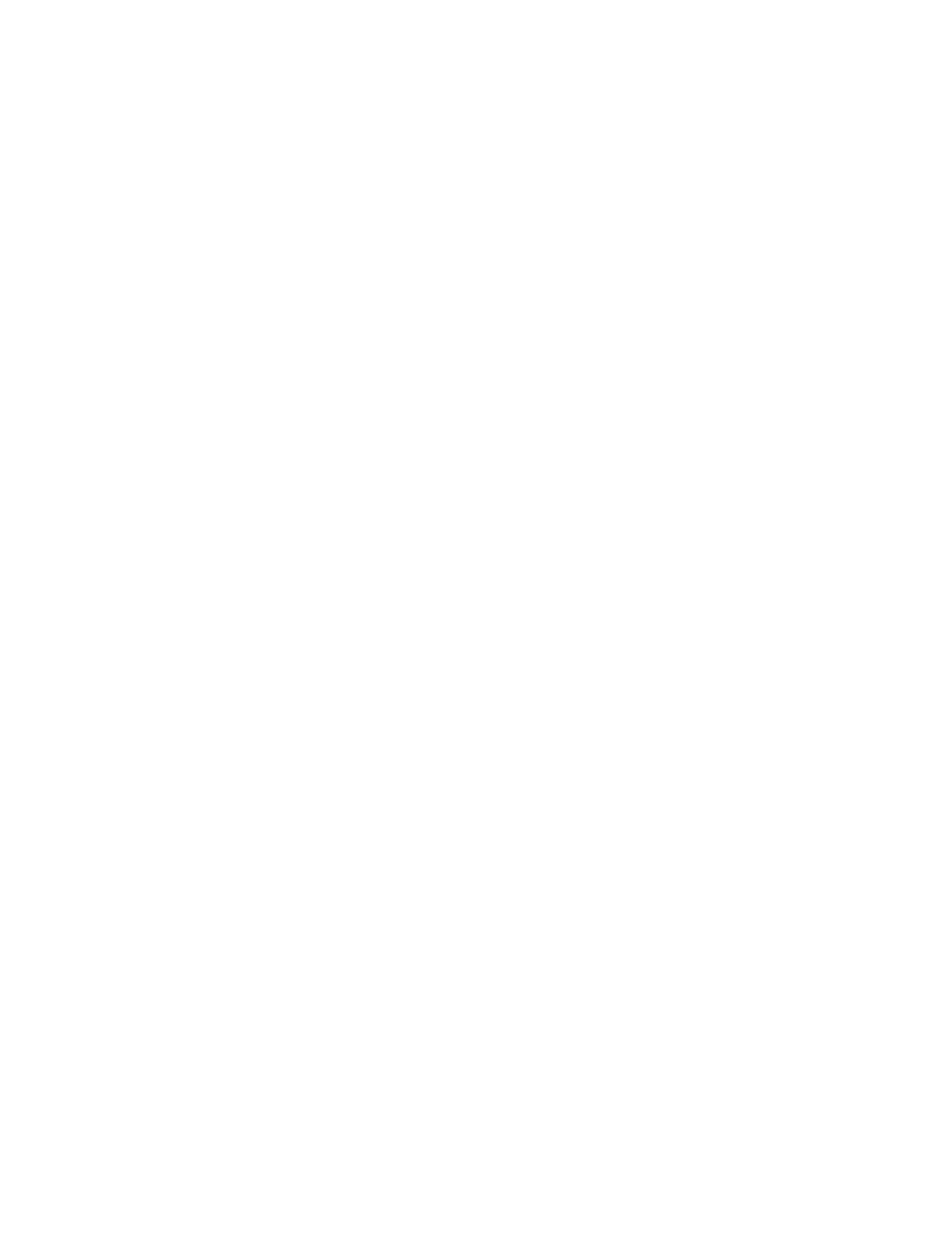
MicroPak - Operation
Ransburg
16
LN-9218-00.13
To Read the Di/dt Setting
Push the “SET” push-button twice within one
second. The kV display will read “SLP” and the
µA display will indicate a number between 0 and
9. This number represents different levels of di/
dt sensitivity with 0 being most sensitive. If the
“SET” push-button is not pressed again, the µA
display will automatically return to normal output
current display.
To Adjust the Di/dt Value
Local Mode
Once a di/dt sensitivity level is displayed, it can
be changed by pressing the “SET” button again
and holding in. The sensitivity level will increment
slowly. Once the desired level is displayed (0-9),
then release the “SET” button. The new value is
stored in memory when the “SET” push-button is
released. This setting should be set as sensitive
as possible (smallest di/dt value) without nuisance
overloads occurring. This should be done with
paint loaded and normal production parts present.
Remote Mode
In remote mode, the above sensitivity levels are
set by the numbers 0 to 9 in a Block Transfer
Write (BTW) similiar to the method for setting the
setpoint for kV. The BTW information is shown
in the “MicroPak Node Adapter PLC/IO” in the
“Operation” section.
The di/dt sensitivity level in Minimized Remote
Mode (Remote mode where SW3-1 is in OFF
position) will still be set as in Local mode. In this
mode, the kV setpoint is still remote, and the µA
setpoint is still from internal pot R21.
The di/dt function can be inhibited when needed
during the application process to avoid nuisance
shutdown. To understand the details of using
this feature with either the Discrete I/O Module
or Serial Node Adapter, reference the appropriate
I/O tables further back in this Operation section.
Determining if a Di/dt
Overload Occurred
The “OVER” LED (overload) will flash on and off if
a di/dt caused an overload, otherwise the “OVER”
LED will stay on continuously if a fixed current
overload occurred. This will help determine the
type of high voltage fault that occurred.
Voltage Boost Mode
The MicroPak software has been revised to provide
two voltage correction modes when configured for
the HP404 cascade. The purpose of this change
is to compensate for the voltage drop in the cas-
cade’s current limiting resistor.
Position 1 (see Figure 6), voltage correction 1
mode, provides correction when the output current
is always below 50 µA. Position 2 (see Figure 6),
voltage correction 2 mode is the default mode and
provides correction when the output current runs
or may range above 50 µA.
Voltage Regulation
To date, the most common type of output regulation
for electrostatic painting applications is voltage
regulation. This means sensing the output volt-
age, comparing this to the voltage setpoint, and
adjusting the cascade drive to maintain the output
equal to the setpoint. In this mode the current
varies, depending on the load, up to the Current
Setpoint where the unit switches to Over Current,
turning off the output.
Current Regulation
The MicroPak is also capable of current regu-
lation which is desired for some applications. In
this mode the functions of voltage and current are
reversed from the voltage regulation mode. This
means sensing the output current, comparing this
to the current setpoint, and adjusting the cascade
drive to maintain the current output equal to the
current setpoint. In this mode the voltage varies,