Maintenance, Inspecting/cleaning the flue passages, Replacing a servomotor and related components – Fulton Vantage (VTG) Fully Condensing Hydronic Boiler User Manual
Page 59
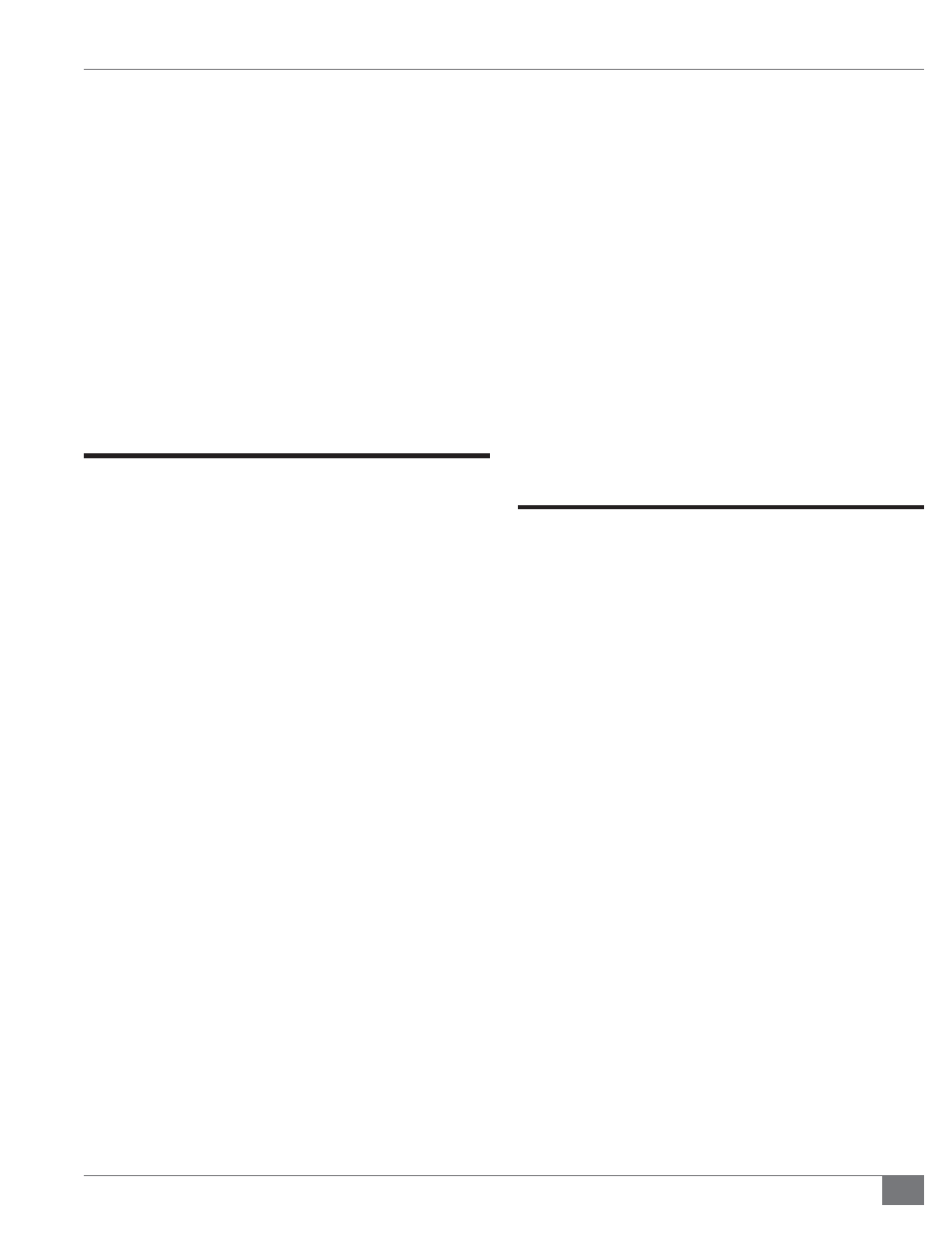
Questions? Call (315) 298-5121, or visit us online at www.fulton.com
SECTION 4
VTG-IOM-2013-0815
MAINTENANCE
4-7
5. Evenly tighten all bolts on the lower door to 23 ft/lbs
(31.2 NM) in a criss-cross pattern. See Figure 15a and
Figure 15b. Do not over torque, as this can result in
damaging of the door seal.
6. Do not replace any of the bolts, nuts, washers, gaskets or
other boiler components without consulting the factory.
Any replacement components must be to factory
specifi cations.
7. Once all bolts are tightened to proper torque, replace
the boiler jacket panels.
8. To
confi rm proper seal on the door after this procedure
has been conducted, ensure there are no fl ue gases
present around the boiler once unit is running.
Inspecting/Cleaning the Flue Passages
For boilers fi ring on Natural Gas or Propane, there is no need
to inspect the fl ue passages of the boiler unless the technician
suspects damage or malfunction.
Boilers Firing on #2 Oil, B100 Bio-Diesel, Digester
Gases or Any Other Substance Besides Natural
Gas or Propane
Inspect the duplex stainless steel fl ue passages every 4,000
hours of operation (not including hours operating on Natural
Gas or Propane). This is the bottom section of the heat
exchanger and will not require removal of the burner or fuel
train.
Procedure for Accessing the Duplex Stainless
Steel Flue Passages (all models)
1. Lock out the power supply to the boiler and isolate the
fuels supplied to the unit.
2. Remove the front lower jacket panel from the boiler.
3. Remove the fl ue passage cover and turbulators.
4. If deemed necessary, clean the fl ue passages with the
proper equipment, such as round wire brushes and a
wet/dry shop vacuum or soot vacuum system.
5. Insert the turbulators back into position.
6. Reinstall the fl ue passage cover. Confi rm torque to 23 ft/
lbs (31.2 NM) on all bolts. Do not replace any bolts, nuts,
washers or other components without consulting the
factory.
7. Restore power to the unit and restore fuel to the unit.
8. Fire the boiler and set combustion to proper levels.
9. To
confi rm proper seal on the door after this procedure
has been conducted, ensure there are no fl ue gases
present around the boiler once unit is running.
10. If evidence of extensive soot, scaling or corrosion is
present in the duplex stainless steel fl ue passages, this
may indicate that removal of the burner and cleaning
of the furnace and upper fl ue passages is required.
Please contact Fulton’s service department for more
information and instructions, as requirements vary by
model and burner selection.
Replacing a Servomotor and Related
Components
If it is determined that a servomotor needs replacement or
you are experiencing reliability issues with the servomotor
assembly, Fulton recommends installing a Siemens Servo
Gas and Butterfl y Valve Assembly. This assembly includes the
gas butterfl y valve, bracket, coupling and servo assembly.
Replacing this entire assembly may not be appropriate for all
applications, thus the servo motors are available individually
as well. The installing technician must verify that the bracket
allows for proper alignment and that the coupling to shaft
connections are secured adequately.
If it is determined that a servomotor needs replacement,
adhere to the following:
1. Verify the model number of the new servomotor is the
same as the old servo motor. The model number starts
with the letters SQM and is displayed on a label on the
side of the motor. Proceed only after model number is
verifi ed.
2. Turn power to the boiler off .
3. Turn
off all electricity to the boiler.
4. Remove the cover on the servomotor to be changed.
5. Remove the green wiring plugs and the conduit
termination point from the motor by pulling them
towards you. A black grounding wire runs from the
motor to the conduit termination point. Pull it off from
the conduit termination point. Also note the location of
the jumper on the left side of the motor.